Contour train (cycle 25), 6 sl cy cles – HEIDENHAIN iTNC 530 (340 49x-02) User Manual
Page 409
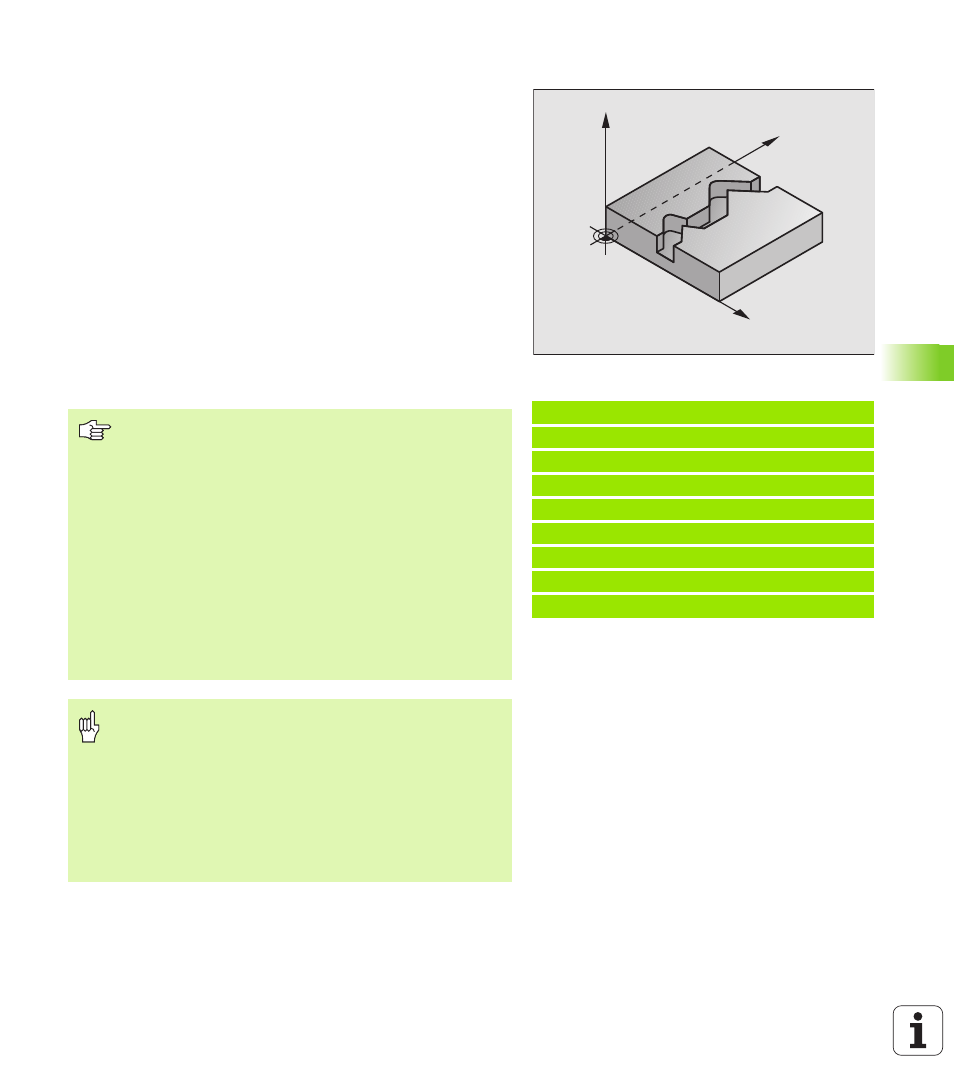
HEIDENHAIN iTNC 530
409
8.6 SL Cy
cles
CONTOUR TRAIN (Cycle 25)
In conjunction with Cycle 14 CONTOUR GEOMETRY, this cycle
facilitates the machining of open contours (i.e. where the starting
point of the contour is not the same as its end point).
Cycle 25 CONTOUR TRAIN offers considerable advantages over
machining an open contour using positioning blocks:
The TNC monitors the operation to prevent undercuts and surface
blemishes. It is recommended that you run a graphic simulation of
the contour before execution.
If the radius of the selected tool is too large, the corners of the
contour may have to be reworked.
The contour can be machined throughout by up-cut or by climb
milling. The type of milling even remains effective when the
contours are mirrored.
The tool can traverse back and forth for milling in several infeeds:
This results in faster machining.
Allowance values can be entered in order to perform repeated
rough-milling and finish-milling operations.
Example: NC blocks
62 CYCL DEF 25 CONTOUR TRAIN
Q1=-20
;MILLING DEPTH
Q3=+0
;ALLOWANCE FOR SIDE
Q5=+0
;SURFACE COORDINATE
Q7=+50
;CLEARANCE HEIGHT
Q10=+5
;INFEED DEPTH
Q11=100
;FEED RATE FOR PLUNGING
Q12=350
;FEED RATE FOR MILLING
Q15=-1
;CLIMB OR UP-CUT
Y
X
Z
Before programming, note the following:
The algebraic sign for the cycle parameter DEPTH
determines the working direction. If you program
DEPTH = 0, the cycle will not be executed.
The TNC takes only the first label of Cycle 14 CONTOUR
GEOMETRY into account.
The memory capacity for programming an SL cycle is
limited. You can program up to 8192 contour elements in
one SL cycle.
Cycle 20 CONTOUR DATA is not required.
Positions that are programmed in incremental dimensions
immediately after Cycle 25 are referenced to the position
of the tool at the end of the cycle.
Danger of collision!
To avoid collisions,
Do not program positions in incremental dimensions
immediately after Cycle 25 since they are referenced to
the position of the tool at the end of the cycle.
Move the tool to defined (absolute) positions in all main
axes, since the position of the tool at the end of the
cycle is not identical to the position of the tool at the
start of the cycle.