Integral feedback control ( sgi ), Velocity feedback control ( sgv ) – Parker Hannifin SERVO CONTROLLER OEM6250 User Manual
Page 43
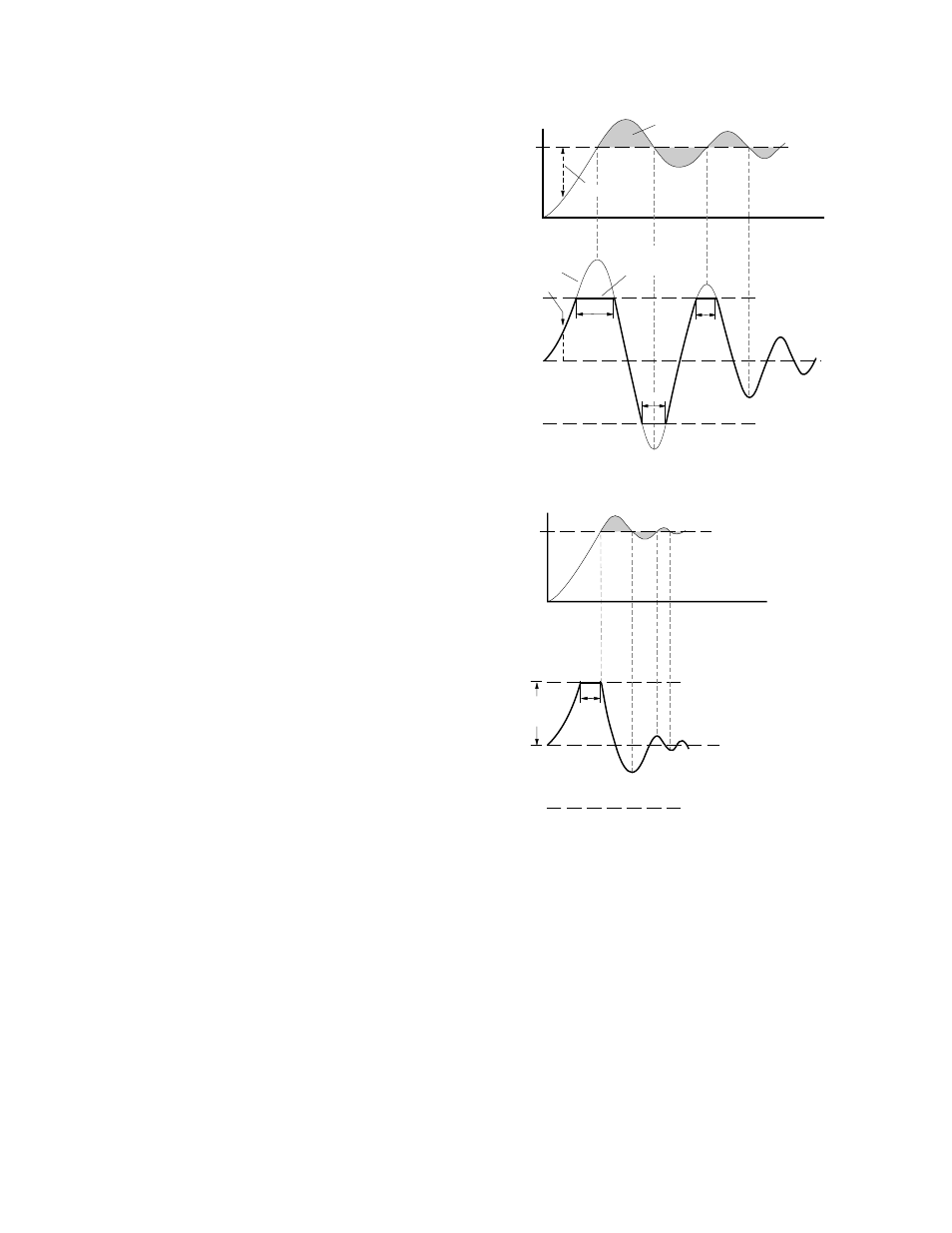
Appendix A – Tuning
3 7
Integral Feedback Control (
SGI
)
Using integral feedback control, the value of the control
signal is integrated at a rate proportional to the feedback
device position error. The rate of integration is set by the
Servo Gain Integral (SGI) command.
The primary function of the integral control is to
overcome friction and/or gravity and to reject disturbances
so that steady state position error can be minimized or
eliminated. This control action is important for achieving
high system accuracy. However, if you can achieve
acceptable position accuracy by using only the
proportional feedback (SGP), then there is no need to use
the integral feedback control.
In the task of reducing position error, the integral gain
(SGI) works differently than the proportional gain (SGP);
this is because the magnitude of its control signal is not
dependent on the magnitude of the position error as in the
case of proportional feedback. If any position error
persists, then the output of the integral term will ramp up
over time until it is high enough to drive the error back to
zero. Therefore, even a very small position error can be
eliminated by the integral feedback control. By the same
principle, integral feedback control can also reduce the
tracking error when the system is commanded to cruise at
constant velocity.
Controlling Integral Windup
If integral control (SGI) is used and an appreciable
position error has persisted long enough during the
transient period (time taken to reach the setpoint), the
control signal generated by the integral action can end up
too high and saturate to the maximum level of the
controller’s analog control signal output. This
phenomenon is called integrator windup.
After windup occurs, it will take a while before the
integrator output returns to a level within the limit of the
controller’s output. Such a delay causes excessive position
overshoot and oscillation. Therefore, the integral windup
limit (SGILIM) command is provided for you to set the
absolute limit of the integral and, in essence, turn off the
integral action as soon as it reaches the limit; thus,
position overshoot and oscillation can be reduced (see
illustration below). The application of this feature is
demonstrated in Step 5 of the Controller Tuning Procedure
below.
Without
SGILIM
Max. Analog Output (+10V)
Min. Analog Output (-10V)
0V
Windup
Duration
(wd)
wd
wd
Internal
Integral
Value
Integral at T1
T1
Position
Time
Actual Output
Generated
by the Integral Term
Position Setpoint
(
D
Command)
Position Overshoot
Position Error at T1
With
SGILIM
Max. Analog Output (+10V)
Min. Analog Output (-10V)
0V
Integral
Windup Limit
(
SGILIM
)
Position
Time
wd
Position Setpoint
(
D
Command)
Velocity Feedback Control (
SGV
)
The velocity feedback control tends to increase damping
and improve the stability of the system. When this
control is used, the control signal is proportional to the
feedback device’s velocity (rate of change of the actual
position). The Servo Gain Velocity (SGV) command sets the
gain, which is in turn multiplied by the feedback device’s
velocity to produce the control signal. Since the velocity
feedback acts upon the feedback device’s velocity, its control
action essentially anticipates the position error and corrects it
before it becomes too large.
A high velocity feedback gain (SGV) can also increase the
position tracking error when traveling at constant velocity.
In addition, setting the velocity feedback gain too high
tends to slow down (overdamp) the response to a
commanded position change. If a high velocity feedback