Valve sizing and selection cont – Powers 596 Series Flowrite II Heavy Duty Control Valves - Type MI Mixing User Manual
Page 4
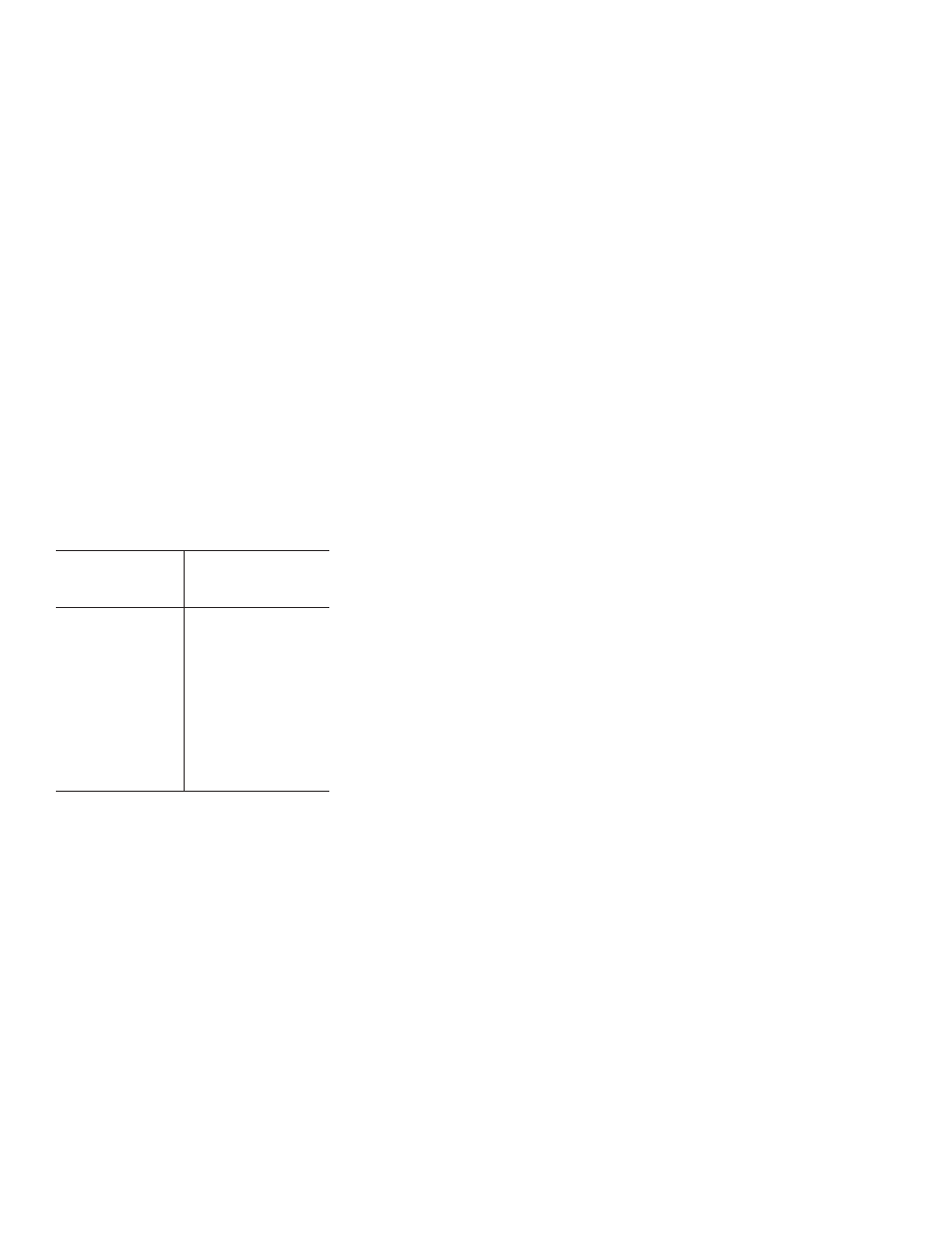
4
Cavitation, Flashing and Choked Flow:
Limitations on Valve Pressure Drop
A concern in high temperature water systems is the potential
for cavitation, which is caused by the downstream pressure
being lower than that of the vapor pressure of the fluid. This
basically causes the water to "boil" and can result in reduced
flow/capacity, excessive noise, vibration, wear and should be
avoided if possible. If the pressure downstream of the area
restriction rises rapidly above the vapor pressure, the vapor
bubbles will collapse violently (implode). The bubble collapse is
an affirmation of cavitation. Use the following equation below
to estimate the maximum allowable pressure drop across the
valve.
Flashing is a phenomenon where the flowing high temperature
water inlet experiences a significant pressure drop, with the
outlet pressure below the vapor pressure of the water (as in
cavitation) and is converted to a vapor within the control region
of the valve.
This can also produce a choked flow condition where the rapid-
ly expanding vapor prohibits any increase in flow, even though
P1 (inlet) pressure is increased.
Valve Sizing and Selection cont.
n
Pmax = 0.5 (P1 – Pv)
Where:
Pmax = Maximum allowable pressure drop
P1 = Absolute inlet pressure (psia)
Pv = Absolute vapor pressure (refer to psia - Table 2)
Absolute pressure = gage pressure + 14.7
Table-2 Vapor Pressure of Water
Water
Vapor
Water
Vapor
Temp.
Pressure
Temp.
Pressure
(°F)
(psia)
(°F)
(psia)
40
0.12
140
2.89
50
0.18
150
3.72
60
0.26
160
4.74
70
0.36
170
5.99
80
0.51
180
7.51
90
0.70
190
9.34
100
0.95
200
11.53
110
1.28
210
14.12
120
1.69
220
17.19
130
2.22
230
20.78