3 wiring the inverter - general requirements, 1 protecting wire – conduit box, 2 wiring requirements – Magnum Energy ME Series User Manual
Page 21: 3 wire routing, 4 torque requirements
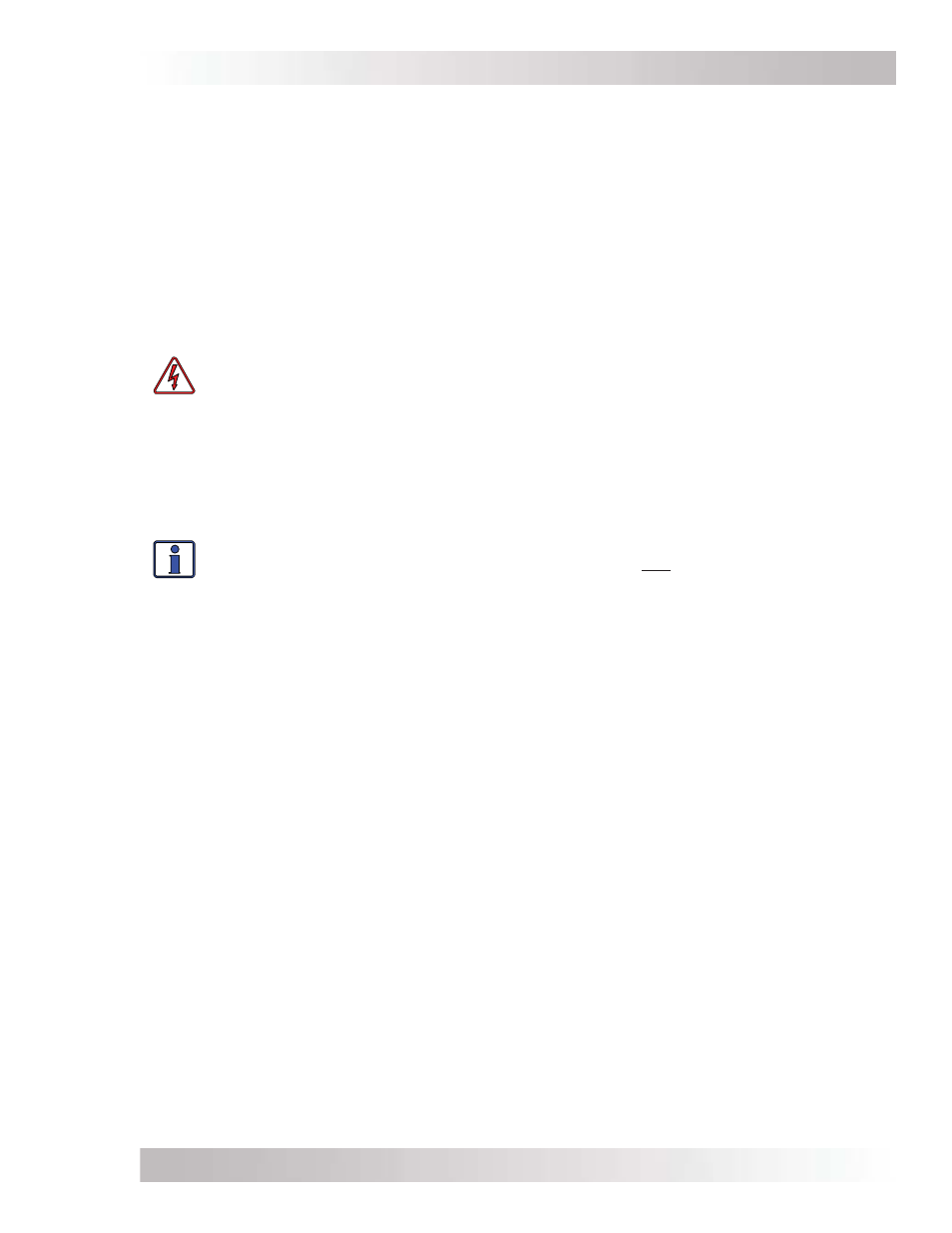
Page 13
©
2012 Magnum Energy, Inc.
Installation
2.3 Wiring the Inverter - General Requirements
This section describes the requirements and recommendations for wiring the ME Series inverter/
charger. Before wiring the inverter/charger, read all instructions.
All wiring should meet all local codes and industry standards, and be performed by
qualifi ed personnel such as a licensed electrician.
The NEC (National Electric Code, ANSI/NFPA 70) for the United States and the CEC (Canadian
Electrical Code) for Canada provide safe wiring standards. The NEC/CEC list requirements for wire
sizes, overcurrent protection, and installation methods/standards.
Inverter/charger systems involve power from multiple sources (e.g., inverter, generator, utility
power, batteries, etc.) which makes the wiring more hazardous and challenging.
The input and output AC and DC circuits are isolated from the inverter chassis. The inverter system
grounding is the responsibility of the installer in accordance with the NEC/CEC and local codes.
WARNING: Ensure the sources of DC power (i.e., batteries) and AC power (utility
power or AC generator) are de-energized (i.e., breakers opened, fuses removed)
before proceeding—to prevent accidental shock.
2.3.1
Protecting Wire – Conduit Box
The AC and DC wires to and from the inverter must be protected as required by code. This can
be done by using jacketed wires or by feeding the wires through conduit. Magnum offers a DC
conduit box (ME-CB), a single inverter enclosure (MMP Series), and a multiple inverter enclosure
(MP Series) that include the necessary AC and DC inverter breakers that allow both the AC and
DC conduit to be connected to the inverter.
Info: The strain reliefs can be removed and replaced with 3/4” grommets if you are using
either the ME-CB conduit box, MMP or MP enclosure, and the AC wires are individual
conductors (i.e., not jacketed).
2.3.2 Wiring
Requirements
• All conductors that are at risk for physical damage must be protected by tape, or placed
in a raceway.
• Always check for existing electrical, plumbing, or other areas of potential damage prior to
making cuts in structural surfaces or walls.
• Do not mix AC and DC wiring in the same panel unless specifi cally approved/designed for
both AC and DC wiring. Where DC wiring must cross AC or vice-versa, try to make the
wires 90° to one another at the crossing point.
• Both AC and DC overcurrent protection must be provided as part of the installation.
• The inverter requires a reliable negative and ground return path directly to the battery.
• Use only copper wires with a minimum temperature rating of 75°C.
2.3.3 Wire
Routing
Before connecting any wires, determine all wire routes to and from the inverter. Conductors passing
through walls, bulkheads, or other structural members must be protected to minimize insulation
damage, such as chafi ng. During installation, always avoid placing conductors near sources of
chafi ng caused by vibration or constant rubbing. Typical routing scenarios include:
• AC input wiring from utility power source to the inverter
• AC input wiring from an onboard generator (optional) to the inverter
• DC input wiring from the batteries to the inverter
• AC output wiring from the inverter to the coach’s AC main panel or to dedicated circuits
• Battery Temperature Sensor cable from the inverter to the batteries
• Remote control cable (optional) to the inverter
• Ground wiring to and from the inverter
2.3.4 Torque
Requirements
• Torque all AC wiring connections to 16 in lbf (1.8 N-m). Torque DC cable connections from
10 to 12 ft lbf (13.6 to 16.3 N-m).