Tool change, 2 t ool d a ta – HEIDENHAIN TNC 320 (340 55x-05) ISO programming User Manual
Page 145
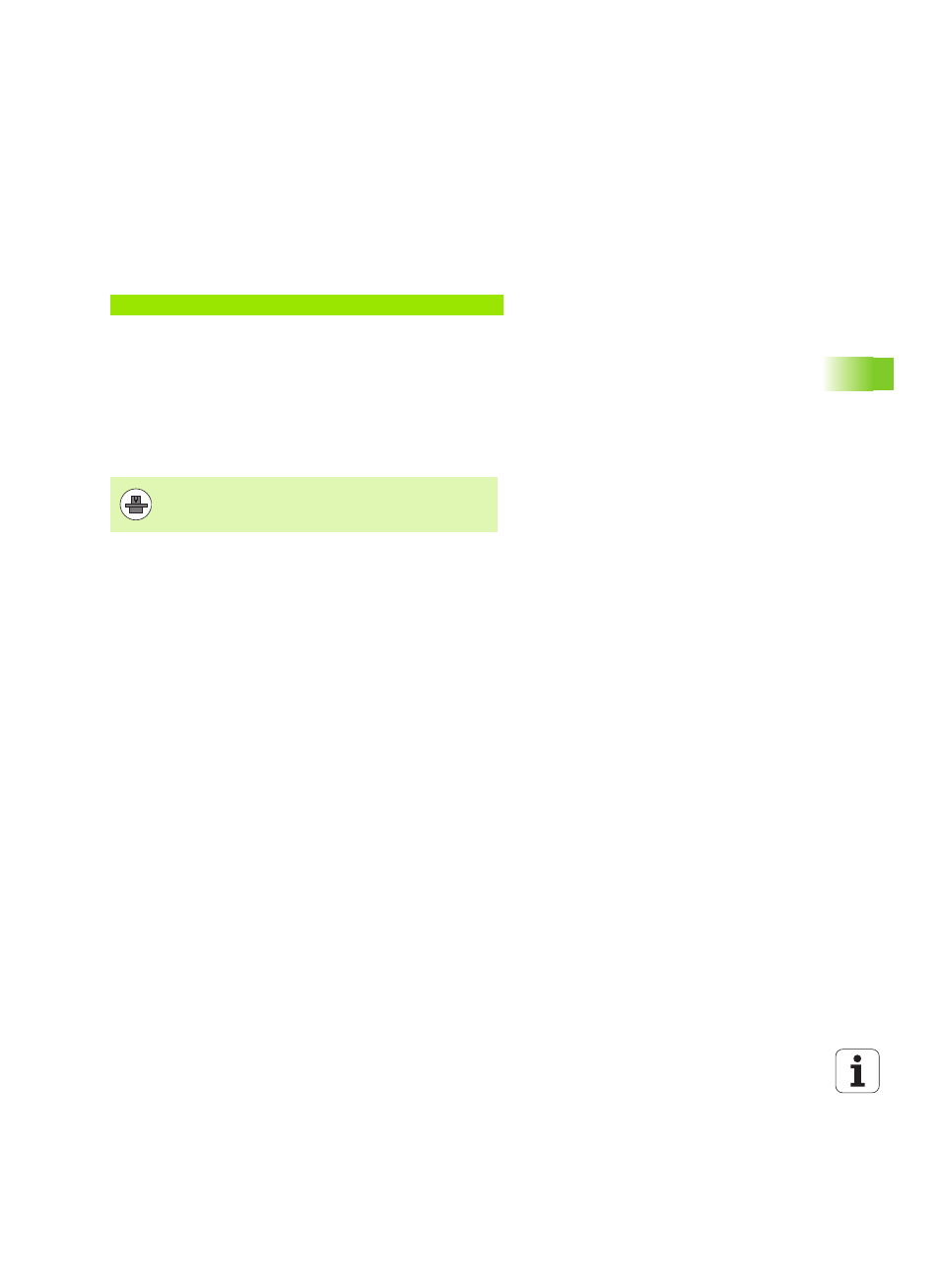
HEIDENHAIN TNC 320
145
5.2 T
ool D
a
ta
Example: Tool call
Call tool number 5 in the tool axis Z with a spindle speed of 2500 rpm
and a feed rate of 350 mm/min. The tool length is to be programmed
with an oversize of 0.2 mm, the tool radius 2 with an oversize of
0.05 mm, and the tool radius with an undersize of 1 mm.
The character D preceding L and R designates a delta value.
Tool preselection with tool tables
If you are working with tool tables, use G51 to preselect the next tool.
Simply enter the tool number or a corresponding Q parameter, or type
the tool name in quotation marks.
Tool change
Tool change position
The tool change position must be approachable without collision. With
the miscellaneous functions M91 and M92, you can enter machine-
based (rather than workpiece-based) coordinates for the tool change
position. If T 0 is programmed before the first tool call, the TNC moves
the tool spindle in the tool axis to a position that is independent of the
tool length.
Manual tool change
To change the tool manually, stop the spindle and move the tool to the
tool change position:
U
Move to the tool change position under program control.
U
Interrupt program run (see "Interrupting machining", page 384).
U
Change the tool.
U
Resume program run (see "Resuming program run after an
interruption", page 386).
Automatic tool change
If your machine tool has automatic tool changing capability, the
program run is not interrupted. When the TNC reaches a T it replaces
the inserted tool by another from the tool magazine.
N20 T 5.2 G17 S2500 DL+0.2 DR-1
The tool change function can vary depending on the
individual machine tool. The machine tool manual
provides further information.