Parker Hannifin SERVO CONTROLLER OEM6250 User Manual
Page 48
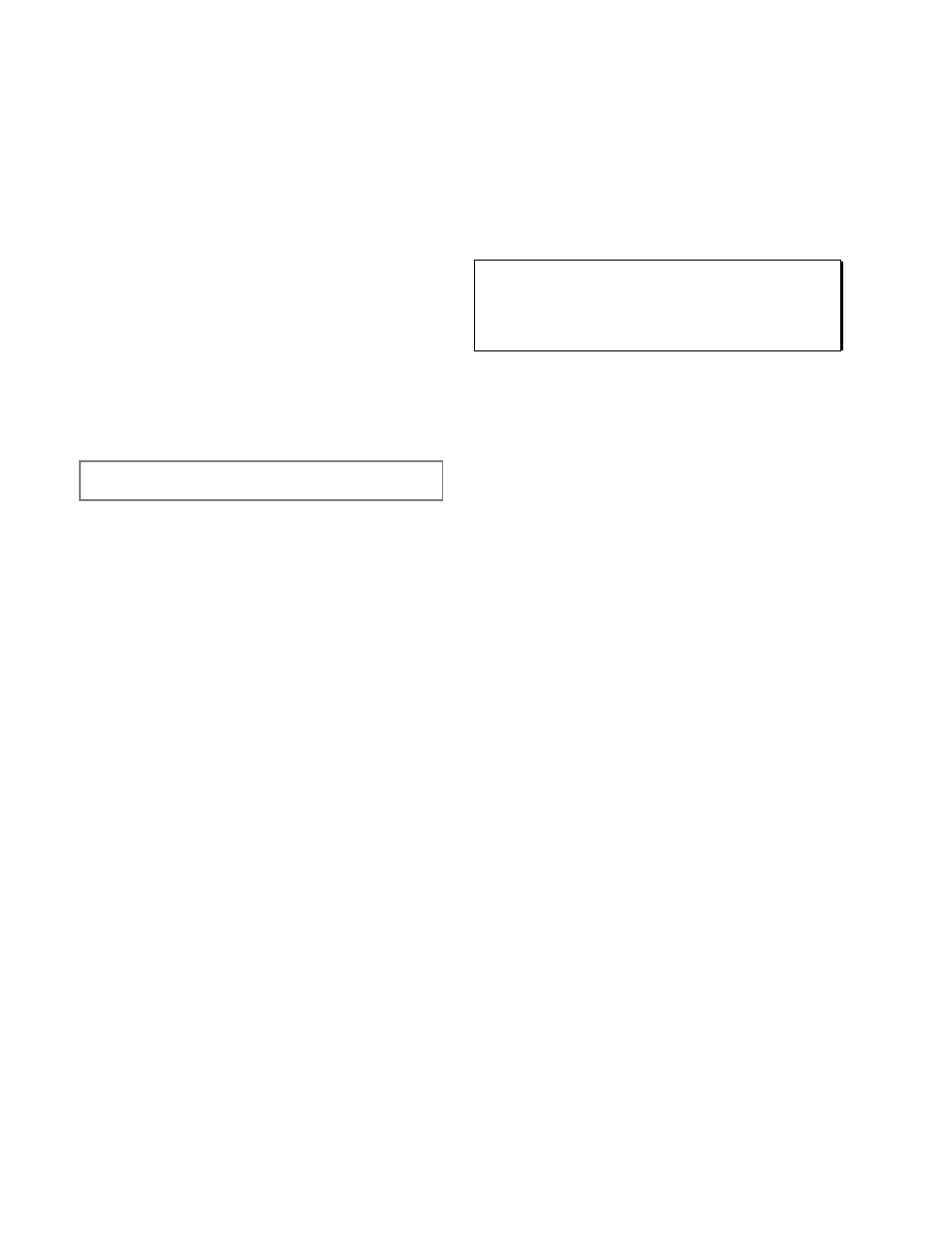
4 2
OEM6250 Installation Guide
Step 4
Optimize the Proportional (
S G P
) and Velocity
(
SGV
) gains
(see illustration on next page for tuning
process).
a. Enter the following commands to create a step input
profile (use a comma in the first data field when tuning
axis 2—e.g., D,1¯¯):
A999
; Set accel to 999 units/sec/sec
AD999
; Set decel to 999 units/sec/sec
V30
; Set velocity to 30 units/sec
D100
; Set distance to 100 units
b. Start with an SGP command value of 0.5 (SGP¯.5 or
SGP,¯.5
).
c. Enter the GO1 or GO,1 command depending on which
axis is being tuned at the time.
d. Observe the plot of the commanded position versus the
actual position on the oscilloscope. If the response is
already very oscillatory, lower the gain (SGP); if it is
sluggish (overdamped), increase the SGP gain.
Repeat Steps 4.c. and 4.d. until the response is slightly
under-damped.
e. Start with an SGV command value of 0.1 (SGV¯.1 or
SGV,¯.1
).
f. As you did in Step 4.c., enter GO1 or GO,1.
g. Observe the plot on the oscilloscope. If the response
is sluggish (overdamped), reduce the SGV gain. Repeat
Steps 4.f. and 4.g. until the response is slightly under-
damped.
h. The flow diagram (next page) shows you how to get
the values of the proportional and velocity feedback
gains for the fastest, well-damped response in a step-
by-step fashion. (Refer to the Tuning Scenario section
later in this chapter for a case example.) The tuning
principle here is based on these four characteristics:
• Increasing the proportional gain (SGP) can speed up
the response time and increase the damping.
• Increasing the velocity feedback gain (SGV) can
increase the damping more so than the proportional
gain can, but also may slow down the response time.
• When the SGP gain is too high, it can cause
instability.
• When the SGV gain is too high, it can cause the
motor (or valve, hydraulic cylinder, etc.) to chatter.
Step 5
Use the Integral Feedback Gain (
S G I
) to
reduce steady state error. (
Steady state position
error is described earlier in the Performance Measurements
section on page 35.)
a. Determine the steady state position error (the difference
between the commanded position and the actual
position). You can determine this error value by the
TPER
command when the load is not moving.
N O T E
If the steady state position error is zero or so small that
it is acceptable for your application, you do not need
to use the integral gain. The use of the Target
Zone Settling Mode (
STRGTE
) is recommended.
b. If you have to enter the integral feedback gain to reduce
the steady error, start out with a small value (e.g.,
SGI¯.1
). After the gain is entered, observe two
things from the response:
• Whether or not the magnitude of steady state error
reduces
• Whether or not the steady state error reduces to zero
at a faster rate
c. Keep increasing the gain to further improve these two
measurements until the overshoot starts to increase and
the response becomes oscillatory.
d. There are three things you can do at this point (If these
three things do not work, that means the integral gain
is too high and you have to lower it.):
1
st
Lower the integral gain (SGI) value to reduce the
overshoot.
2
nd
Check whether the OEM6250’s analog output
saturates the
±10V limit; you can do this by
observing the signal from a digital oscilloscope.
If it saturates, then lower the integral output limit
by using the SGILIM command. This should
help reduce the overshoot and shorten the settling
time. Sometimes, even if the analog output is not
saturated, you can still reduce the overshoot by
lowering SGILIM to a value less than the
maximum output value. However, lowering it too
much can impair the effectiveness of the integral
feedback.
3
rd
You can still increase the velocity feedback gain
(SGV value) further, provided that it is not already
at the highest possible setting (causing the motor
or valve to chatter).