Servo system terminology, Servo tuning terminology, Position variable terminology – Parker Hannifin SERVO CONTROLLER OEM6250 User Manual
Page 40: Oem6250 installation guide
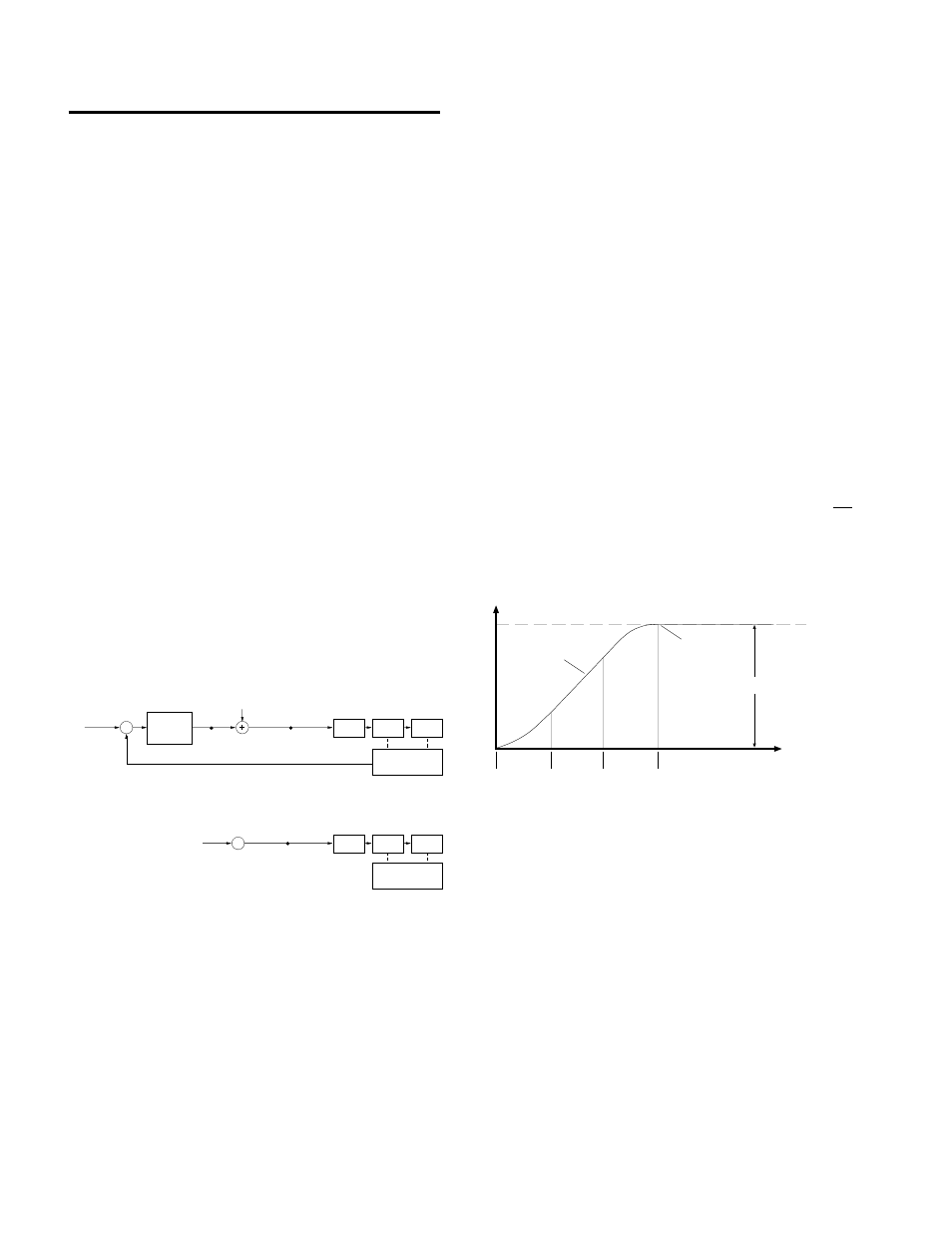
3 4
OEM6250 Installation Guide
Servo System Terminology
This section gives you an overall understanding of the
principles and the terminology used in tuning your
OEM6250.
Servo Tuning Terminology
The OEM6250 uses a digital control algorithm to control
and maintain the position and velocity. The digital control
algorithm consists of a set of numerical equations used to
periodically (once every servo sampling period)
calculate the value of the control signal output. The
numerical terms of the equations consist of the current
commanded and actual position values (plus a few from
the past sampling period) and a set of control parameters.
Each control parameter, commonly called a gain, has a
specific function (see Servo Control Techniques later in
this appendix). Tuning is the process of selecting and
adjusting these gains to achieve optimal servo
performance.
When this control algorithm is used, the whole servo
system is a closed-loop system (see diagram below). It
is called closed loop because the control algorithm
accounts for both the command (position, velocity,
tension, etc.) and the feedback data (from the encoder or
ANI input); therefore, it forms a closed loop of
information flow.
When all gains are set to zero, the digital control
algorithm is disabled. During system setup or
troubleshooting, it is desirable to disable the algorithm
(by setting all the gains to zero) and use the SOFFS
command to directly control the analog output.
Feedback Device
(Encoder or ANI Input)
Load
Servo
Drive
Motor
Load
Command
Digital
Control
Algorithm
Control
Signal
Offset
Drive Command =
Control Signal + Offset
Servo
Drive
Closed Loop System
SOFFS
Offset
Drive Command = Offset
Servo Algorithm Disabled
Feedback Data
Motor
Feedback Device
(Encoder or ANI Input)
The controller has the capability of providing an analog
voltage output of
±10V for commanding the drive. After
the digital control algorithm has calculated the digital
control signal, this digital value is sent out from the DSP
(digital signal processor) to the Digital-to-Analog converter
(DAC). The DAC has an analog output range of -10V to
+10V. It is often possible that the digital control signal
calculated by the control algorithm can exceed this limit.
When this happens, the analog output would just stay, or
saturate, at the maximum limit until the position error
changes such that the control algorithm would calculate a
control signal less than the limit. This phenomenon of
reaching the output limit is called controller output
saturation. When saturation occurs, increasing the gains
does not help improve performance since the DAC is
already operating at its maximum level.
Position Variable Terminology
In a servo system, there are two types of time-varying
(value changes with time) position information used by
the controller for control purposes: commanded position
and actual position. You can use this information to
determine if the system is positioning as you expect.
Commanded Position
The commanded position is calculated by the motion
profile routine based on the acceleration (A, AA),
deceleration (AD, ADA), velocity (V) and distance (D)
command values and it is updated every servo sampling
period. Therefore, the commanded position is the intended
position at any given point of time. To view the
commanded position, use the TPC (Transfer Commanded
Position) command; the response represents the commanded
position at the instant the command is received.
When this appendix refers to the commanded position, it
means this calculated time-varying commanded position, not
the distance (D) command. Conversely, when this appendix
refers to the position setpoint, it means the final intended
distance specified with the distance (D) command. The
following plot is a typical profile of the commanded position
in preset (MC¯) mode.
Setpoint
Distance
(
D
)
Acceleration
Constant
Velocity
Deceleration
Profile
Complete
Position
Time
Commanded
Position
Actual Position
The other type of time-varying position information is the
actual position; that is, the actual position of the motor
(or load) measured with the feedback device (encoder or ANI
input). Since this is the position achieved when the drive
responds to the commanded position, we call the overall
picture of the actual position over time the position
response (see further discussion under Servo Response
Terminology).
To view the actual position, use the TFB (Transfer
Position of Feedback Device) command; the response
represents the actual position at the instant the command
is received. The goal of tuning the servo system is to get
the actual position to track the commanded position as
closely as possible.
The difference between the commanded position and actual
position is the position error. To view the position