Yaskawa YASNAC PC NC Programming Manual User Manual
Page 44
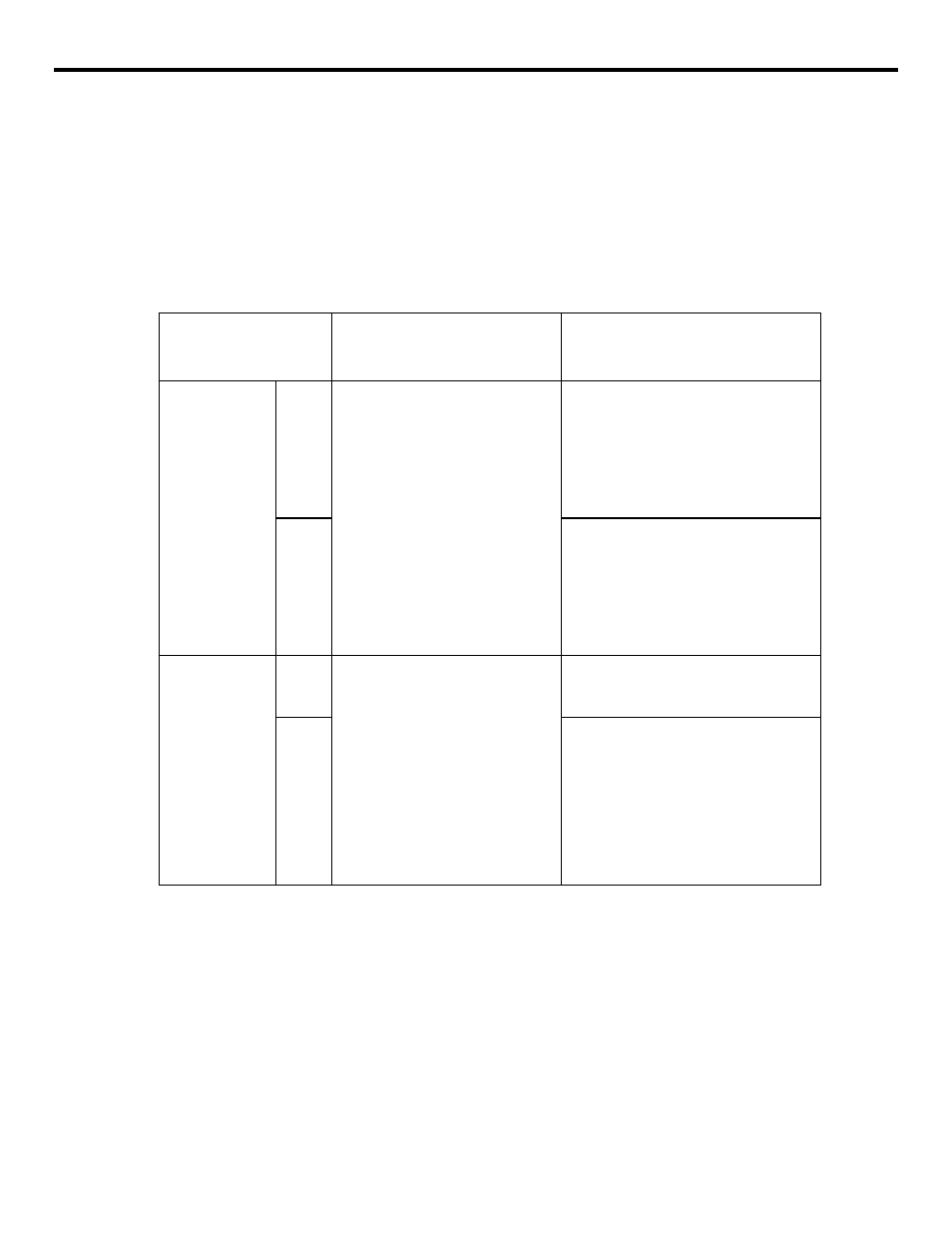
2 - 16
YASNAC PCNC Programming Manual
Chapter 2: Commands Calling Axis Movements
(e) Machine lock intervention
Concerning machine lock intervention, there are two types of operation: turning ON the
machine lock after suspending axis movement by using the feed hold function, and turning
OFF the machine lock after suspending axis movement again by using the feed hold func-
tion. Table 2.2.1.4 shows how the machine operates according to the machine lock inter-
vention.
Table 2.2.1.4
Machine Operation according to Machine Lock Intervention
Machine Lock Intervention
during Positioning to
Intermediate Positioning Point
Machine Lock Intervention during
Positioning to Reference Point
Machine Lock
OFF
Å ON
Low
speed
type
Although positioning is continued
to the intermediate positioning
point (position data display only),
movement to the reference point
is not executed.
Display data are not updated,
either.
Display data are infinitely updated.
Although positioning is made at the
reference point after the detection of
the actuation of the deceleration limit
switch, this cannot be detected due to
machine lock and, therefore, the dis-
play data are infinitely updated.
High
speed
type
In response to the machine lock inter-
vention, the axes stops moving. After
that, the display data (position data in
the workpiece coordinate system) are
updated until the reference point
return is completed. (without axis
movement)
Machine Lock
OFF
Å ON
Å OFF
Low
speed
type
The axes move in the workpiece
coordinate system up to the inter-
mediate positioning point. After
that, positioning is executed at the
reference point in the machine
coordinate system. Accordingly,
the reference point given in the
workpiece coordinate system is
offset.
However, the reference point in
the machine coordinate system is
not offset.
The axes move to the reference point.
High
speed
type
Actual axis position is displayed due
to the intervention of machine lock.
Accordingly, although the display data
(position data in the workpiece coordi-
nate system) agree with the reference
point, the axes are not located at the
reference point.