Table 4-8. control module (continued) – Micromod Micro-DCI: 53SL5100B Single Loop Controller User Manual
Page 39
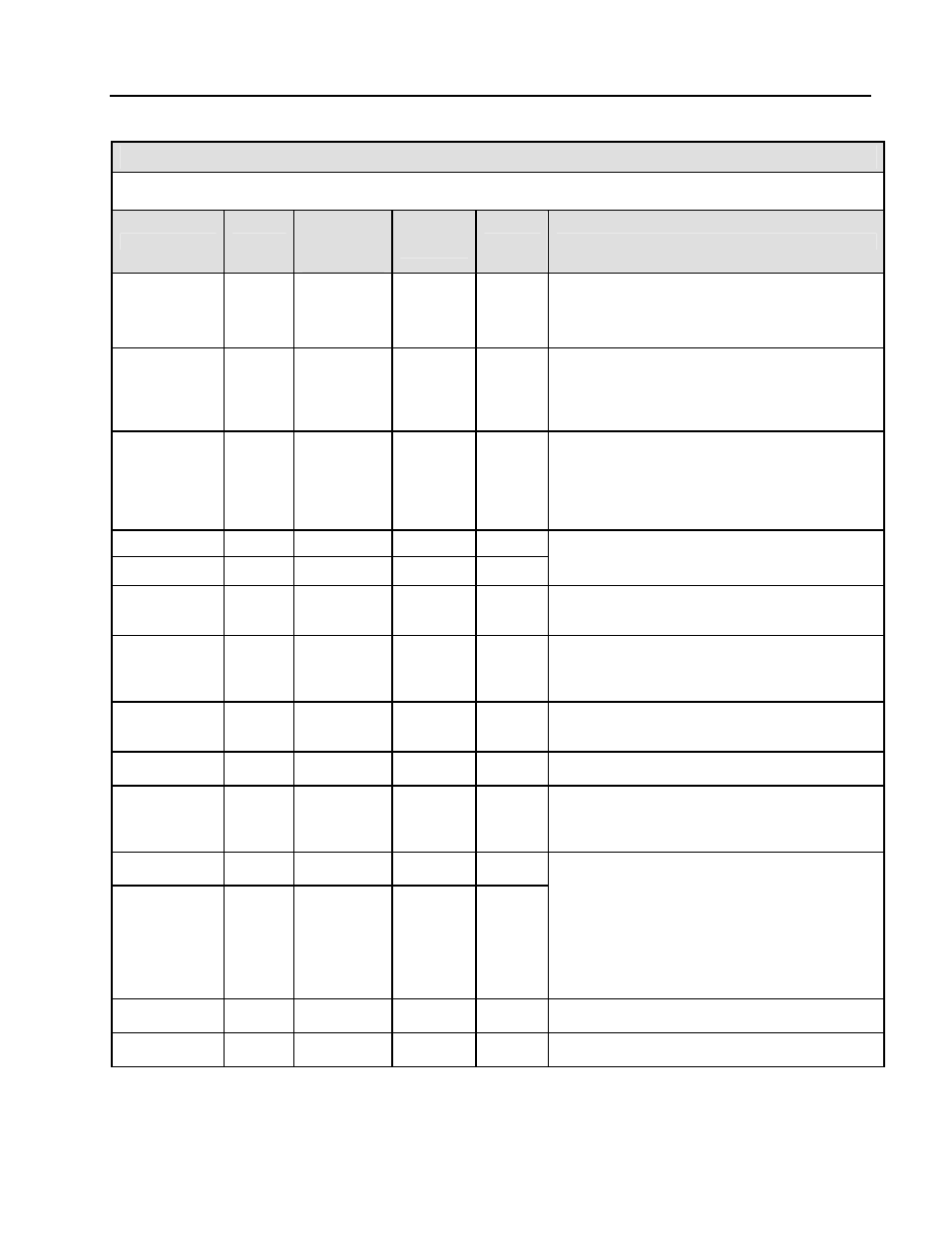
53SL5100B Single-Loop Controller
INSTRUCTION MANUAL
33
Table 4-8. Control Module (continued)
Purpose: The primary purpose of this module is to set the instrument’s Alarm Index mode, Alarm
Limits 1 & 2, and Alarm Dead Band.
Title
Symbol
CS
■
1 | 2 | 3 | 4
CON-0
Datapoint
Default
Attribute
Control Action
RSW
■
106 0
When set to a 0, the controller output increases as
the process value increases.
When set to a 1, the controller output decreases as
the process value increases.
Reverse Valve
RSV
■
L109 0
This parameter provides information for the control
display to indicate which direction the control output
must go to close the final control element. A 1
indicates that 20 mA closes the valve. A 0 indicates
that 20 mA opens the valve.
Manual
Fallback
Disable
MFD
■
L120 0
Under normal operation, whenever the controller is
powered up, the Auto/Manual Selector is forced to
the Manual position. When this datapoint is set to a
1, the selector will not be forced to the Manual
position at power up but will remain in the last
position before power was removed.
Alarm Limit 1
PL1
■
C103 100
Alarm Limit 2
PL2
■
C104 0
These parameters are the points in engineering
units at which the alarms are triggered.
Alarm
Dead
Band
ADB
■
C105 2
This parameter sets the activation/deactivation gap
for the alarm. This value in engineering units
defines an area of hysteresis at the alarm point.
Proportional
Band
PB
■
C106 100
This parameter is the percent of error required to
move the output full scale for proportional action. It
modifies the controller response in standard PID
terms.
Reset Time
TR
■
C107 0
This parameter represents the number of minutes
per repeat of integral action. It modifies the
controller response in standard PID terms.
Rate Time
TD
■
C108 0
This parameter value represents the minutes that
proportional action is advanced (derivative action).
Manual Reset
MR
■
C111 50
This parameter determines the position of the valve
(output) when the instrument is in Automatic mode
and the error is zero. (It is only in effect when TR =
0.)
Controller
Span
■
C115 1100
Controller
Lower Range
■
C116 0
These two parameters set the upper and lower
values on the controller display. They permit the
control action to be defined over a range
independent of the process variable input range.
They also determine the speed at which the
setpoint changes when the up or down arrow
pushbuttons are pressed (CS1 through CS3). For
CS4, they determine only the displayable range, as
the setpoint pushbuttons are not used.
Control Tag
Name
■
A000
An assignable 10 character name that appears with
CS1-4 displays.
Engineering
Units
■
A001 Percent
The default is PERCENT, but is assignable as units
of measure the Process Variable represents.
NOTE: CS1 = Single Loop (PID) Controller, CS2 = Analog Backup Controller, CS3 = Ratio
Controller, and CS4 = Automatic/Manual Station.