AEM 30-6905 Universal Programmable EMS-4 User Manual
Page 177
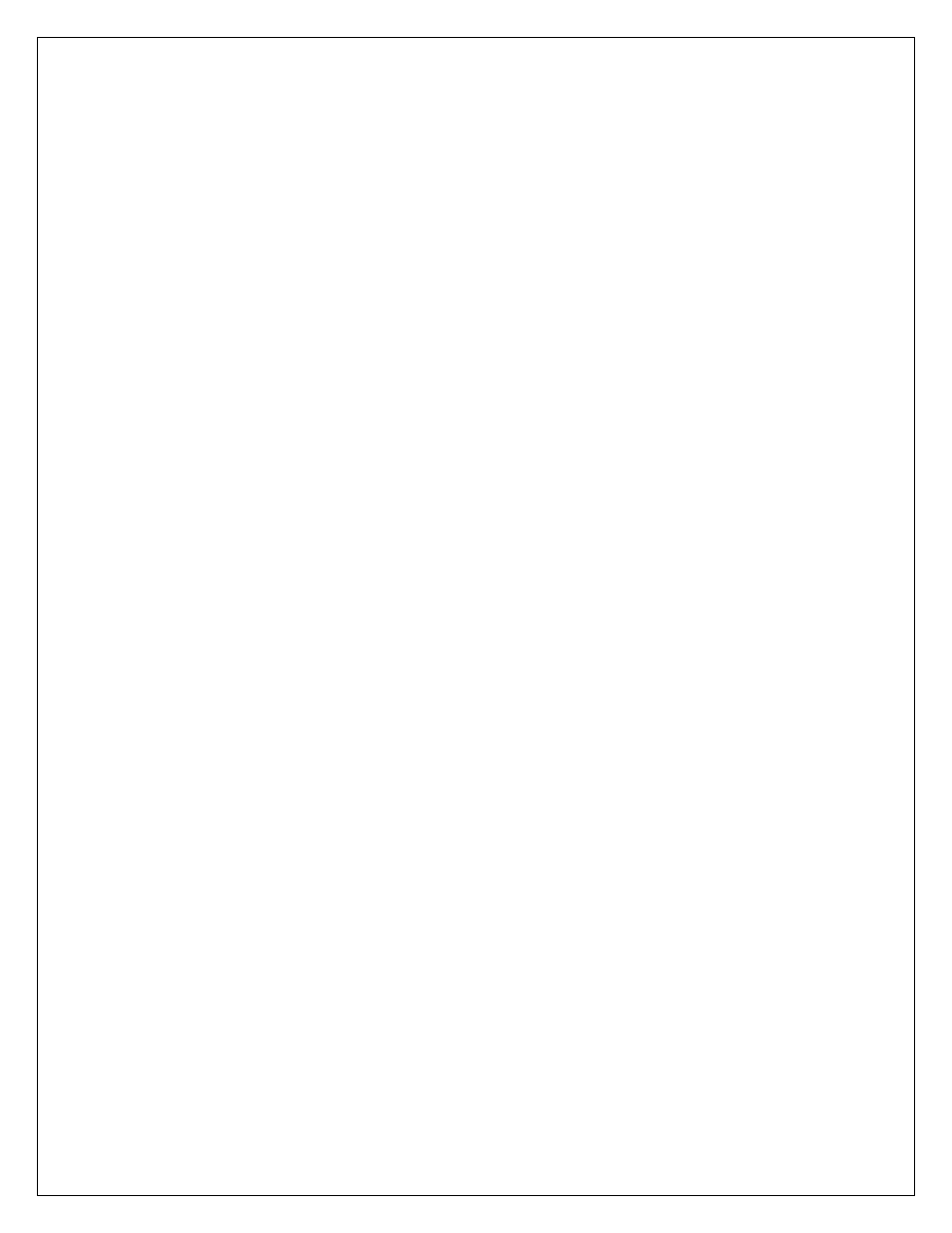
Page 177 of 279 EMS-4 Install and Tuning Guide_Rev 1.6
of the throttle is consistent with the need for high-power AFR during acceleration, it is equivalent
to the value needed for full power.
The amount of enrichment required is largely dependent on the design of the inlet tract and
placement of the injectors. Enrichment for systems where the injectors are placed far from the
inlet valves will have to be higher than if the injectors are placed near the inlet valves. This is
because when the injectors are far from the inlet valves, such as on throttle body systems, there
is considerable manifold wall wetting.
At low manifold pressures (commonly high manifold vacuum), fuel tends to stay in the air stream
in a vapor-like state and has relatively low wetting characteristics. The reason the wetting is
lower at high vacuum is because the pressure in the inlet manifold is closer to the vapor
pressure of the fuel, allowing the fuel to evaporate more readily (This is the same phenomenon
that makes water boil at a lower temperature at higher altitudes than at sea level).
As the throttle opens, manifold pressure increases (vacuum decreases), which increases the
pressure on the fuel vapor driving it to a more liquid state. This causes droplets of fuel to
deposit on the manifold walls and come out of the air stream. When the air speed in the inlet
manifold increases to a point where the liquid fuel on the manifold walls is reintroduced into the
air stream, there is no need for additional fueling and acceleration fuel is shut off.
With most modern road cars the injectors are placed near the inlet valves so that manifold wall
wetting is virtually eliminated. With the elimination of wetting comes the drastic reduction of
acceleration fuel requirement. This configuration of fuel injector needs short duration and a
small amount of fuel for acceleration enrichment.
The prime input for acceleration data for the ECU is the throttle position sensor (TPS). The TPS
indicates the rate of change of the throttle plate to the ECU so that it can calculate the amount
of fuel in both volume (additional pulse width) and time (duration of additional pulse width). Very
rapid throttle movements usually require a short duration of a large amount of fuel, while slow
throttle changes use minimal amounts of additional fuel over a longer period.
When the throttle is closed rapidly the need for fuel is reduced sharply. Under deceleration
manifold pressure is very low (high vacuum). Any fuel that was on the manifold walls, port
walls, or valve head is re-introduced into the air stream due to the rapid decrease in manifold
pressure resulting in a temporarily rich mixture. The main fuel MAP values are usually very low
when experiencing low manifold pressure, so minimal fuel is being injected into the engine.
However, the mixture will still be rich due to the re vaporization of the wetted fuel.
The AEM EMS can be programmed to turn off or nearly turn off the fuel injectors during periods
of deceleration. This eliminates after burning in the exhaust manifold, and reduces hydrocarbon
emissions. There is a range of RPM and manifold pressure that must be defined by the
programmer to turn off the fuel. The RPM defined usually has a lower limit of idle speed plus
300 RPM. The manifold pressure is usually idle pressure minus 15 kpa. There is the possibility
that a load value of idle
– 15 kpa can be achieved during sustained running, but the throttle
angle decrease must be sensed by the ECU to activate deceleration fuel cut.