10 overload protection, 11 brake motors, 12 reversing the motor – DE-STA-CO IM-pAC AC Drive Getting Started Guide User Manual
Page 9: 13 emergency stop safety, 14 warranty and return policy, 15 disposal, Overload protection, Brake motors, Reversing the motor, Emergency stop safety
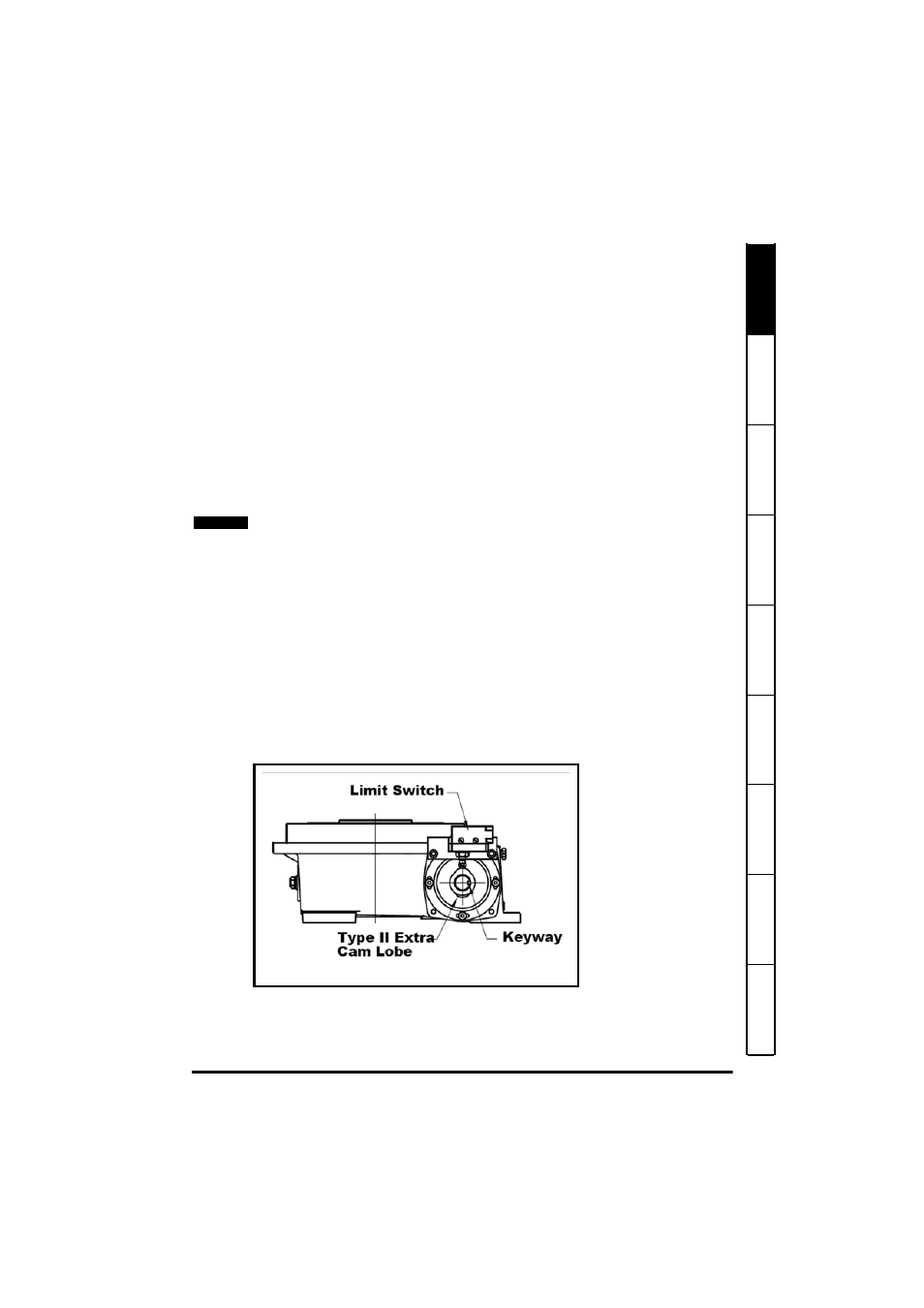
IM-pAC Getting Started Guide
9
Issue Number: 5
www.camcoindex.com | www.destaco.com
Re
a
Sa
R
Me
ch
Ele
n
Ke
Par
D
UL
Li
1.10
Overload Protection
The IM-pAC drive can provide protection to the indexer if the indexer is restrained from
movement by an obstruction or jammed during motion. See section 1.24 How to
configure the IM-pAC drive to trip for a current overload.
1.11
Brake Motors
See "24V brake motor - wiring and parameters" section.
1.12
Reversing the Motor
See "Reversing the motor direction - wiring and parameters" section.
1.13
Emergency Stop Safety
It is recommended that you purchase a commercial safety relay and motor contactor
product from a vendor such as Schneider Electric, Square D, Telemecanique or Phoenix
Contact that complies with the OSHA, ANSI or IEC safety directives you are required to
follow.
1.14
Warranty and Return Policy
The IM-pAC Drive is warranted for 1 year from date of receipt. For technical support call
CAMCO-FERGUSON (847-215-5658).
1.15
Disposal
Waste Electrical and Electronic Equipment (WEEE) Directive and the Restriction on the
use of Hazardous Waste (RoHS) Directive does not apply to the IM-pAC drive.
1.16
Indexer drive shown in middle of dwell position diagram.
Camshaft keyway position of a Roller Gear, Right Angle or Parallel indexer stopped in
the middle of dwell. For an RPP, LPP or WBD see the timing diagram or an assembly
drawing for the middle dwell locations.
A standard Roller Gear unit with cam and limit or proximity switch mounted on the correct
keyway position directly opposite of the output shaft, 90 degrees clockwise from the cam
lobe. The cam and switch may also be mounted on the reducer. If the unit is a Type II
motion a special switch cam is need with one extra lobe, 180 degrees from the first lobe.
The drive must be disabled (open the B2 - B4 connection) before the motor contactors
are opened. Failure to do so will damage the drive.
NOTE