AEM 30-6905 Universal Programmable EMS-4 User Manual
Page 186
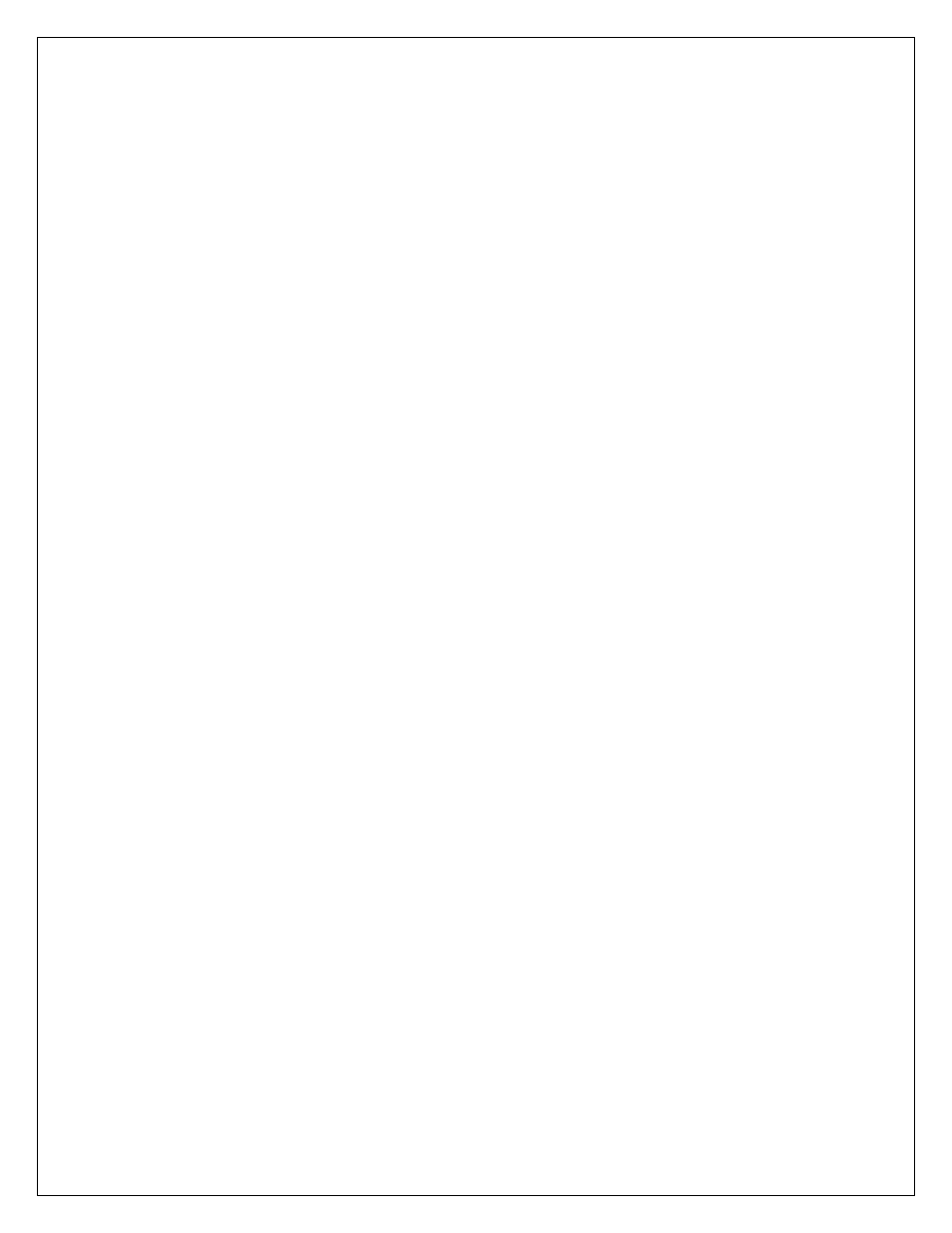
Page 186 of 279 EMS-4 Install and Tuning Guide_Rev 1.6
Too lean of an air/fuel mixture.
The following tuning adjustments can be performed on an engine to reduce or eliminate
knocking:
Reduce ignition timing.
Verify that the air/fuel mixture is adequate for your engine set up.
Verify that the spark plugs are of proper heat range.
Preignition is the ignition of the charge in the combustion chamber before the spark occurs. This
type of ignition is caused by a very hot, or even incandescent surface in the combustion
chamber. These “hot spots” can be an overheated spark plug, a glowing remnant of carbon in
the chamber or even a hot exhaust valve edge. The preignition condition flame front rapidly
expands while the piston is still on its way up the bore. Due to the very high pressure generated
by the expanding flame front and the piston approaching TDC, the combustion chamber
pressure rises rapidly causing audible knocking. Detonation and preignition typically have a
cause and effect relationship; when detonation is prolonged and overheats the spark plug to the
point where the tip glows, preignition occurs. Preventative measures can be taken to avoid
preignition by using spark plugs with the correct heat range, avoiding detonation by using fuel
with the correct octane rating for your application, and when building an engine, ensuring that
there are no machined components with sharp corners in the combustion chamber. Also, the
cooling system must be in good working condition to effectively cool the combustion chamber.
Sustained operation of an engine in either of these conditions can result in severe engine
damage.
At low manifold pressure the flame front is slower due to the low density of mixture in the
combustion chamber. Because peak manifold pressure is optimal at 15-20 degrees ATDC and
the burn rate is slower at very low manifold pressure, the ignition point must be started earlier.
The main ignition map typically has high ignition timing values during times of low manifold
pressure and high RPM, which gradually decreases at load increases.
As the throttle is opened, the density of the mixture increases and the flame propagation
increases in speed. The timing must be reduced as load and RPM increase to keep the peak
pressure at approximately the same point and reduce the chances of knocking.
With forced induction engines, the burn rate increases as charge density is increased. In this
example, timing must be reduced because of the faster burn rate, and to further reduce the
chances of knocking. On forced induction engines, the inlet charge temperature is elevated
because of the heat generated by compressing the air. Utilizing an intercooler or after-cooling
system usually helps reduce the inlet charge temperature. But in many cases this still will not
bring the inlet charge down to ambient temperature, making the engine more susceptible to
knocking.
Remove the spark plugs each time the timing is increased to a higher value and check for signs
of detonation. The spark plug is the best indicator of what is happening in the engine because it
is such an integral part of the combustion chamber. If you see small flecks of black deposits, or