Using timing diagrams, Figure 1 example diagrams for position-based model, Figure 2 example diagrams for time-based mode – Rockwell Automation 1746-BLM Blow Molding Module Installation Instructions User Manual
Page 34
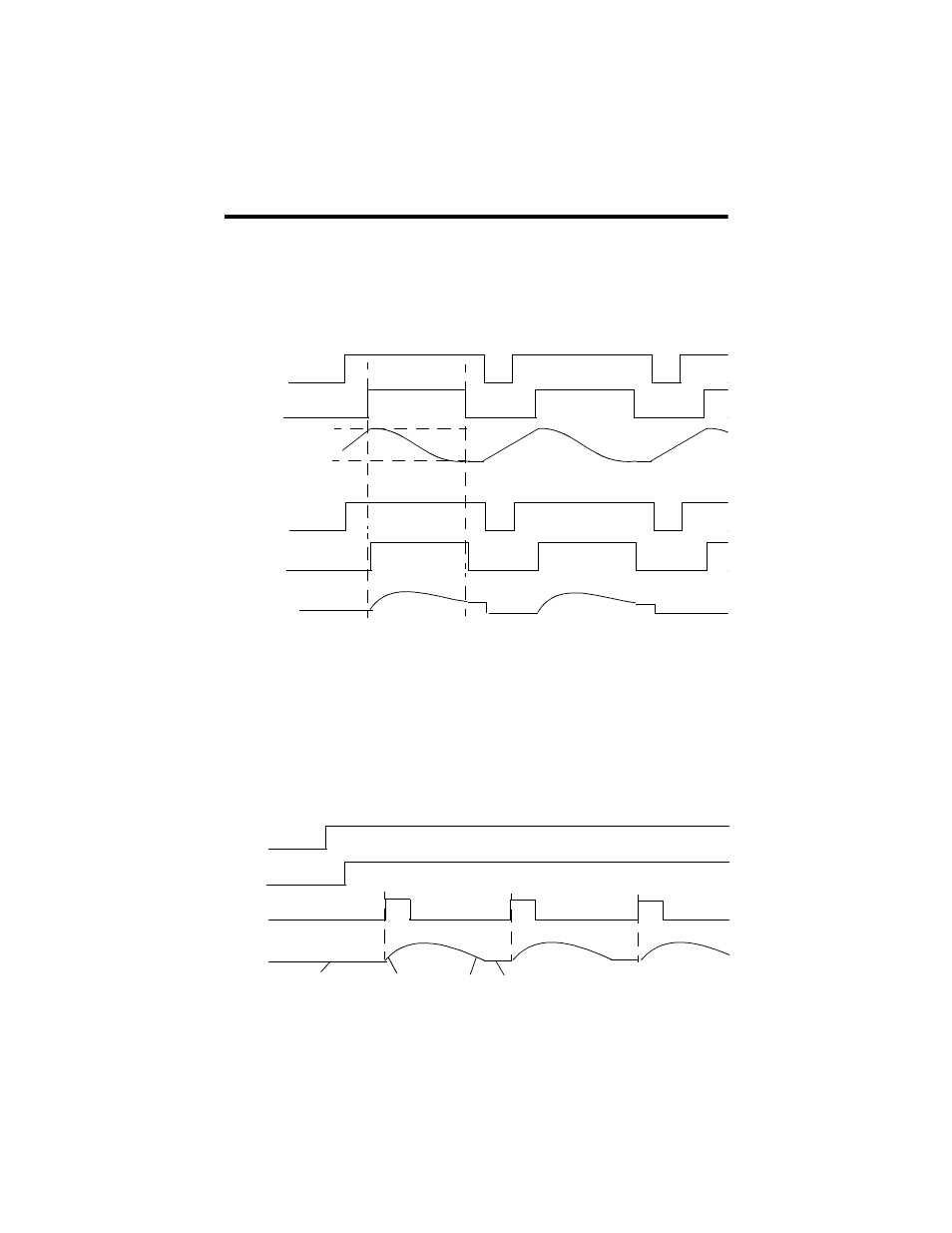
34 Blow-molding Module
Publication 1746-IN014B-EN-P - January 2001
Using Timing Diagrams
Study these timing diagrams for position-based and time-based modes of operation.
Figure 1 Example Diagrams for Position-based Model
(see wiring on page 23)
Notes:
(1) Profile status bits are set when profile enable bits are set and the independent axis position reaches step 0.
shot size
≥
independent axis position
≥
(255/256)(shot size - zero scale)
(2) Profile status bits are cleared when the independent axis position reaches step 255.
independent axis position
≤
(shot size - zero scale)/256
(3) Axis position setpoint retains its previous value until the profile enable bit is disabled.
(4) The highest priority enabled hold value determines the axis setpoint when profiling is disabled:
the mandrel will hold constant position, the ram will hold constant velocity
(for additional information, see Step 5, page 26).
Figure 2 Example Diagrams for Time-based Mode
(see wiring on page 23)
Axis 2 profile enable
O:e.2/0
Axis 2 profile status
I:e.2/0
Axis 2 position
Velocity-controlled Ram
Position-controlled Mandrel
Axis 1 profile enable
O:e.0/0
Axis 1 profile status
I:e.0/0
Axis 1 position
Profile
step 0
Profile
step 255
zero scale
shot size
(1)
(2)
(3)
(4)
(1)
(2)
(3)
(4)
Axis 2 profile enable
O:e.2/0
Axis 2 profile status
I:e.2/0
Synchronization Input
(from ladder logic or hardware
Axis 2 position
Profile
step 0
Profile
step 255
Last profile
setpoint
Highest-priority
hold value