12 setting up inverting fault avoidance – Rockwell Automation WebPak 3000 DC Drives Hardware Reference, Installation and Troubleshooting User Manual
Page 57
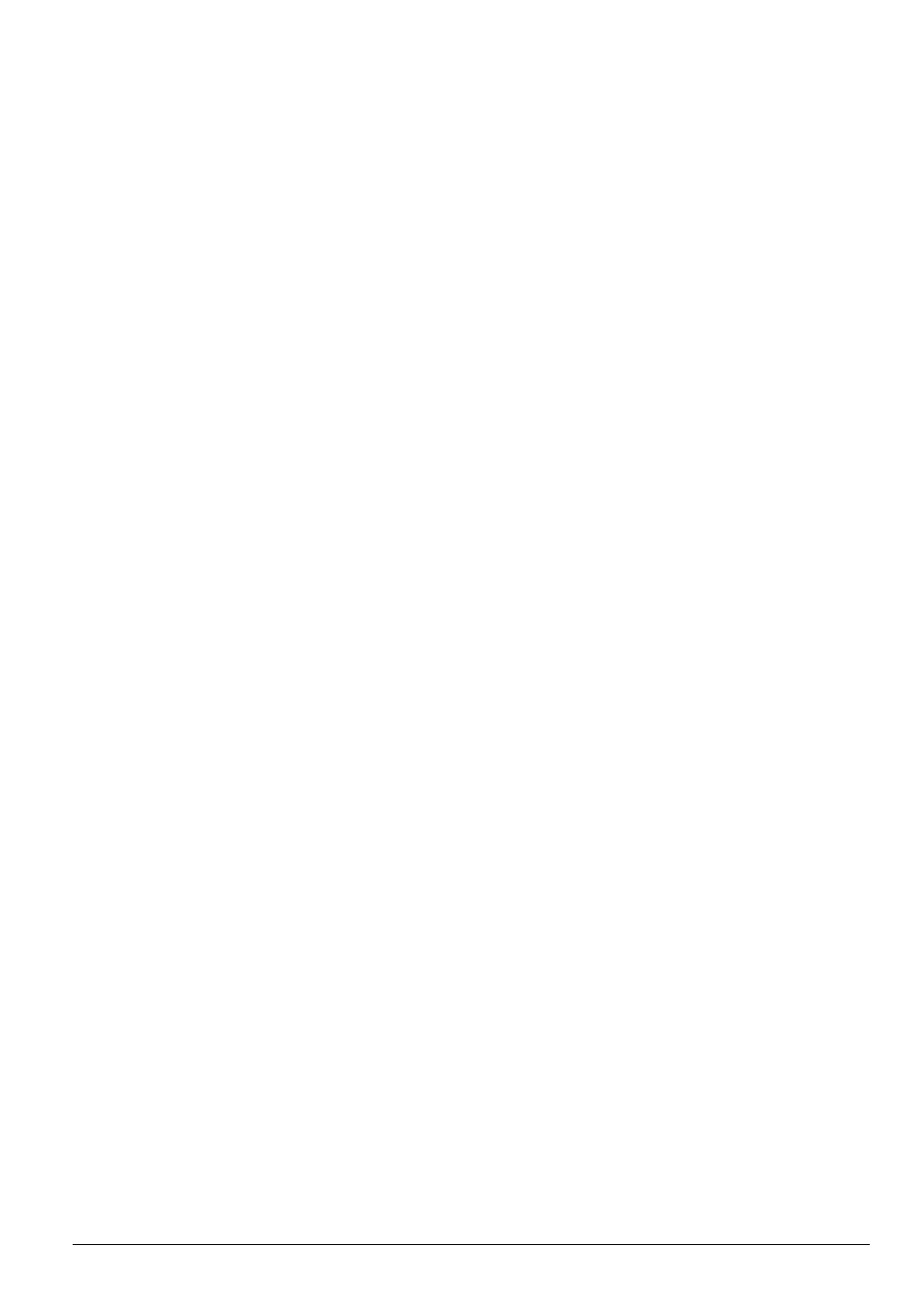
Troubleshooting/Diagnostics
4-15
4.11
Setting Reversed Tachometer or Reversed Encoder Lead Detection
The WebPak 3000 drive includes an algorithm for detecting reversed speed feedback wiring.
The logic verifies that the difference between the speed reference and the speed feedback is
greater than the threshold set by
TACH LEAD FLT THRESH
(P.227) for the amount of time set by
TACH LEAD FLT DELAY
(P.228). When the threshold is greater than the difference for the
specified delay, and the speed reference and speed feedback are opposite in polarity, a
REVERSED TACH LEADS
fault is generated (fault F00014). For a description of
TACH LEAD FLT
THRESH
(P.227) and
TACH LEAD FLT DELAY
(P.228), refer to the WebPak 3000 Software
Reference manual.
Fault F00014 can also be caused by an overhauling load, improper drive tuning, or a
tachometer or encoder loss.
The tachometer lead fault parameters have default values that are set so that reversed
tachometer lead detection is effectively disabled. You must empirically determine values for
these parameters so that reversed tachometer or encoder wiring can be detected without
generating nuisance faults.
The ability to check for reversed tachometer lead faults is useful for machine manufacturers
that require their equipment to be disassembled for shipping and reassembled and rewired at a
customer site.
4.12
Setting Up Inverting Fault Avoidance
An inverting fault is an uncontrollable high current resulting from commutation failure. It is
typically caused by an excessive armature-to-line voltage ratio, which can be caused by
situations such as a line voltage dip, a poorly tuned field regulator, or an overhauling load.
Inverting faults can also be caused by thyristor misfiring induced by noise, or a current minor
loop rate limit that is set too fast.
Inverting faults can cause:
•
clearing of the AC line fuses that protect the armature thyristors
•
tripping of an inverting fault circuit breaker
•
clearing of an armature DC fuse
•
loss of thyristors
•
degradation of commutator due to high current
•
flashover in the motor or power unit
Inverting faults are only a concern in regenerative DC drive applications. Typically, a
regenerative drive application uses a regenerative power unit (S6R).
Inverting fault avoidance can be used in regenerative drive applications to prevent the
occurrence of an inverting fault. If inverting fault avoidance is used, the drive recognizes
conditions that could lead to an inverting fault and dynamically adjusts drive operation to
prevent an inverting fault.
For a description of parameter
INV FAULT AVOID SEL
(P.312), refer to the WebPak 3000
Software Reference manual.