Step: 12 tuning a pid loop, Tuning a pid loop, Introduction – Rockwell Automation 1746-BLM Blow Molding Module Installation Instructions User Manual
Page 38
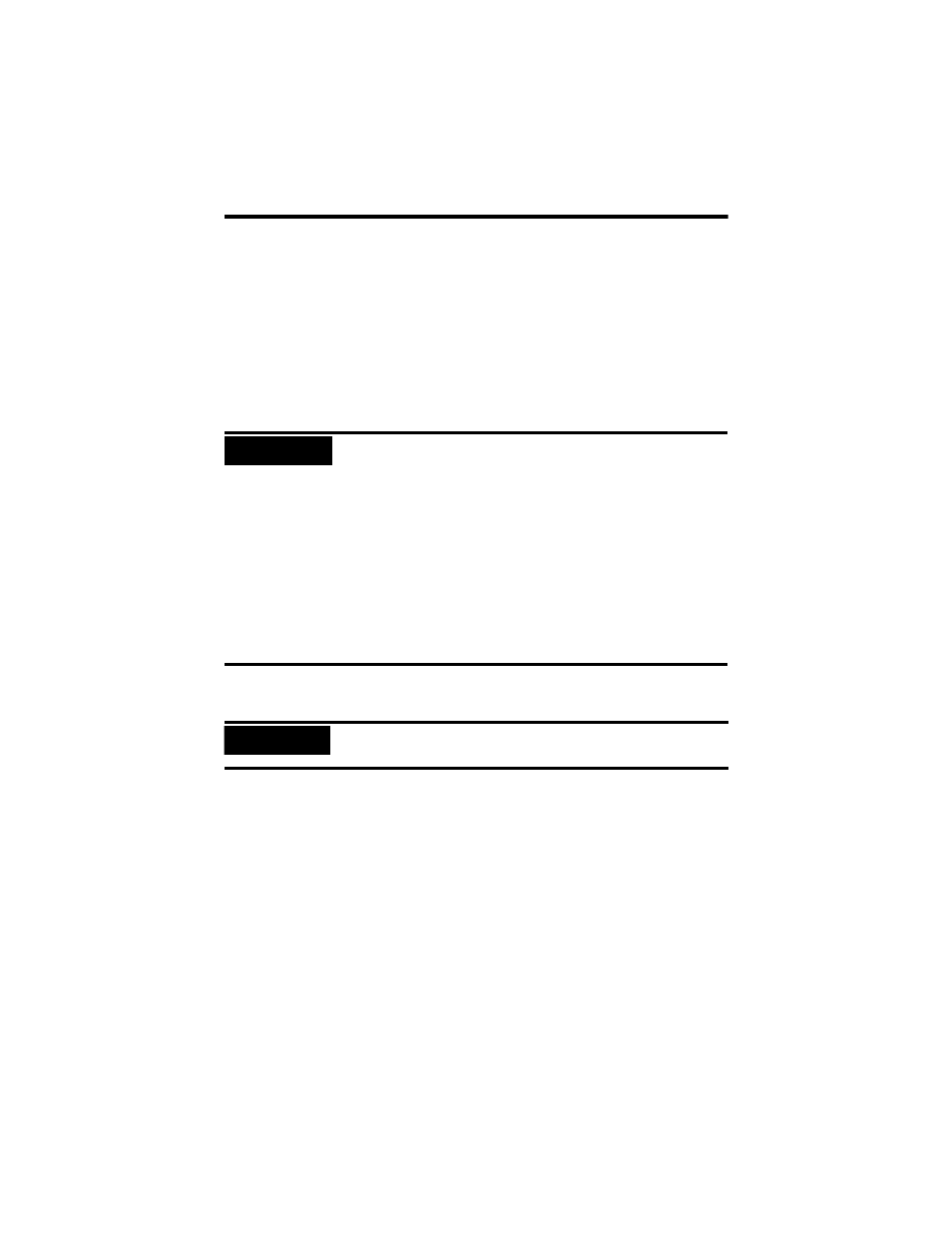
38 Blow-molding Module
Publication 1746-IN014B-EN-P - January 2001
Step: 12 Tuning a PID Loop
Use the following standard PID tuning method to tune the module’s PID control
loops:
Introduction
In the module’s feedback control system, steady-state error using the proportional
term is 100% x 1/(1+K), where K = proportional gain.
Procedure
1. Start with a proportional gain of one; with integral and derivative terms
disabled.
2. Double the proportional gain until oscillation just begins to occur.
3. Halve the proportional gain.
4. Enable the integral term using a large integral time (e.g. 1 sec.)
5. Halve the integral time until oscillation just begins to occur.
6. Double the integral time.
7. Fine tune the proportional gain, integral time, and derivative time to achieve
optimum results.
EXAMPLE
If the proportional gain is 9, the steady state error is an
unacceptably high 10%. At the maximum proportional gain
of 256, the error is better at 0.4%, but such a high gain may
cause instability. Using the integral term forces the
steady-state error to zero without adverse effects on system
stability. This is especially important in position-based
operation, where the position of the independent axis (ram)
must reach the first and last steps as follows:
•
step 0 (within 1/256
th
of shot size) before a profile may
begin
•
step 255 (within 1/256
th
of zero-scale) before a profile
may complete
IMPORTANT
Monitor the response to a setpoint change after performing
each of the subsequent steps.