Rockwell Automation 1746-BLM Blow Molding Module Installation Instructions User Manual
Page 7
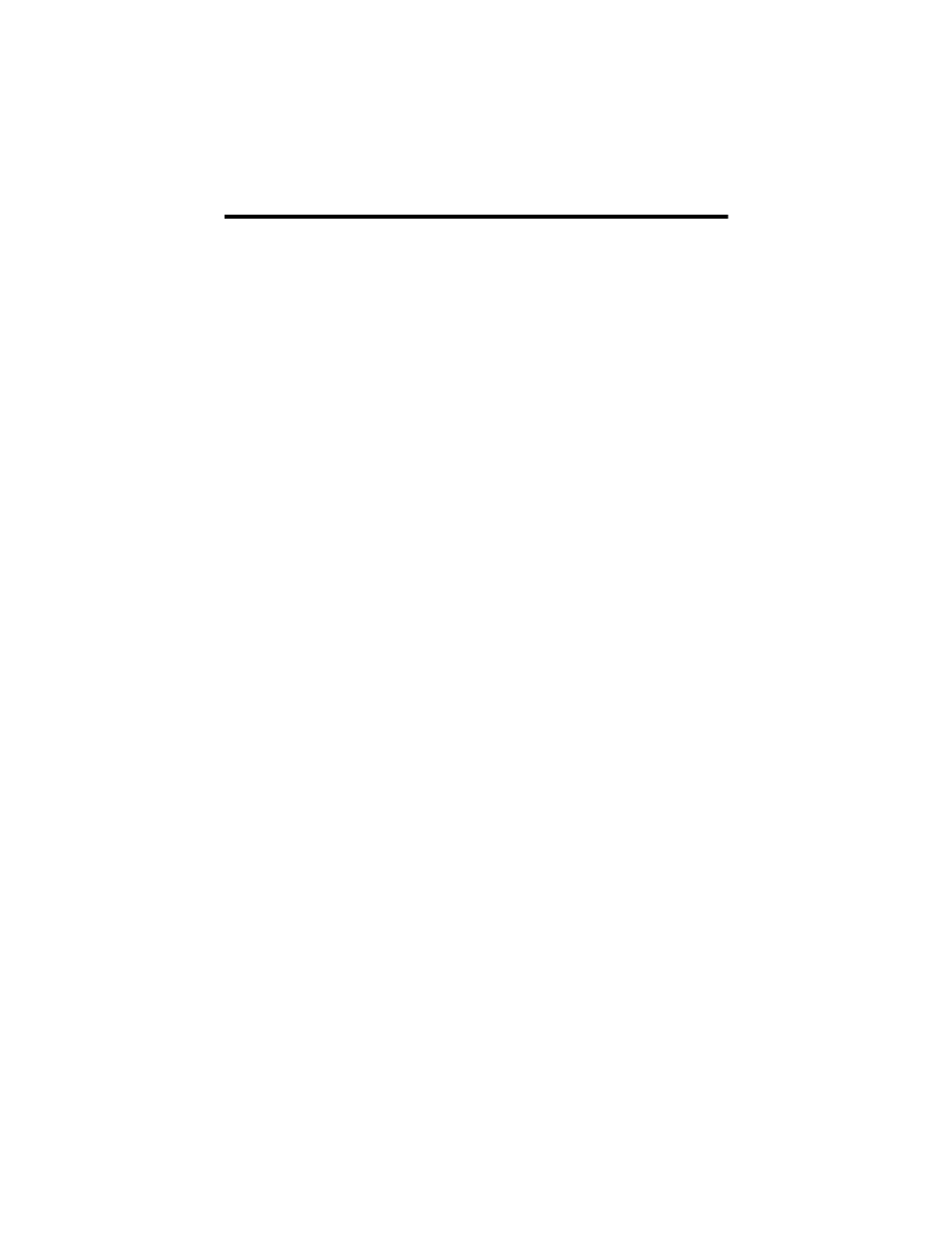
Blow-molding Module 7
Publication 1746-IN014B-EN-P - January 2001
M0 File
contains four axis control structures and five setpoint profiles.
Each axis has a variety of PID and profiling options, controlled
by its axis control structure. Each axis also has a unique
256-point setpoint profile. A single master setpoint profile is used
with an “interpolate” command to ease the task of generating
setpoint profiles.
Entries in the M0 File are written by move or copy instructions in
ladder program. Unlike changes made to the Output File, which
are automatically detected by the module, the module must be
explicitly instructed to download axis-control structures and
setpoint profiles from shared memory (done by setting bits in the
Output File).
M1 File
contains four axis-status structures, four process-variable profiles,
and a single interpolated profile. Axis-status structures are copies
of respective axis-control structures, except that status
information has been inserted by the module. Each
process-variable profile provides a record of the actual position
response to a setpoint profile. The interpolated profile is the
result of either a linear or natural cubic-spline interpolation
performed between the setpoints specified in the master setpoint
profile.
Unlike the Input File, which is automatically updated, the
module must be explicitly instructed to upload axis-status
structures, process variable profiles, and the interpolated profile
to shared memory (done by setting bits in the Output File).
Entries in this file are then read by move or copy instructions in
ladder program.
Handshake with control and status bits
To ease the task of synchronizing module operations with your ladder program, all
control bits in the Output File have a corresponding status bit in the Input File.
Upon detecting a change in a control bit from zero to one, the module performs
any associated processing and then acknowledges completion by setting the
corresponding status bit to one. The status bit will remain set as long as the control
bit remains set. When the control bit is cleared, the status bit will be cleared
immediately in acknowledgment.
Exceptions to this protocol are the profile enable control/status bits and the
control/status bits for the digital inputs and digital outputs. See step 9 for complete
descriptions of these and other bits.