Micromod Micro-DCI: 53SL5100B Single Loop Controller User Manual
Page 111
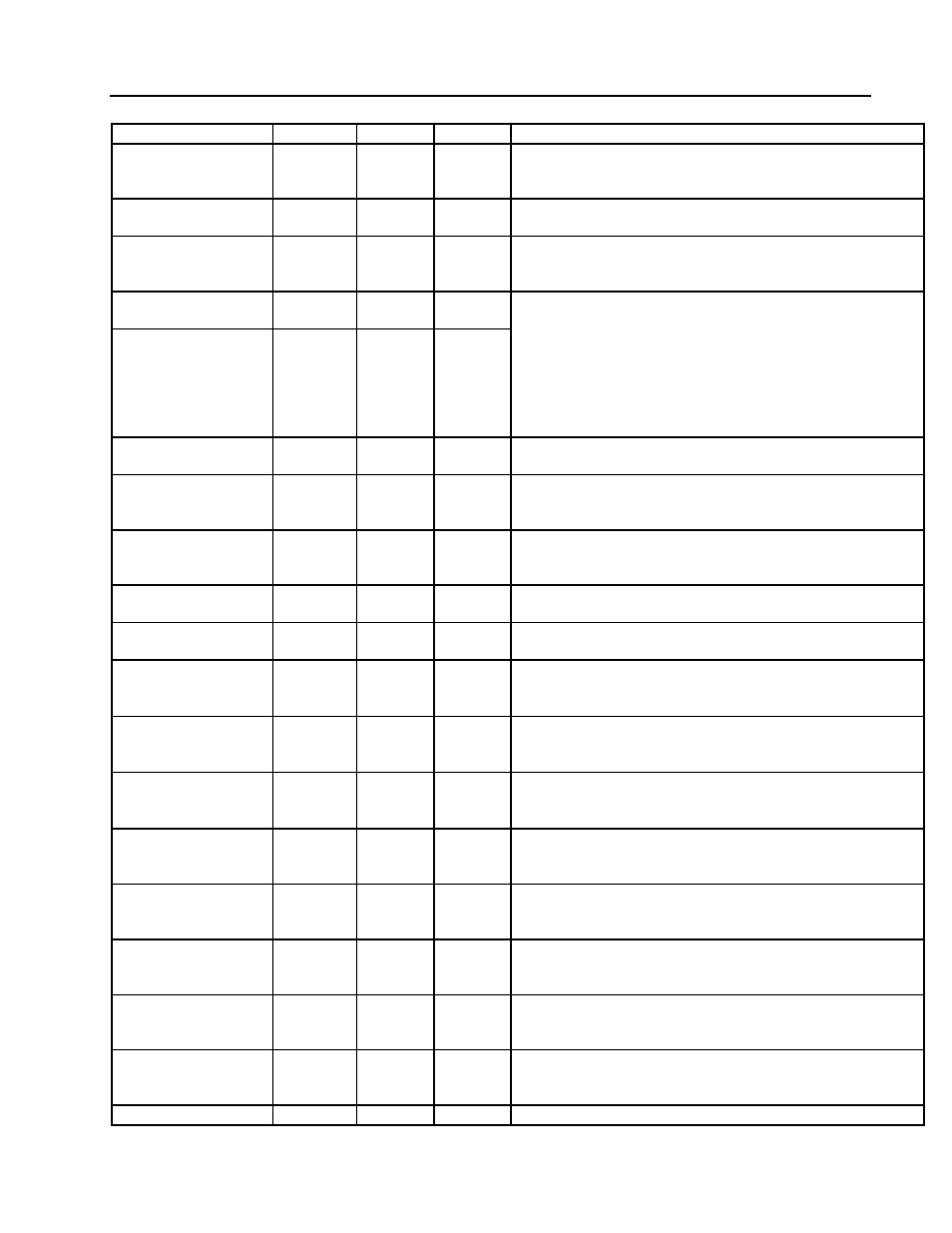
53SL5100B Single-Loop Controller
INSTRUCTION MANUAL
105
controller response in standard PID terms.
Reset Time
TR
C107
0
number of minutes per
This parameter represents the
repeat for integral action. It modifies the controller
response in standard PID terms.
Rate Time
TD
C108
0
utes that proportional
This parameter represents the min
action is advanced (derivative action).
Manual Reset
MR
C111
50
mode and
This parameter determines the position of the valve
(output) when the instrument is in Automatic
the error is zero. (It is only in effect when TR = 0.)
Controller Span
IR
C115
100
Controller Lower
Range
ues
it the control action to
e the speed at
row
ILR
C116
0
These two parameters set the upper and lower val
on the controller display. They perm
be defined over a range independent of the process
variable input range. They also determin
which the setpoint changes when the U
P
or D
OWN
ar
pushbuttons are pressed (CS1 through CS3). For CS4,
they determine only the displayable range, as the
setpoint pushbuttons are not used.
Remote Setpoint
RSP
C120
0
e.
It is the calculated result of the remote setpoint algorithm
and is used as the setpoint if the controller is in remot
ANI0 Engineering
Span
SPAN
C256
100
This determines the upper range that analog input 0
represents in engineering units. The upper range value
equals Engineering Zero plus Engineering Span.
ANI1 Engineering
Span
SPAN
C257
100
1
pper range value
This determines the upper range that analog input
represents in engineering units. The u
equals Engineering Zero plus Engineering Span.
ANI0 Engineering
ZERO
C276
0
Zero
This is the lower range value of analog input 0.
ANI1 Engineering
Zero
ZERO
C277
0
This is the lower range value of analog input 1.
ANI0 Calibrate Span
er is
CIS
C296
This is the calibration span adjustment. This paramet
factory set and should not need adjustment under
normal operation. See Section 12.3 for adjustment.
ANI1 Calibrate Span
meter is
factory set and should not need adjustment under
t.
CIS
C297
This is the calibration span adjustment. This para
normal operation. See Section 12.3 for adjustmen
ANO0 Calibrate
COS
C300
This is the calibration span adjustment. This parameter is
Span
factory set and should not need adjustment under
normal operation. See Section 12.3 for adjustment.
Parameter Point 1
PDA
F087
C106
value
d
Designator
A database datapoint whose contents will be displaye
under the Point 1 Name (e.g., C103 to display the Alarm
Limit 1 setting) of the parameter display.
Parameter Point 2
PDB
F088
C107
value
d
Designator
A database datapoint whose contents will be displaye
under the Point 2 Name (e.g., C104 to display the Alarm
Limit 2 setting) of the parameter display.
Parameter Point 3
PDC
F089
C108
d
Designator
value
A database datapoint whose contents will be displaye
under the Point 3 Name (e.g., C105 to display the Alarm
Dead Band) of the parameter display.
ANI0 Input (Display
ANI
H000
0
measured
Only)
This is the value in engineering units of the
input for ANI0 after all signal conditioning has been
applied.
ANI1 Input (Display
ANI
H001
0
measured
Only)
This is the value in engineering units of the
input for ANI1 after all signal conditioning has been
applied.
CCI Input (Display
CCI
L000
0
0 when IINV = 0.
When open, a 4 - 24 V dc input signal =