Servo response terminology, Position response types – Parker Hannifin SERVO CONTROLLER OEM6250 User Manual
Page 41
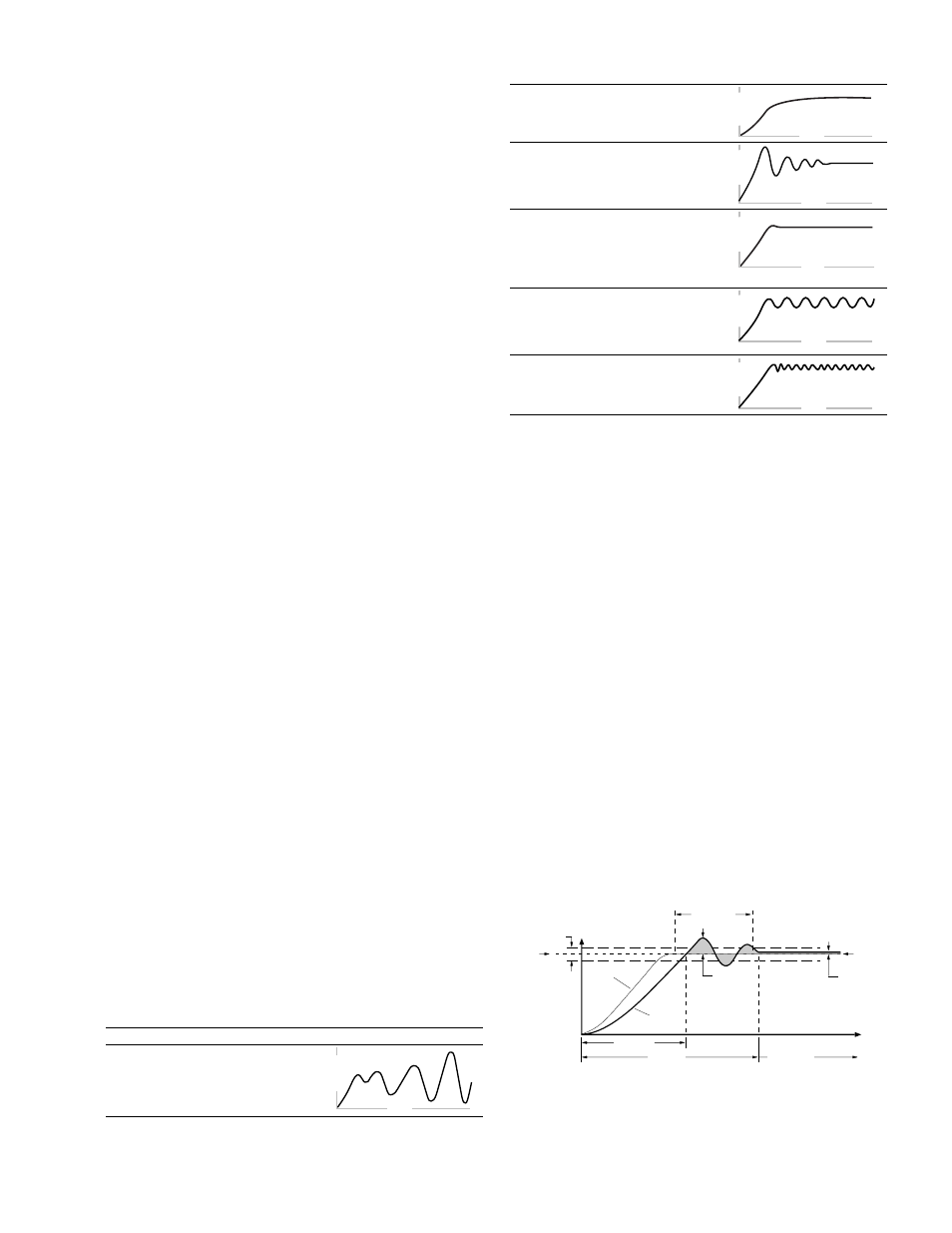
Appendix A – Tuning
3 5
error, use the TPER (Transfer Position Error) command; the
response represents the position error at the instant the
command is received. When the motor is not moving, the
position error at that time is called the steady-state
position error (see definition of steady-state under Servo
Response Terminology). If a position error occurs when the
motor is moving, it is called the position tracking
error.
In some cases, even when the system is properly tuned,
the position error can still be quite significant due to a
combination of factors such as the desired profile, the
motor’s limitation, the dynamic characteristics of the
system, etc. For example, if the value of the velocity (V)
command is higher than the maximum velocity the motor
can physically achieve, then when it is commanded to
travel at this velocity, the actual position will always lag
behind the commanded position and a position error will
accumulate, no matter how high the gains are.
Servo Response Terminology
Stability
The first objective of tuning is to stabilize the system.
The formal definition of system stability is that when a
bounded input is introduced to the system, the output of
the system is also bounded. What this means to a motion
control system is that if the system is stable, then when
the position setpoint is a finite value, the final actual
position of the system is also a finite value.
On the other hand, if the system is unstable, then no
matter how small the position setpoint or how little a
disturbance (motor torque variation, load change, noise
from the feedback device, etc.) the system receives, the
position error will increase continuously, and
exponentially in almost all cases. In practice, when the
system experiences instability, the actual position will
oscillate in an exponentially diverging fashion as shown
in the drawing below. The definition here might contradict
what some might perceive. One common perception
shared by many is that whenever there is oscillation, the
system is unstable. However, if the oscillation finally
diminishes (damps out), even if it takes a long time, the
system is still considered stable. The reason for this
clarification is to avoid misinterpretation of what this user
guide describes in the following sections.
Position Response Types
The following table lists, describes, and illustrates the six
basic types of position responses. The primary difference
among these responses is due to damping, which is the
suppression (or cancellation) of oscillation.
Response
Description
Profile (position/time)
Unstable
Instability causes the
position to oscillate in an
exponentially diverging
fashion.
Position
Time
Over-
damped
A highly damped, or
over-damped, system
gives a smooth but
slower response.
Position
Time
Under-
damped
A slightly damped, or
under-damped, system
gives a slightly
oscillatory response.
Position
Time
Critically
damped
A critically-damped
response is the most
desirable because it
optimizes the trade-off
between damping and
speed of response.
Position
Time
Oscillatory
An oscillatory response
is characterized by a
sustained position
oscillation of equal
amplitude.
Position
Time
Chattering
Chattering is a high-
frequency, low-
amplitude oscillation
which is usually audible.
Position
Time
Performance Measurements
When we investigate the plot of the position response
versus time, there are a few measurements that you can
make to quantitatively assess the performance of the servo:
• Overshoot—the measurement of the maximum
magnitude that the actual position exceeds the position
setpoint. It is usually measured in terms of the
percentage of the setpoint value.
• Rise Time—the time it takes the actual position to
pass the setpoint.
• Settling Time—the time between when the
commanded position reaches the setpoint and the actual
position settles within a certain percentage of the
position setpoint. (Note the settling time definition
here is different from that of a control engineering text
book, but the goal of the performance measurement is
still intact.)
These three measurements are made before or shortly after
the motor stops moving. When it is moving to reach and
settle to the setpoint, we call such period of time the
transient. When it is not moving, it is defined as in
steady-state.
A typical stable position response plot in preset mode
(MC¯) is shown below.
Setpoint
Commanded
Position
Actual
Position
Setpoint
Target Zone Mode
Settling Band
Rise Time
Transient
Settling Time
Overshoot
Steady State
Position Error
Steady State
Time
Position