Fulton VMP Webster Oil_Combo Burner User Manual
Page 36
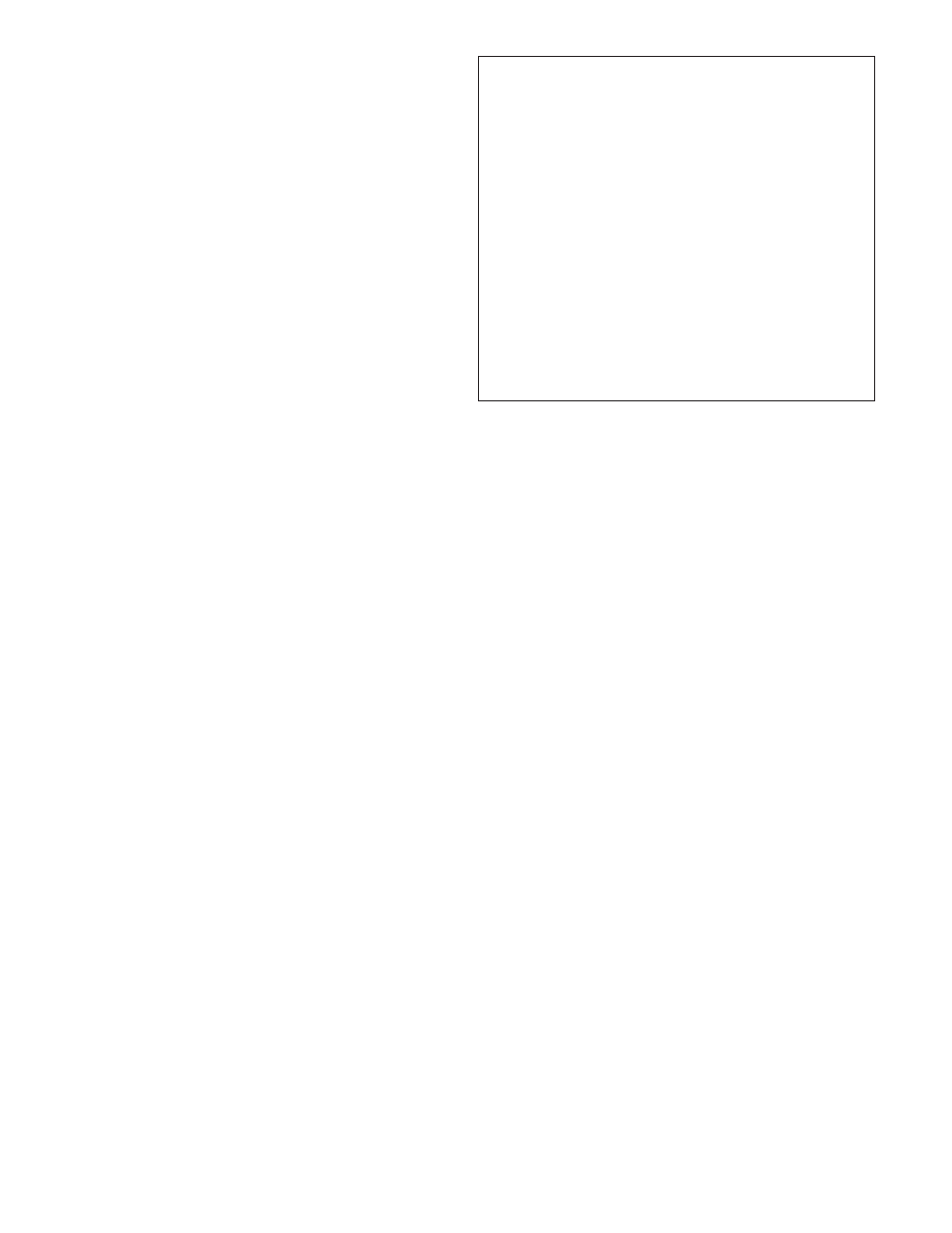
valves must be visually checked by observing the valve
stem operation.
k. After the timer has completed the trial for main flame,
the burner will go out on alarm (the closed manual gas
valve prevented the burner from lighting). At this time, the
gas valves must be visually checked to verify that they
have closed. This test sequence proves the proper opera-
tion of the primary control.
l. Press the reset button and restart the burner. When the
pilot has started, open the manual gas valve to allow the
main flame to start.
m. If equipped with FGR, the shutoff FGR valve should
open on a linkage system, after the main flame has been
proven. The timing can be adjusted with the time delay in-
side the control panel, so that the FGR shutoff valve opens
5 to 10 seconds after the main flame is established. The
control valve of the linkageless system should move from
closed to a low flow position after light off timing has ex-
pired.
NOTE: If the burner is not operating as indicated, follow
the troubleshooting guide steps to determine the problem
and corrections required.
n. After a few seconds, the combustion analyzer should
have an accurate reading of the O2 in the stack. Figure
I-3 shows the typical range of O2 at different firing rates,
and the burner should be adjusted to be within this range.
Rough settings for low and mid fire combustion settings
are adequate at this time. Once the high fire is set, the
other settings can be fine tuned.
• Turning the cam screw in will add fuel, making it richer
and reducing the O2 level.
• Turning the cam screw out will reduce the fuel input,
increasing the O2 level.
If equipped with FGR, the NOx level should be close to the
desired NOx, as required by the specific order. The FGR
valve can be opened to decrease the NOx level, or closed
to increase the NOx level.
o. Operate the burner until the boiler is warmed up, and
near the operating pressure or temperature. Increase the
firing rate, using the manual potentiometer, or put low fire
hold switch in auto mode, while monitoring and adjusting
the O2 level. Adjust the gas pressure regulator as needed
to reach the high fire input.
p. If equipped with FGR, adjust the FGR valve as needed
to obtain the approximate NOx level.
q. Adjust the high fire input to match the maximum input
listed on the rating label. At high fire, the gas butterfly
valve should be at least 75 degrees open (more if avail-
able gas pressure is low), and the gas pressure regulator
adjusted to obtain the rating. The input should be
measured using the following equation:
Calculating Natural Gas Input
Gas MBH =
HHV x [(Patm + Pgas)/29.92] x [520/(Tgas +460)] x
[measured ft3/sec] x [3600 sec/hr]
Where:
MBH = 1000’s of BTU/M input
HHV = Higher heating value of gas, BTU/cubic feet
Patm = Atmospheric pressure in inches Hg
Pgas = Gas pressure before gas meter in inches Hg
(inches HG = PSIG x 2.04)
Tgas = Gas temperature at the flow meter, in
degrees F
Measured ft
3
= volume of gas measured by meter
sec = Time for measured ft
3
to flow through meter
Note: Some gas meters require a 6 inch wc correction
to Pgas. Consult your meter calibration data.
NOTE: The listed manifold pressure is only an ap-
proximate value and can vary with operating condi-
tions and normal tolerances. The fuel flow rate must
be measured to obtain an accurate input value.
r. Adjust the air damper to obtain the correct O2 level.
s. If equipped with FGR, adjust the NOx level to be about
10% below any guaranteed NOx performance. A balance
of the FGR control valve and air damper are required to
obtain the final result, as each can impact the other.
t. Modulate the burner to low fire, adjusting the O2 level
as the burner modulates.
u. Adjust the low fire input, using the fuel cam and air
damper adjustments. The linkage may need to be read-
justed to obtain the correct relationship between the fuel
valve and air damper. (Figure I-1)
v. Re-adjust the midfire points for the correct O2 level.
w. If equipped with FGR, adjust the NOx levels at low
and midfire rates to be about 10% under the guaranteed
levels.
x. Adjust the low gas pressure switch to be 10% below
the lowest expected gas pressure.
• With a gauge or manometer at the same location as the
low gas pressure switch, modulate the burner to deter-
mine the firing rate with the lowest gas pressure.
• At the lowest gas pressure, adjust the low gas pressure
setting up until the switch breaks and causes the burner
to shutdown.
• From the scale reading of the switch, adjust the set-
ting to a pressure that is 10% lower than the shutdown
pressure. For example, if the switch opened at 10 inches
as indicated on the low gas pressure switch, the switch
should be adjusted to a reading of 9 inches.
• Remove the gauge or manometer and plug the open-
ing.
• Cycle the burner on and off to determine if the limit
works properly.
• If the limit causes nuisance shutdowns because of
small pressure drops during startup, reduce the pressure
setting an additional 5%.
y. Adjust the high gas pressure switch to be 10% above
Page 36
JB Manual
Startup and Operating Adjustments