Micromod Micro-DCI: 53SL5100B Single Loop Controller User Manual
Page 44
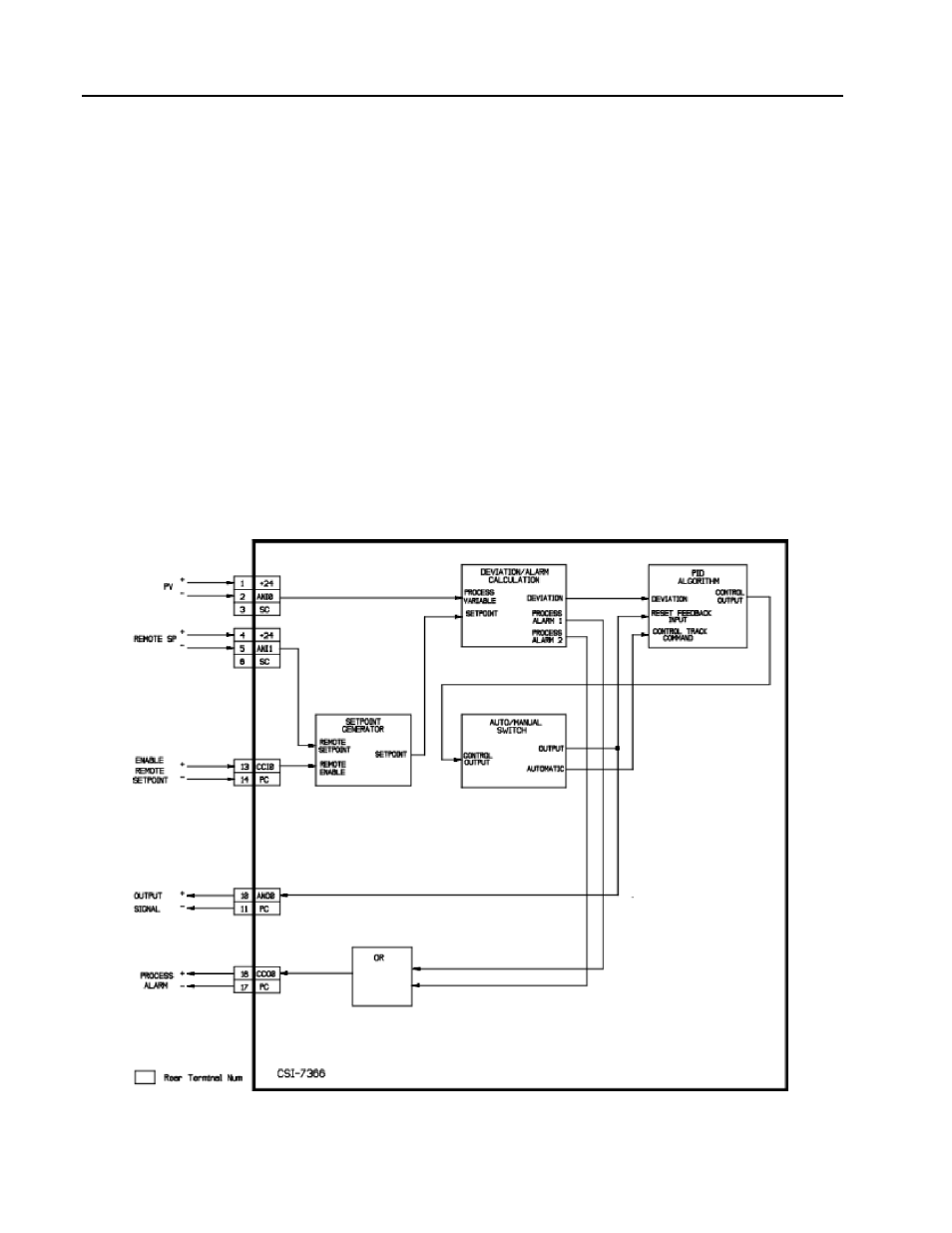
53SL5100B Single-Loop Controller
INSTRUCTION MANUAL
It is the difference between the setpoint (SP) and received process variable (PV), augmented by the action of
the tuning constants Proportional Band, Reset Time, and Rate Time, that determines the required output to
the final element to restore the process. The output signal (Analog Output) to the final element is 4-20 mA dc.
This signal is also factory calibrated for zero and span, and should not be altered. On the controller display,
the output signal value correlates to the desired control element operation (e.g., an output of 100% equals a
20 mA signal amplitude, which causes a valve to be fully opened or closed, depending on the reverse valve
setting in the Single Loop Controller).
Single Loop Controller output response characteristics to the process changes are determined by
Proportional, Integral, and Derivative parameters (also called PID constants). The controller PID constants, as
well as other controller functions (e.g., reverse valve), can be defined with configuration datapoint parameter
entries. The PID general response characteristics are defined in Section 10, Instrument Tuning.
As illustrated in Figure 5-2, Single Loop Controller Block Diagram, when a 1 is loaded into System Module
datapoint B00 to initiate CS1, the signal designators are as follows:
1. ANI0 = Process Variable Input
2. ANI1 = Remote Setpoint Input
3. ANO0 = Controller Output
4. CCI0 = Enable Remote Setpoint
5. CCO0 = Process Alarm
38