E. determine the flyback nominal timing t1 and t2, An368 – Cirrus Logic AN368 User Manual
Page 15
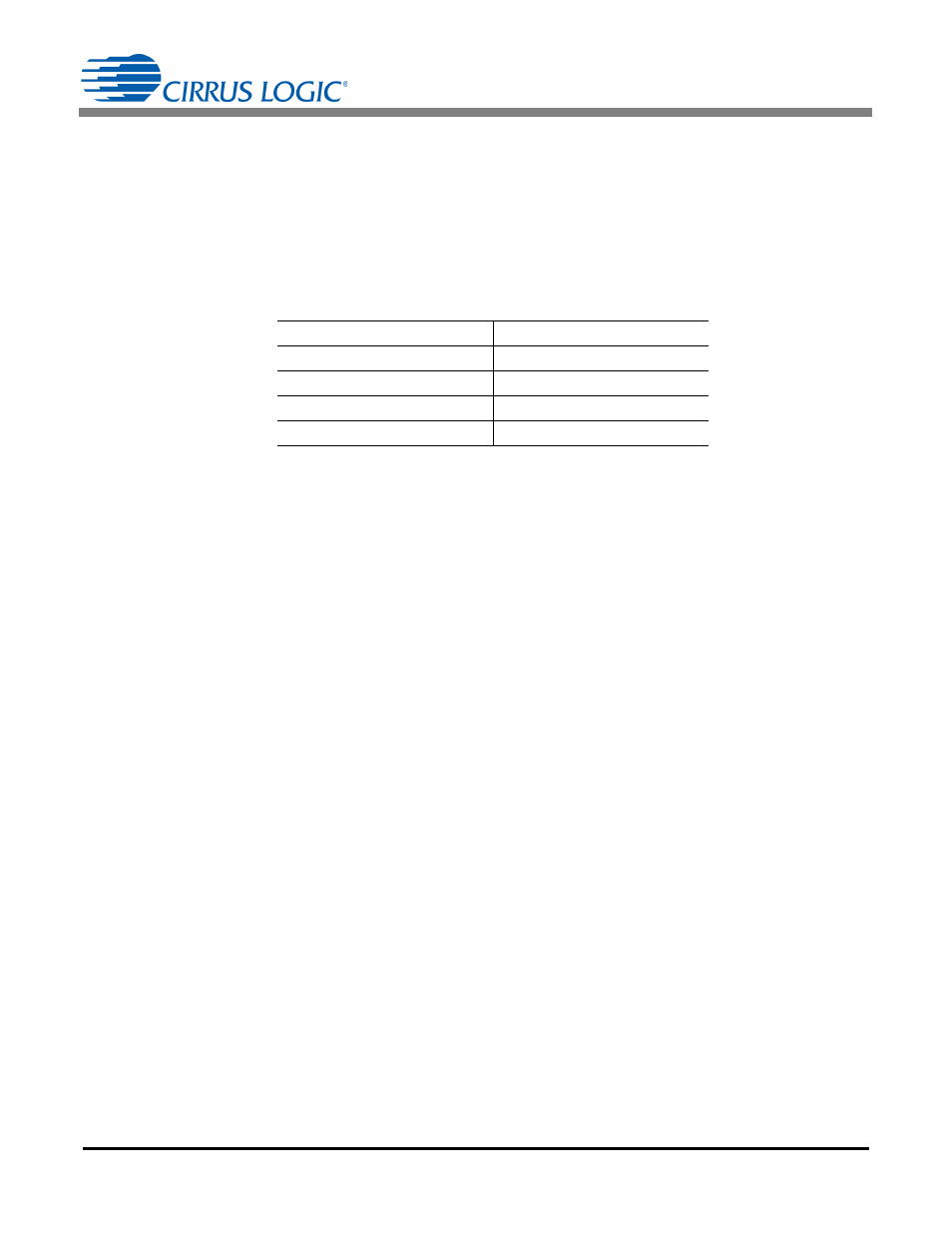
AN368
AN368REV2
15
The minimum switching frequency F
sw(min)
for the second stage is configured to provide good power
regulation. The minimum switching frequency should be set to the smallest possible value, but it should remain
outside of the audible frequency range. F
sw(min)
is configured using register TTMAX at Address 38. Bits
TTMAX[7:0] set the maximum allowable target period for the second-stage time TT:
The maximum second-stage switching period that is measured by the controller algorithm is set using bits
TT_MAX[1:0] in register Config3 at Address 35.
There are two modes of operation, and the output configuration in each of these modes is different.
Mode 1: Switching Event TT
CH1
In Mode 1 the phase synchronizer FET Q3 is switched ‘OFF’. Output voltage V
MODE1
and output current
I
MODE1
are calculated using Equations 7 and 8, respectively:
where,
V
CH1
= Channel 1 secondary output VDC (channel 1 LED string supply voltage)
V
CH2
= Channel 2 secondary output VDC (channel 2 LED string supply voltage)
V
D15
= Forward bias voltage across diode D15
V
D5
= Forward bias voltage across diode D5
I
CH2
= Channel 2 LED current
Mode 2: Switching Event TT
CH2
In Mode 2, phase synchronizer MOSFET Q3 is switched ‘ON’. Output voltage V
MODE2
and output current
I
MODE2
are calculated using Equations 9 and 10, respectively:
where,
I
CH1
= Channel 1 LED current
e. Determine the Flyback Nominal Timing T1 and T2
Assume that the power transferred in Mode 1 is greater than the power transferred in Mode 2. Select a Mode 1
switching frequency F
sw1
for optimal driver performance using the criteria described above.
TT_MAX[1:0]
Max Switching Period
0
51.15
s
1
102.35
s
2
153.55
s
3
204.75
s
Table 1. Maximum Measurable Switching Period
1
F
sw min
--------------------
TTMAX[7:0] 128 127
+
50ns
=
[Eq. 6]
V
MODE1
V
CH1
V
CH2
V
D15
V
D5
+
+
+
=
[Eq. 7]
I
MODE1
I
CH2
=
[Eq. 8]
V
MODE2
V
CH1
V
D15
+
=
[Eq. 9]
I
MODE2
I
CH1
I
CH2
–
=
[Eq. 10]