Parameters – Elmo Rietschle 2FC4...-1CB User Manual
Page 37
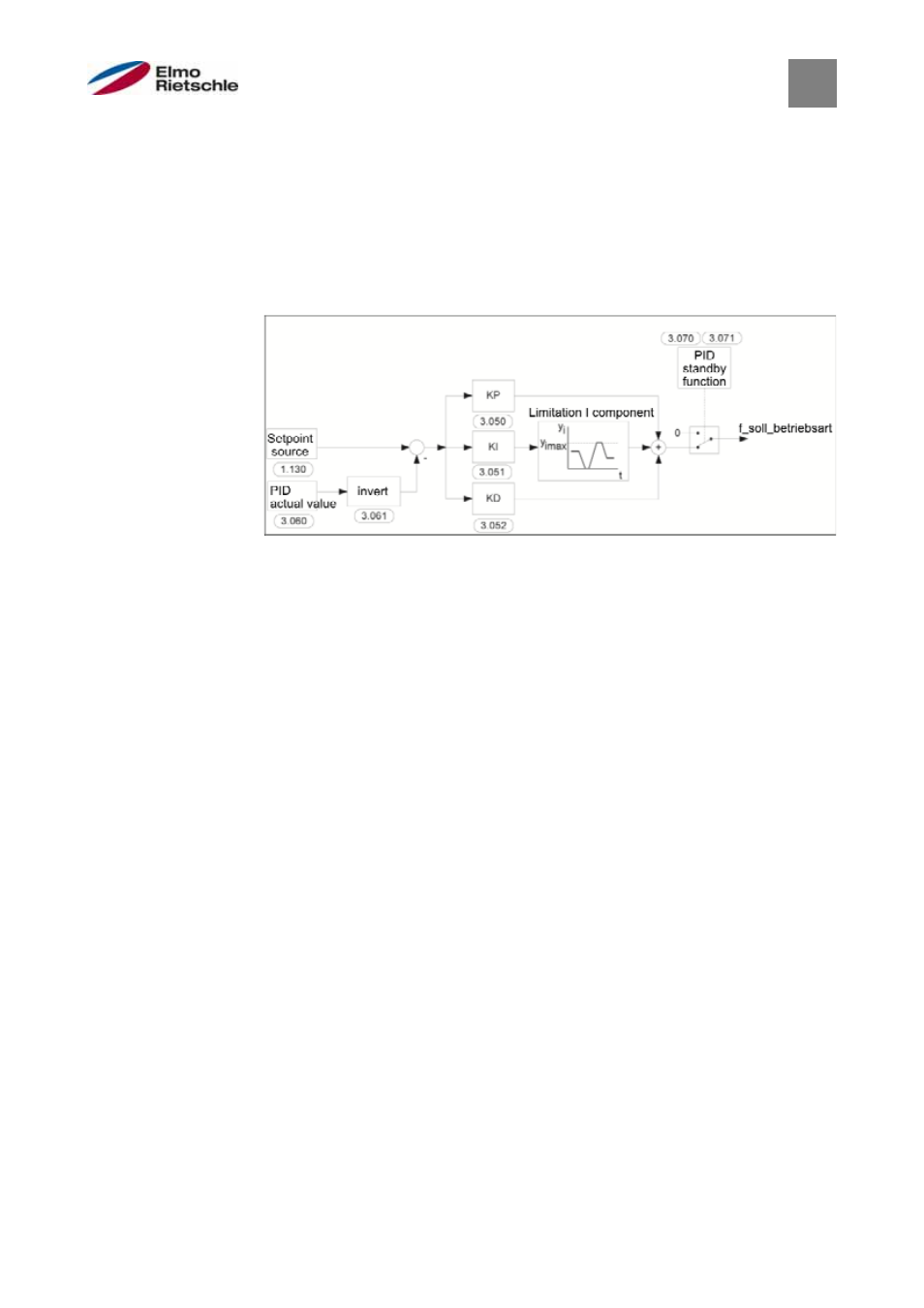
Parameters
7
© Gardner Denver Deutschland GmbH
37
/
74
05.2014 · 610.00260.40.000
PID inverse:
Inversion of the PID feedback can be done with the help of parameter 3,061. The
actual value is read inverted, i.e. 0V…10V correspond internally to 100% ... 0%.
Please bear in mind that the setpoint should also be specified inversely!
An example:
A sensor with an analogue output signal (0V…10V) is to be operated as the actual
value source (at AIx). At an output quantity of 7V (70%), it should be regulated in-
versely. The internal actual value then corresponds to 100% - 70% = 30%. That
is, the setpoint to be specified is 30%.
PID process control
Standby function for PID process control:
This function can be used in applications such as pressure boosting systems, in
which it is controlled to a specific process variable using the PID process control
and the pump should run at a "minimum frequency" (1020) to lead to energy sav-
ings. Since the inverter reduces the pump speed with decreasing process variable
during normal operation, but can never go below the "minimum frequency"
(1,020), it is possible to stop the motor when it runs at the "minimum frequency"
(1,020) for a wait time, the "PID standby time" (3,070).
After the actual value deviates from the setpoint by the set % value, the "PID
standby hysteresis" (3,071), the (motor) control is restarted.