9300 servo plc, Appendix – Lenze Drive PLC Developer Studio 9300 Servo PLC (V8.x) User Manual
Page 118
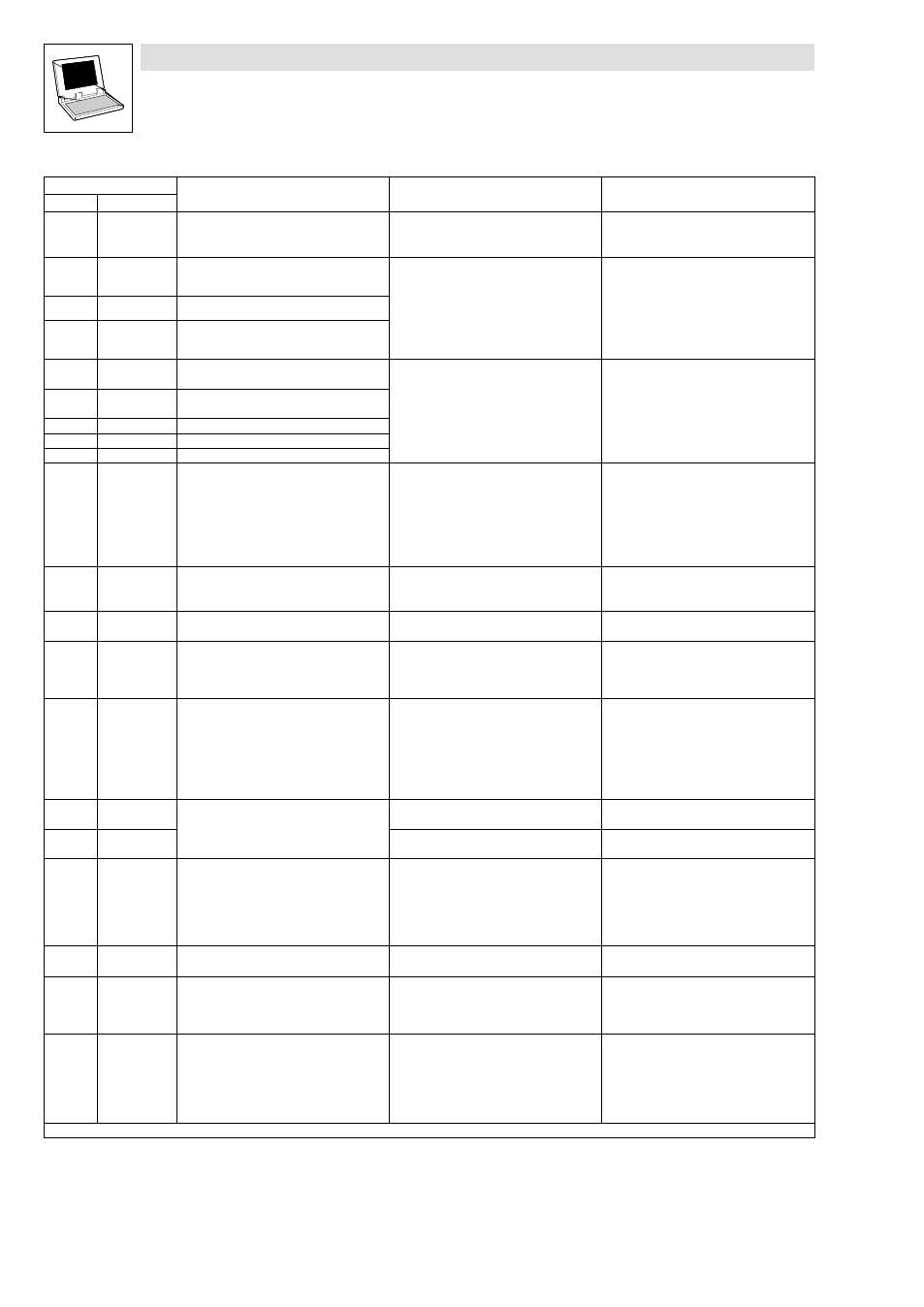
9300 Servo PLC
Appendix
3−16
L
9300 Servo PLC EN 5.0
Fault message
Remedy
Cause
Description
No.
Remedy
Cause
Description
Display
x200
Nmax
Maximum speed (C0596) has been
exceeded.
·
Active load (e.g. for hoists) is too high
·
Drive is not speed−controlled, torque is
excessively limited.
·
Check drive dimensioning.
·
Possibly increase torque limit.
·
Switch off monitoring (C0607 = 3).
0201
overrun
Task1
Time−out in task 1 (ID 2)
Task processing takes longer than the
monitoring time set.
·
Adjust the length of the task runtime.
·
Adjust monitoring time.
·
Determine the cause of time−out by
checking the task runtime at the task
monitor.
·
Swap out time−critical program parts in
a slower task.
...
...
...
0208
overrun
Task8
Time−out in task 8 (ID 9)
0209
float
Sys−T
Float error in system task (ID 0)
Error in real calculation
(e. g. division by 0)
Check calculations (program code).
0210
float
Cycl.−T
Float error in cyclic task (PLC_PRG ID 1)
0211
float Task1
Float error in task 1 (ID 2)
...
...
...
0218
float Task8
Float error in task 8 (ID 9)
0219
overrun
Cyc.−T
Time−out in cyclic task (PLC_PRG ID 1)
Task processing takes longer than the
monitoring time set.
·
Adjust the length of the task runtime.
·
Adjust monitoring time.
·
Determine the cause of time−out by
checking the task runtime at the task
monitor.
·
Swap out time−critical program parts in
a slower task.
0220
noT−Fkt
Credit
Not enough technology units available.
A program with technology functions has
been tried to be loaded to a controller not
providing the corresponding units.
·
Use technology variant of the controller.
·
Contact Lenze, if necessary.
0230
No
Program
Missing PLC program
No PLC program loaded.
Load PLC program.
0231
Unallowed
Lib
PLC program calls invalid library function.
In the PLC program a library function has
been called which is not supported by the
controller (e.g. because the corresponding
hardware is missing).
·
Remove library function or ensure that
the corresponding hardware is available.
·
Contact Lenze, if necessary.
0232
NoCam
Data
Motion profiles (cam data) are not available. When calling functions of the function
library LenzeCamControl.lib it was
detected that there are no motion profiles
(CAM data) loaded in the memory of the
controller.
·
Ensure that the valid cam data has been
attached to the project via the DDS CAM
support.
·
Reload the PLC program into the
controller. (Possibly the command
Online
WReset (origin) has been
executed in DDS.)
x240
ovrTrans
Queue
"Free CAN objects" error
Overflow of the transmit request memory
·
Reduce the number of transmit requests.
·
Prolong the cycle time.
x241
ovr Receive
Too many receive telegrams
Reduce the number of telegrams on the
system bus (CAN).
x250
2.Flash Err
Error when the FLASH memory is accessed
The PLC program tries to access
non−available or defect FLASH memory
Make sure that the PLC has the
corresponding FLASH memory. If not, please
contact Lenze.
After troubleshooting: Deenergise the
device completely (disconnect 24 V
supply, discharge DC bus)!
x251
AddData CsErr
Error during FLASH memory access
Check sum error occurred when loading
data into the FLASH memory
Check the checksum of the file to be loaded
and repeat the data transfer.
x252
AddData DlErr
Error during FLASH memory access
An error occurred when downloading the
data into the FLASH memory (e.g. time−out,
transmission error, mains failure during
transmission)
Check/repeat data transfer.
x260
Err Node
Guard
"Life guarding event"
The controller configured as a CAN slave
does not receive a "Node Guarding"
telegram from the CAN master within the
"Node Life Time".
·
Check wiring at X4.
·
Check CAN configuration.
·
Ensure that "node guarding" has been
activated in the CAN master
·
Adapt the "node life time" (C0383) to
CAN master setting.
x: 0 = TRIP, 1 = Message, 2 = Warning, 3 = FAIL−QSP