Hired-Hand Emergency Back-Up and Alarms: Secondary Sensing System Expansion User Manual
Page 16
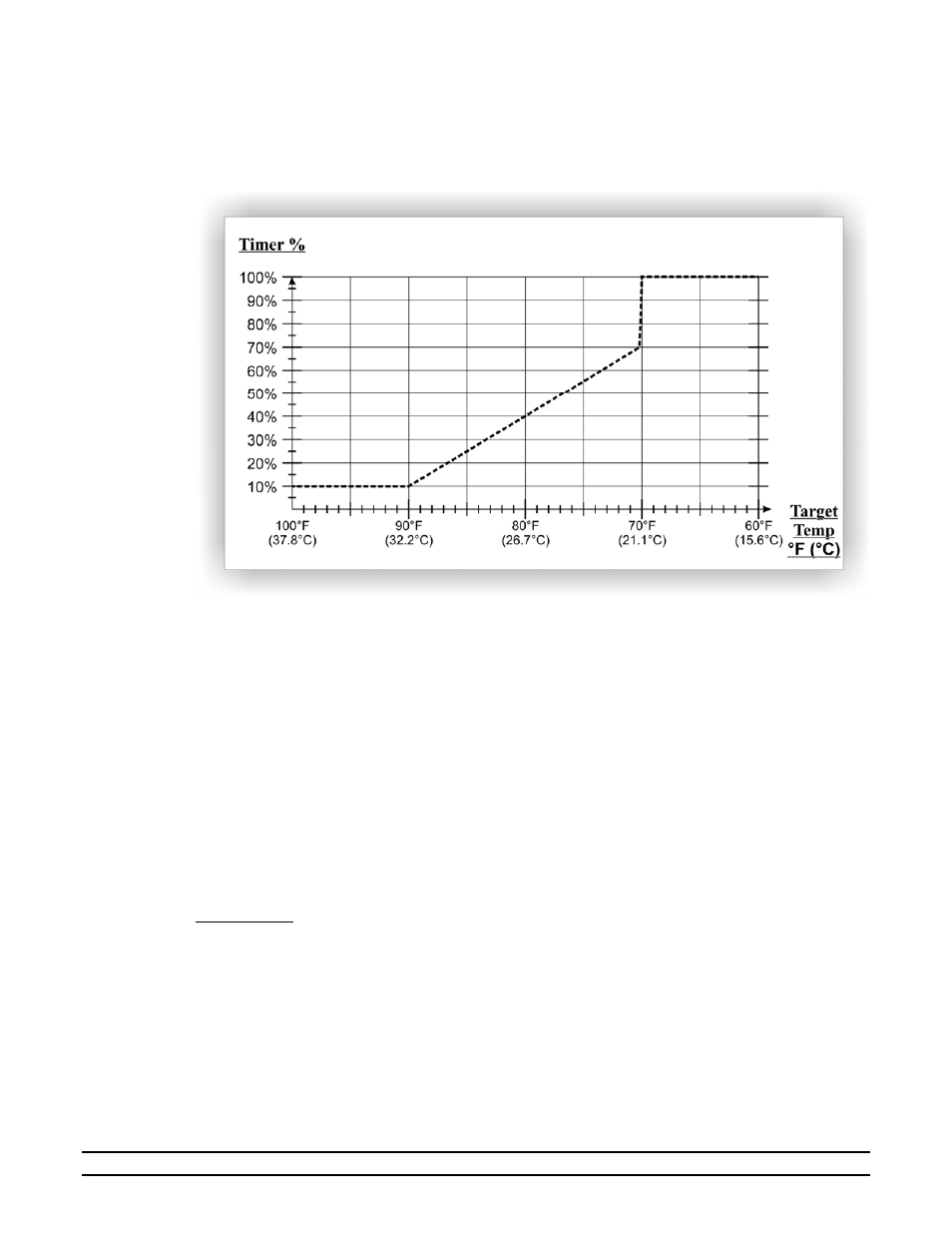
Manual No. 4801-3001 Rev 7-08
Secondary Sensing System Expansion
16 of 46
P3 – Back-Up Timer Percentage
This determines the percentage that COOL 1 will be run in an Emergency condition for minimum
ventilation. (10% to 100%). The timer is a five minute timer.
A new timer percentage curve feature (added in version V0.09 and later software) automatically
changes the timer percentage based on the Target Temperature.
The data and table below shows an example:
The table and graph above is representative of the curve. The curve actually has multiple points as the
Target Temperature changes in between these points. The Emergency Back-Up Timer Percentage is
not user selectable although you can view the current timer percentage by going to Program Mode and
displaying P3. As you can see by the table, once the Target Temperature gets to 70 F (21.1 C) or less,
the timer fan will run 100% of the time. In other words, Cool 1 will always run in the event that the
main controller is lost or has a problem operating its timer fans. Timer percentages in between 70 –
100% are not implemented because frequent on-off transitions are very hard on single phase AC
motors.
P4 – Back-Up Stage On Delay
This determines the number of seconds that the S
3
will wait before turning Stages ON during power
loss (10 to 60 seconds). This feature is designed to help with generator start-up.
P5 – Fail-Safe Vent Inlets
This determines whether the “Vent Inlet” relay operates with a normal action or a fail-safe action. If
“Yes” (Fail-Safe Action) is chosen, the relay will default to allow the inlet machine to “Open” under
extreme failure. Example – Power removed. If “No” (Normal Action) is chosen, the relay will default
to allow the main controller control of the inlet. If “Fail-Safe” mode is chosen, the wiring must be
reversed as shown in Section 13.8 wiring diagram.
IMPORTANT: It is important to ensure that the correct wiring connections are implemented with the
specific P5 or P6 setting selection. Section 13.8 shows the required wiring for Normal
Action (P5/P6 = “No”) and also the required wiring for Fail-Safe Action (P5/P6 =
“Yes”).
P6 – Fail-Safe Tunnel Inlets
This determines whether the “Tunnel Inlet” relay operates with a normal action or a fail-safe action. If
“Yes” (Fail-Safe Action) is chosen, the relay will default to allow the inlet machine to “Open” under
extreme failure. Example – Power removed. If “No” (Normal Action) is chosen, the relay will default
to allow the main controller control of the inlet. If “Fail-Safe” mode is chosen, the wiring must be
reversed as shown in Section 13.8 wiring diagram.