4 configuring the edh4 for mat heater operation – Alpha Technologies XP-EDH4 - Technical Manual User Manual
Page 40
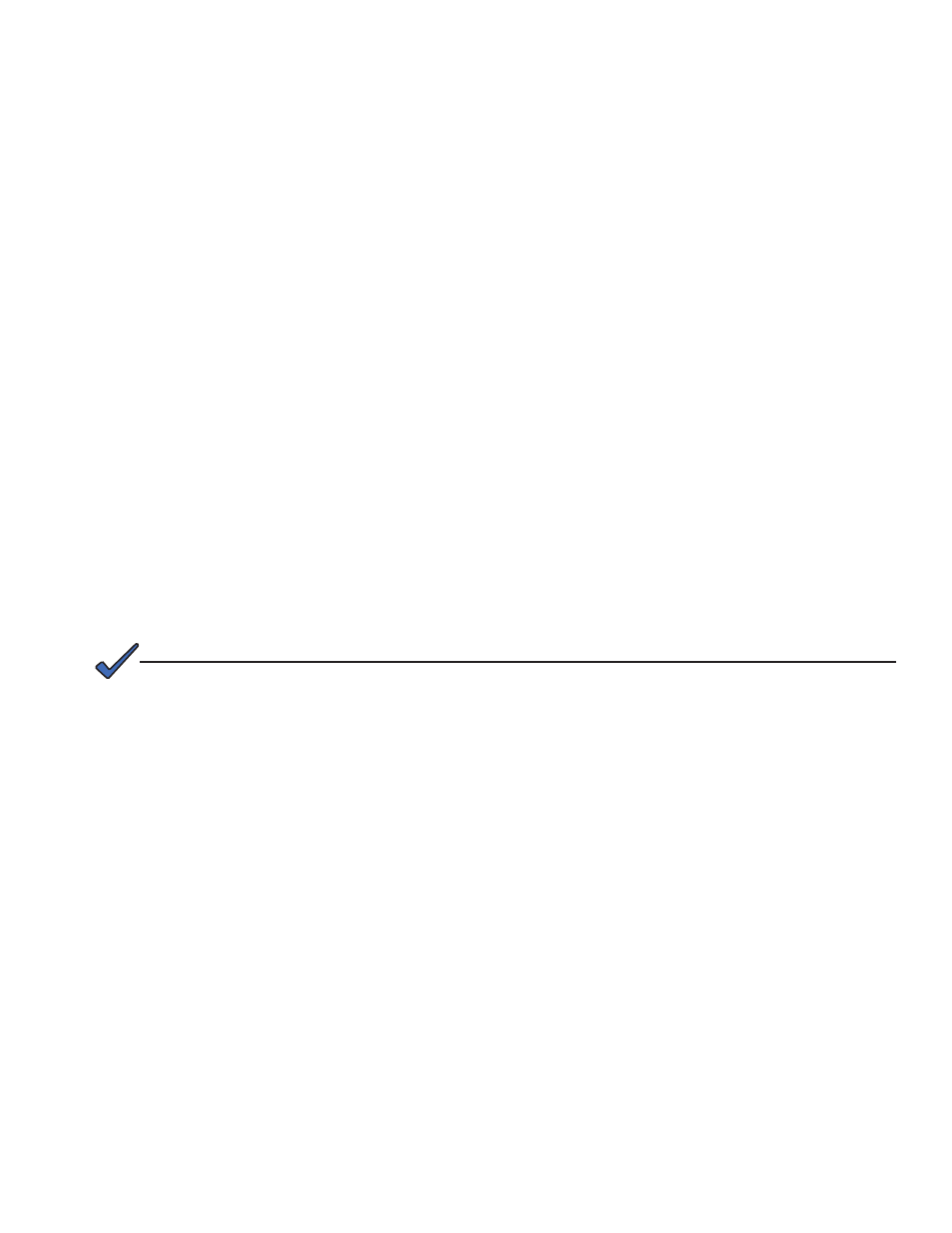
40
745-419-B0-001 Rev. A (11/2013)
3.0
Configuration and Operation, continued
3.4 Configuring the EDH4 for Mat Heater Operation
The CNTL connector can be utilized in conjunction with a built-in mat heater application to control a
battery mat heater controller (customer supplied). The mat heater application will turn the mat heater on
when the temperature falls below a specific threshold, and will turn it off when the temperature returns to
above the threshold. The application provides for a minimum “on” time to avoid frequent on/off cycling,
and also provides for manual override of the transponder algorithm.
The following sections detail the steps necessary to configure the EDH4 to utilize the built-in mat heater
feature. An external battery temperature sensor is required for the mat heater application. In the case of
HMS-022 power supplies that are capable of being daisy-chained together, the lowest addressed power
supply with a temperature sensor will be utilized. This document assumes the transponder has been
properly provisioned, i.e., SNMP access / trap destinations set up via docsDevNmAccessTable, is online,
and has discovered a power supply with a battery temperature sensor connected.
By default, the mat heater feature is disabled. It will be the operator’s responsibility to configure and
enable the feature for it to work. Three MIBs are utilized to properly configure the EDH4: TLGDGenericIO.
mib, Tollgrade-Lighthouse-Tree-MIB.mib, and TLGDMatHeater.mib. An additional MIB, RFC-1155-SMI.
mib, may be required as a dependency.
3.5 Generic I/O MIB Configuration for Mat Heater Application
This MIB is used to configure the CNTL connector available on the EDH4. This connector is used by the
mat heater feature to control and provide status of the mat heater hardware. Two I/O pins will be used:
a digital output to provide control (turning the mat heater hardware on/off) and a digital input to provide
status (indicating the on/off state of the mat heater hardware). By default, all digital inputs will be inactive.
This means they will not be processed by the transponder until activated. Digital outputs, on the other
hand, are active by default and cannot be deactivated. The following steps detail what is necessary to
configure and activate the auxiliary I/O connector for operation with the mat heater feature:
The Index for the digital input and digital output for the mat heater must be configured as 3.
NOTE:
Digital input suggested settings for mat heater input.
Table index 3, connector Control-pin 4
genericDigitalInputName.3 = “Mat heater”
genericDigitalInputStateNameLow.3 = “Mat heater On”
genericDigitalInputStateNameHigh.3 = “Mat heater Off”
genericDigitalInputActive.3=2
Digital output suggested settings for mat heater input.
Table index 3, connector Control-pin 3
genericDigitalOutputName.3 = “Mat heater”
genericDigitalOutputControlNameLow.3 = “Mat heater On”
genericDigitalOutputControlNameHigh.3 = “Mat heater Off”
Monitoring of the mat heater status input will be accomplished via MIB object genericDigitalInputState.3.
A value of 1(low) from the relay box indicates that the heater is ON. A value of 2(high) from the relay box
indicates that the heater is OFF.
Monitoring of the mat heater control output will be accomplished via MIB object
genericDigitalOutputControl.3. A value of 1(low) indicates that the transponder is commanding the heater
to be ON. A value of 2(high) indicates that the transponder is commanding the heater to be OFF.