Troubleshooting, 9 troubleshooting – Retrotec DM-2 User Manual
Page 45
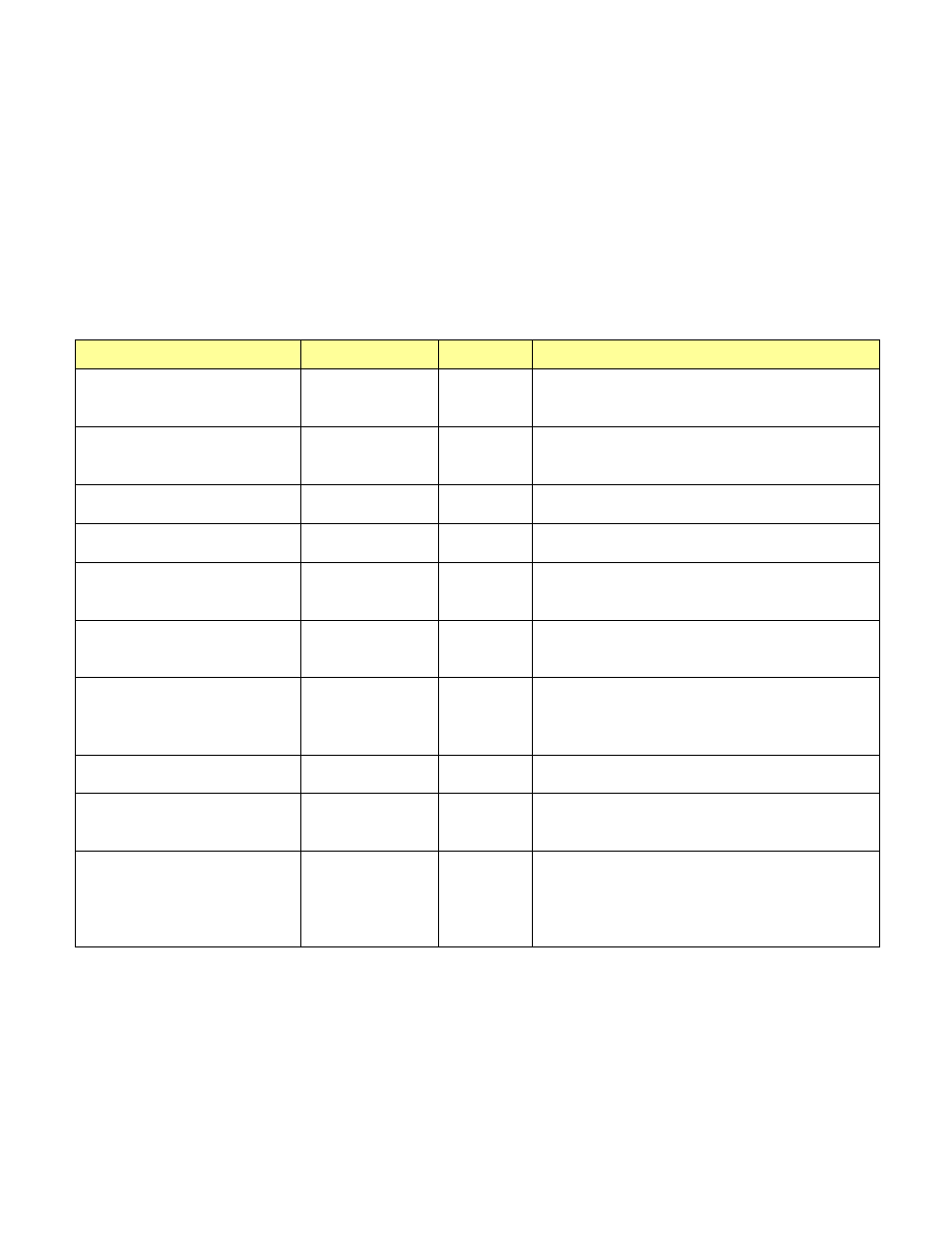
Page 45 of 72
©Retrotec Inc. 2012
9 Troubleshooting
After getting a clear understanding of what pressure is and how it's measured, knowing the common
causes of erroneous readings will increase your confidence in the results. It is often assumed the
gauge must be regularly calibrated in order to get accurate readings, but this thought obscures the fact
that most gauge problems do not result from incorrect calibrations. The following list provides
approximate percent probabilities based on our experience for certain types of gauge problems.
Notice that gauge calibration is one of the smallest, and even that can usually be eliminated by
following the gauge check procedures in this manual.
Table 9: Causes of common problems
Problem caused by
Error frequency
Error range
Comments
Tubing is crimped shut
5%
25 to 90%
Usually noticeable because gauge does not move,
but the blockage may be partial, which could cause
an erroneous result.
Water in tubing
10%
75-90%
Possible only in wet areas. If gauges sent in to be
repaired or calibrated, the water evaporates and
the user never discovers the cause.
Improper Device selected
2%
20 to 90%
Not common because the wrong Range
Configurations will appear on the gauge.
Improper Flow Range selected
5 to 25%
50%
Very common unless gauges checked before and
after tests to ensure the right Flow Range.
Extrapolation pressure set
incorrectly
10%
25%
If the gauge shows a different extrapolation
pressure [@ Pressure] then the results will be
extrapolated to the wrong pressure
Improper use of reference tube
for pressurization
5%
25%
Pressurization is seldom used, but if the technician
is improperly trained, they may not set the
equipment up properly for this test.
Time averaging set too high or
too low
25%
5 to 10%
If the gauge is fluctuating too much it will be
difficult to read. If the time averaging is too high,
the pressure may have changed but that change is
not reflected in the reading.
Wind
25%
10%
These errors can be eliminated by long-term
averaging or by multiple pressure pickups.
Out of calibration
5%
1-50%
Gauges can go out of calibration in a week or may
take 10 years. It is impossible to tell unless the
readings seem unreasonable.
Out of calibration with regular
checks
0.5%
1-2%
Regular gauge checks can eliminate most of the
calibration problems, by identifying large errors
immediately, and before erroneous test results can
be taken. It is unlikely that errors in excess of 2%
would occur if the gauges checked before each use.
Proper training can eliminate almost all of the above errors.
9.1 Check if moving tubes are causing fluctuating pressure
If the measured values on Channel A or B are fluctuating back and forth, in a way that doesn't
correspond with any of the current testing conditions, it's possible that the pressure tube is moving. A
moving tube can cause a significant error. For instance, a tube that is attached both to the gauge and