Fulton VMP Webster Oil_Combo Burner User Manual
Page 38
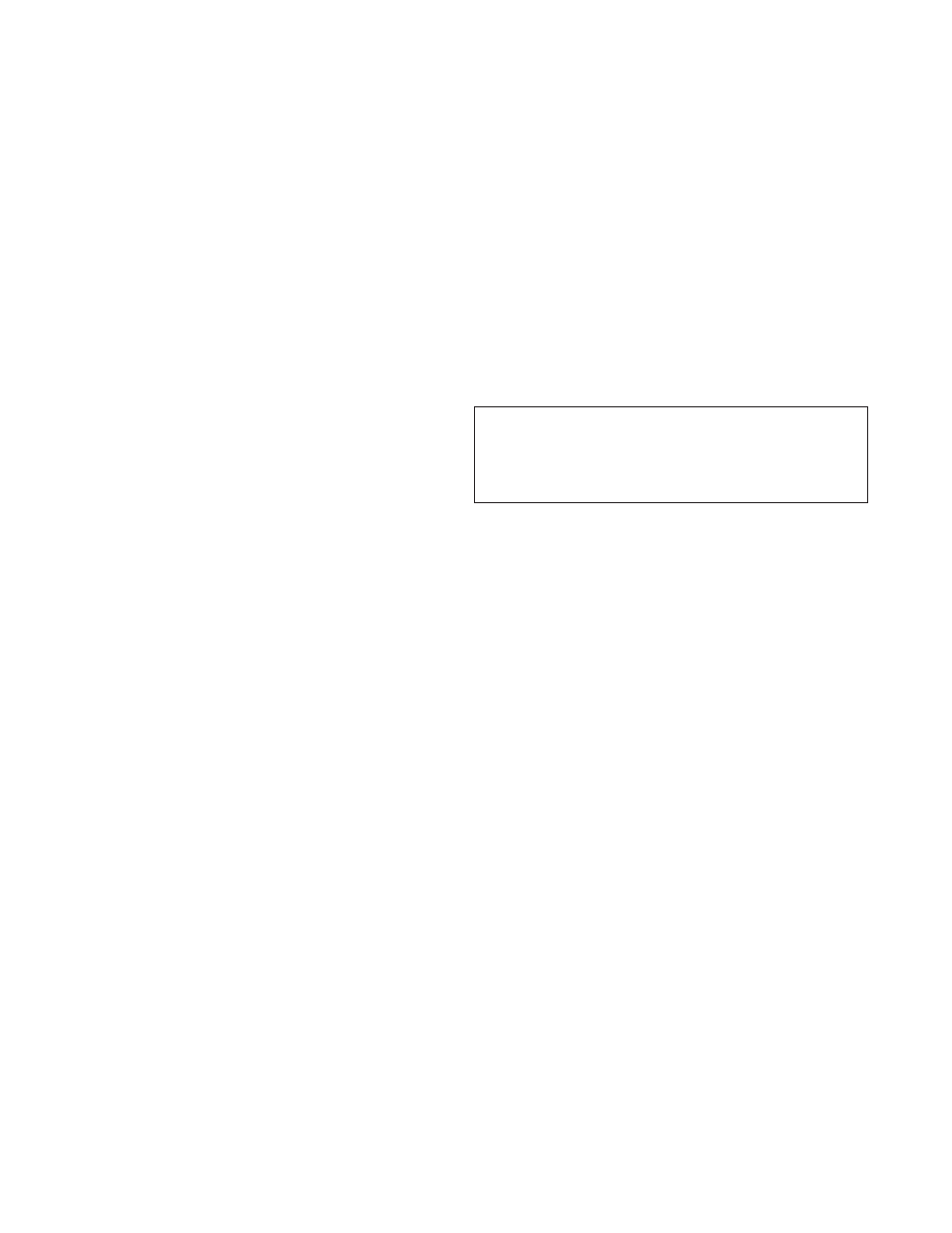
m. At high fire (end of the modulating motor travel), adjust
the high fire input (open or close the fuel valve) to match
the maximum input and/or pressure listed on the rating
label. The fuel metering valve should be nearly closed
(or closed) at this point and the nozzle pressure should
be about 150 PSIG (return line) for JB3. For JB1 and JB2
250 to 300 psig.
n. If equipped with FGR, adjust the NOx level to be about
10% below any guaranteed NOx performance or if perfor-
mance guarantee exists adjust the FGR to provide some
added turbulence but not high enough to impact flame sta-
bility. A balance of the FGR control valve and air damper
are required to obtain the final result, as each can impact
the other. If this is a 30 ppm system, the FGR limiting pot
should be adjusted to reduce the FGR rate for stable com-
bustion, with the FGR control valve set when firing gas. If
this is a 60 ppm system, no adjustment is necessary.
o. Modulate the burner to low fire, adjusting the O2 level
as the burner modulates.
p. Adjust the low fire input, using the fuel cam or low fire
regulator on LO-HI-LO systems and air damper adjust-
ments. If the burner is equipped with FGR, adjust the NOx
level according to the type of system (limiting potentiom-
eter or matching gas).
q. Re-adjust the midfire points for the correct O2 levels.
The linkage may need to be readjusted to obtain the cor-
rect relationship between the fuel valve and air damper.
(Figure I-1)
r. If equipped with FGR, adjust the NOx levels at low and
midfire rates to be about 10% under the guaranteed levels
or as required for the gas firing.
s. The burner should be operating at low fire to adjust
the air proving switch. Turn the adjusting screw cw (in)
until the burner trips out (shutdown caused by the air flow
switch). Turn the adjustment screw ccw (out) 1 ½ turns
from the point of shutdown. Check the operation at higher
rates.
t. Adjust the oil pressure switch to trip and shutdown the
burner at a pressure that is 10% lower than the supply oil
pressure.
12. Air Atomized, #2 oil Setup
The air atomized oil system has the potential for a large
turndown range similar to gas and has the potential to be
adjusted to different low fire rates. See the burner name-
plate for details on actual rates for this burner.
If the burner is equipped with FGR and is a linkage sys-
tem, the type of FGR control must be determined prior
to starting. If this is a dual fuel burner, the FGR rate is
determined by the NOx performance on gas. A 60 ppm
burner will operate with the same FGR rate on gas and oil.
A 30 ppm unit will use the limiting potentiometer to slightly
reduce the FGR rate on oil firing. For Oil only combustion,
the NOx level will be given on the burner detail sheet, and
should be used to set the FGR control valve.
a. Place the burner switch in the “OFF” position.
b. Place the “Auto-Manual” switch in the manual position.
If this is a combination fuel burner, make sure the fuel se-
lector switch is on “OIL”.
c. Place the manual flame control potentiometer in the
min (low fire) position.
d. Turn the electrical power for the burner, boiler and re-
lated components on.
e. Verify that the oil metering valve is at the nearly closed
position.
f. Turn the burner switch on. This will start the blower mo-
tor and initiate the purge cycle.
g. When the prepurge sequence is complete and the low
fire start switch is made, the pilot valve will open and the
pilot flame should be visible through the burner sight port.
h. When the pilot flame is established, the flame safeguard
will energize the main oil valves (indicated with the Fuel
Valve Light), and the burner should ignite at low fire. This
operation of the main fuel valves must be visually checked
by observing the valve stem moving up with a motorized
valve or hearing the clicking noise from a solenoid valve.
NOTE: If the burner is not operating as indicated, follow
the troubleshooting steps to determine the problem and
corrective action.
WARNING
DO NOT ATTEMPT TO START THE BURNER WHEN EX-
CESS OIL HAS ACCUMULATED, WHEN THE UNIT IS FULL
OF VAPOR, OR WHEN THE COMBUSTION CHAMBER IS
HOT.
i. After a few seconds, the combustion analyzer should
have an accurate reading of the O2 in the stack. The O2
level should be between 4% and 7% (see Figure I-3 for
O2 rates), and the nozzle oil press should be between 5
and 15 PSIG (see Figure I-4). Do not attempt to fine tune
combustion until the high fire input has been set.
If the burner is equipped with FGR, the FGR control valve
or limiting potentiometer should be set for the approximate
NOx level required.
• Turning the cam screw in will add fuel, making it richer
and reducing the O2 level.
• Turning the cam screw out will reduce the fuel input,
increasing the O2 level.
• The air damper should be positioned for the correct low
fire settings.
• The atomizing air pressure can be adjusted using the air
bleed valve.
j. Operate the burner until the boiler is warmed up, and
near the operating pressure or temperature.
k. Increase the firing rate, using the manual potentiome-
ter, while monitoring and adjusting the O2 level. Adjust the
cam, oil pressure and atomizing air pressure as needed to
reach the high fire input.
l. If the burner is equipped with FGR, adjust the FGR con-
trol valve or potentiometer as required to maintain the NOx
level.
m. At high fire (end of the modulating motor travel), adjust
the high fire input to match the maximum input listed on
the rating label. Using a flow meter, the fuel input may be
measured using the following equation,
Oil GPH =
[Gal end – Gal start] x [3600 sec/hr] /
[measured sec]
Where Gal end = meter gallons at end of test
Page 38
Startup and Operating Adjustments
JB Manual