2 compact decentralised i/o system, Compact decentralised i/o system, Function library lenzeiosystem.lib – Lenze DDS Function library IOSystem User Manual
Page 15: Application examples
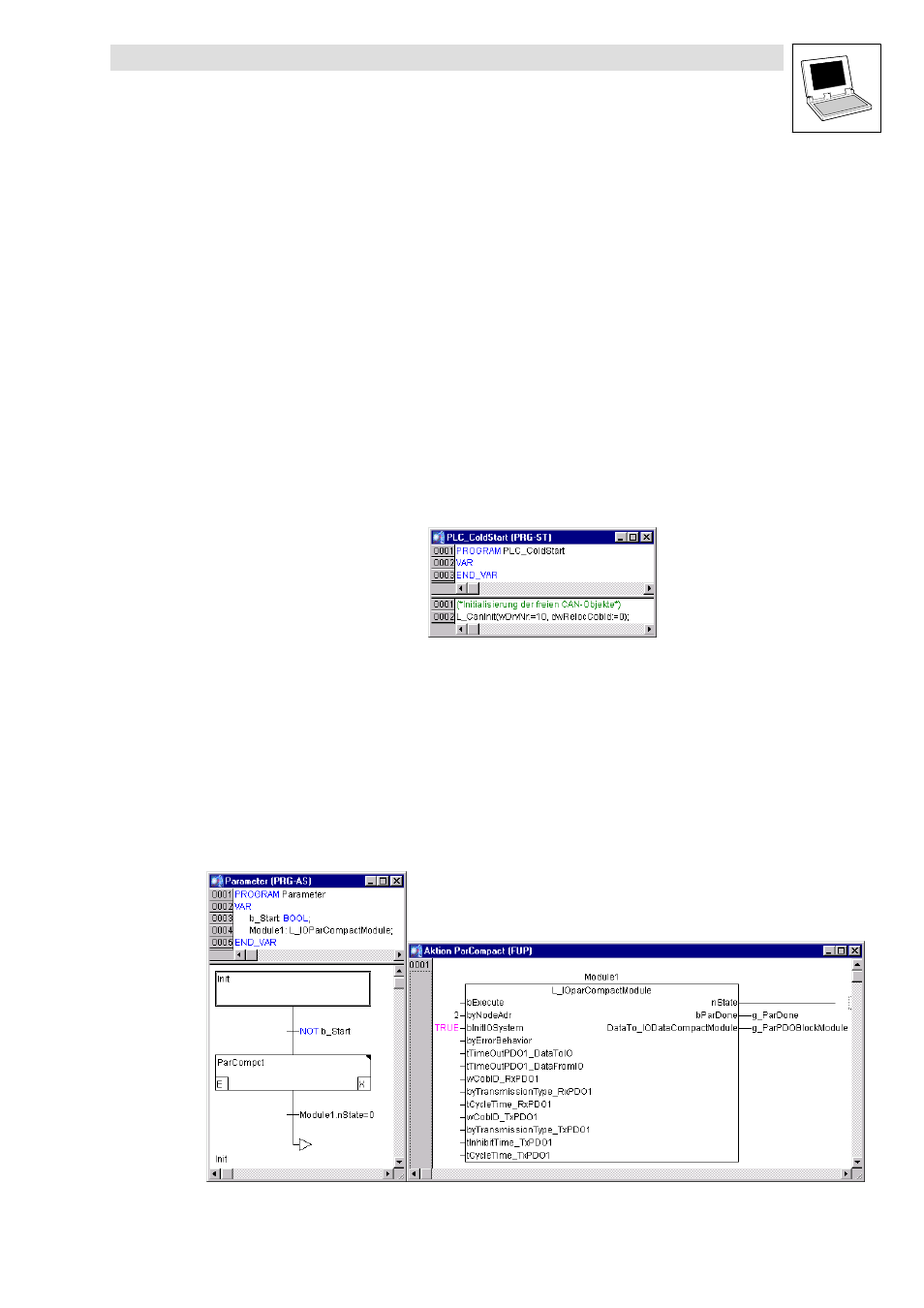
Function library LenzeIOSystem.lib
Application examples
3.2
Compact decentralised I/O system
3−5
L
LenzeIOSystem.lib EN 1.7
3.2
Compact decentralised I/O system
The compact module EPM − T832 with 24 digital inputs and 8 digital outputs is integrated into a PLC
program with the help of LenzeIOSystem.lib.
During this process, the following steps must be carried out in the given order:
1. Initialise the CAN driver
2. Parameterise the communication conditions
3. Program the process data exchange between PLC and I/O system
4. Initialise the codes
Initialising the CAN driver
Communication between the PLC and the I/O system is based on "unassigned CAN objects"
(control, alarm, diagnostics...). These objects are available in DDS from version 2.x onwards.
To initialise the unassigned CAN objects, the function L_CANInit must be requested once only in the
system POU PLC_ColdStart.
Parameterising the communication conditions
Function block L_IOParCompactModule for parameterising the communication conditions is
integrated into the SFC editor and necessarily is to be used in every project. This function block
specifies the communication parameters in the I/O system.
The values are transferred to the process data block L_IOCompactModule as a structure (STRUCT)
in order to match the communication parameters of the devices (controller and I/O system).
On program execution, this step is executed once only at the beginning.
Then the Parameter program that must be generated in the SFC editor follows. With the invocation
of the function block instance, the step ParCompact has the action generated in the FBD editor.