Ultra-cut 100 xt – Tweco 100 Ultra-Cut Plasma Cutting System with Automated Gas Control User Manual
Page 199
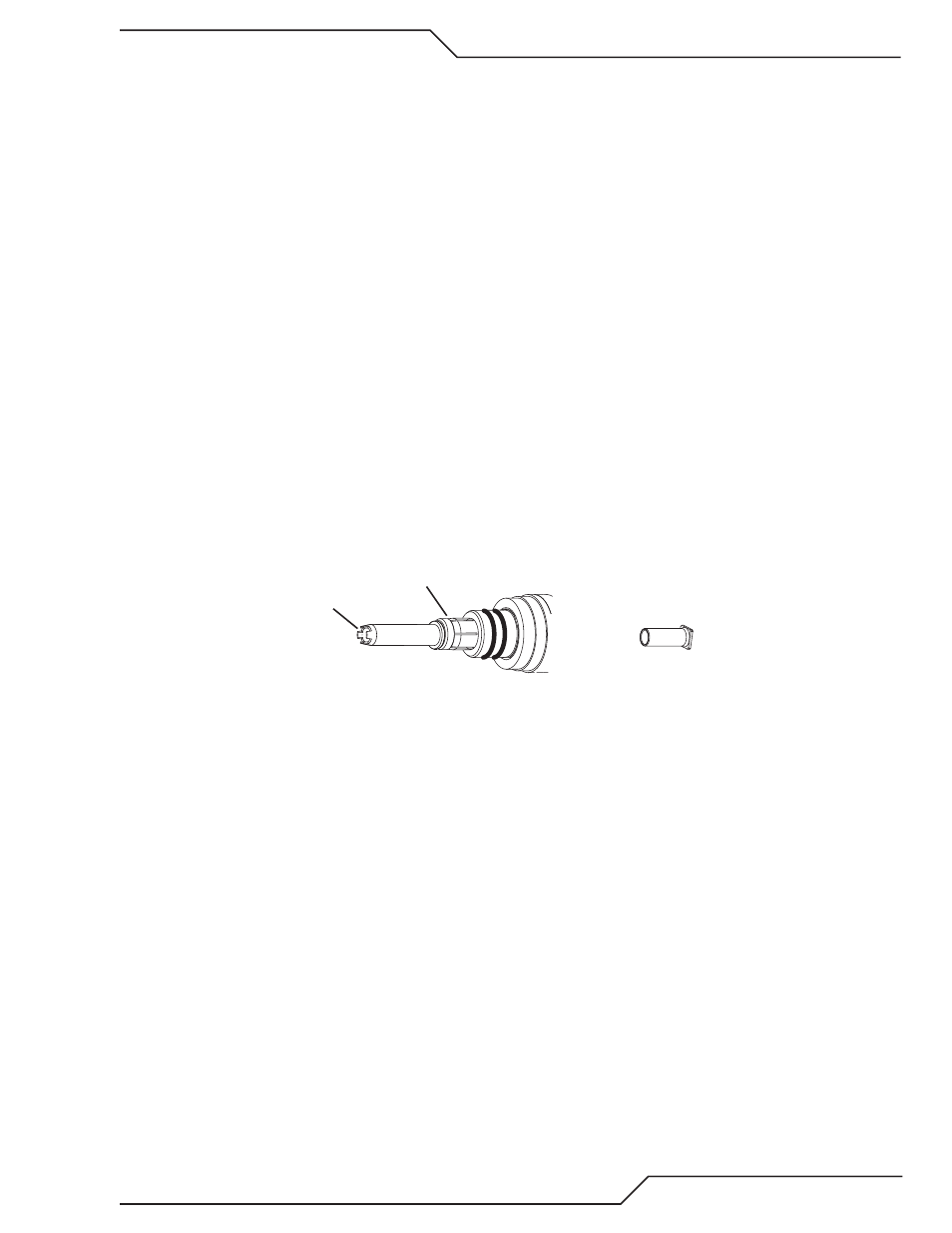
ULTRA-CUT 100 XT
Manual 0-5303
APPENDIX
A-75
Reasons for �0� faults (Coolant not flowing):
• In new installation, coolant has not circulated all the way through the leads. Add more coolant if neces-
sary and recycle the power to restart the pump and � minute timer.
• Coolant supply & return leads are reversed, check valve in torch coolant return prevents reverse flow.
• Torch parts removed or are wrong style so torch check valve shuts off flow.
• Torch coolant tube damaged or the tube extension (if required) missing.
• No power to pump motor.
• Pump/motor failure.
• Bypass valve defective or adjusted incorrectly.
Damaged Coolant Tube
Coolant tube includes a check valve at its upper end. When cartridge with consumables is not installed the
spring loaded coolant tube is fully extended closing the check valve preventing coolant from leaking out.
When consumables are in place they push the tube inward, opening the check valve, allowing coolant to flow.
The coolant tube has fingers on the end to contact the inside of the electrode and allow coolant to flow through
the openings between the fingers.
The fingers can be bent over or broken if reasonable care is not taken when the cartridge is not in place. If the
fingers are bent or broken it shortens the tube so the consumables may not push the tube in enough to open
the check valve resulting in no coolant flow. The coolant tube assembly may be replaced separately from the
torch head.
Some consumables use an extension on the coolant tube. A missing extension will not allow the check valve
to open.
Art # 12312
Coolant Tube Extension
Fingers
Internal Check Valve
No Power to the Pump Motor
The pump motor is powered by 230 VAC controlled by the MC3 control relay. During the � minutes after turning
on power, before the �0� fault code is displayed, measure for 230 VAC at the motor connector J1� pin 1 to pin 3.
a. If the pump motor is not getting 230 VAC, measure for 24 VAC on the coil of MC3. If present and the relay
contacts aren’t closed the relay is defective. Note, the coil is rectified so you won’t measure continuity of
even a good coil.
b. If 24 VAC is not on the MC3 coil check for D27 on the relay board being ON. If it’s on the Relay board should
be providing the 24 VAC so if it’s not the Relay board may be defective. Measure for 24 VAC at J9-6 to J9-12
on the Relay board. If 24 VAC is present and D27 is on, the Relay board or the wire harness is defective.
c. If D27 is not on, measure on the CCM I/O board between TP3 and the common at TP1. It should be low,
near zero volts. If not the CCM is probably defective. Jumper TP3 (I/O board) to TP1. If the pump comes
on now replace the CCM.