Troubleshooting chart – Pulsafeeder Pulsar Shadow User Manual
Page 36
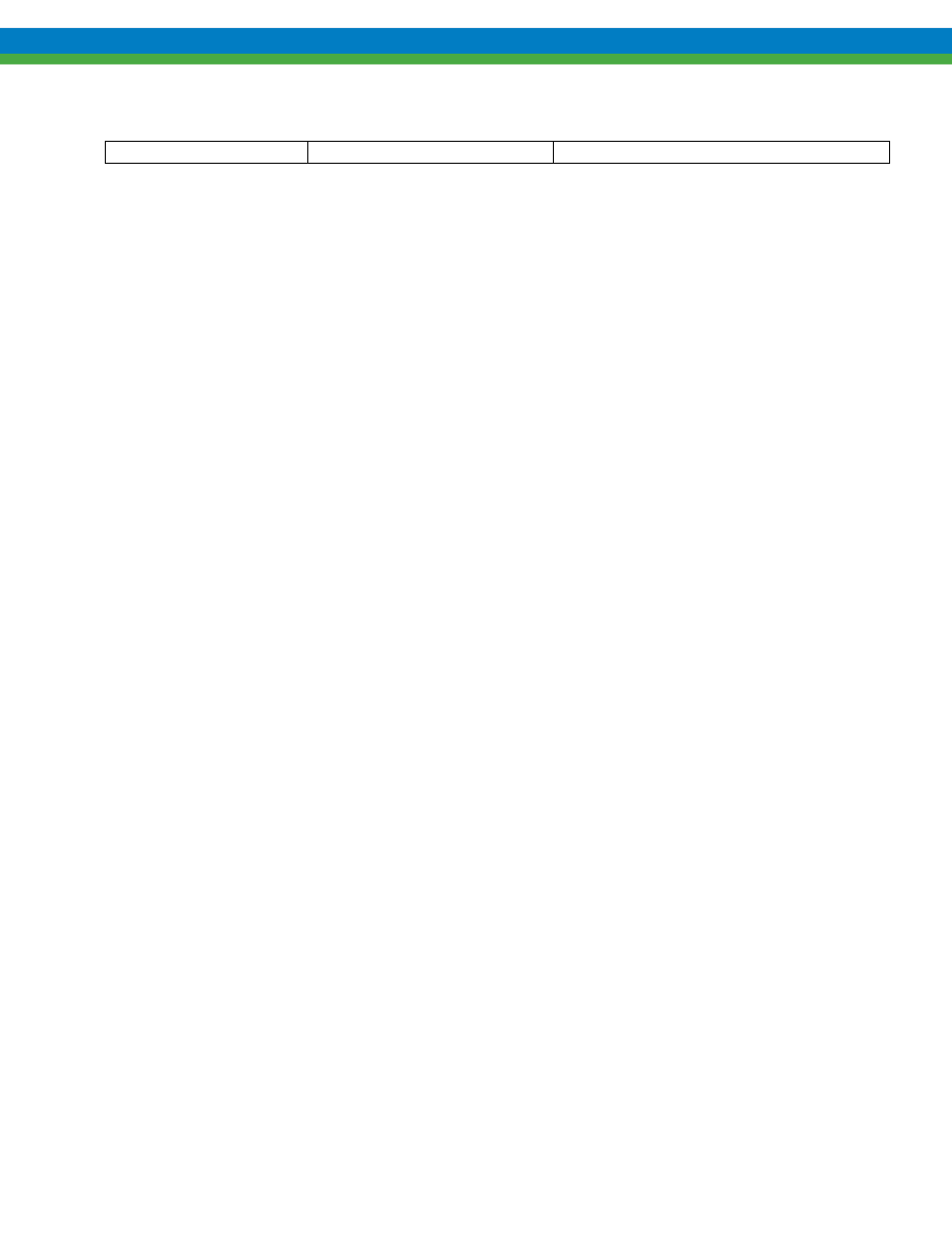
30
10. Troubleshooting Chart
Difficulty
Probable Cause
Remedy
Pump does not start.
1. Coupling disconnected.
Connect coupling.
2. Faulty power source.
Check power source.
3. Blown fuse, and circuit breaker.
Replace - eliminate overload.
4. Broken wire.
Locate and repair.
5. Wired improperly.
Check diagram.
6. Pipe line blockage.
Open valves.
No delivery.
1. Motor not running.
Check power source. Check wiring diagram.
2. Supply tank empty.
Fill tank.
3. Lines clogged.
Clean and flush.
4. Closed line valves.
Open valves.
5. Ball check valves held open with
solids.
Clean and inspect.
6. Vapor lock, cavitation.
Increase suction pressure.
7. Prime lost.
Reprime, and check for leak.
8. Strainer clogged.
Remove and clean. Replace screen if necessary.
9. Hydraulic system under-primed.
Refer to Repriming the Pump.
Low delivery.
1. Motor speed too low.
Check voltages, frequency, wiring, and Terminal
connections. Check nameplate vs. Specifications.
2. Check valves worn or dirty.
Clean, replace if damaged.
3. Hydraulic bypass valve operating
each stroke.
Refer to Hydraulic Bypass Valve.
4. Calibration system error.
Evaluate and correct.
5. Product viscosity too high.
Lower viscosity by increasing product
temperature. Increase pump and/or piping size.
6. Product cavitating.
Increase suction pressure. Cool product as
necessary.
7. Piston seal worn or damaged by
contamination.
Inspect and replace if necessary, refer to Piston
Seal.
8. Process pressure relief valve
leaking or relieving
Repair, adjust or replace
Delivery gradually drops. 1. Check valve leakage.
Clean, replace if damaged.
2. Leak in suction line.
Locate and correct.
3. Strainer fouled.
Clean or replace screen.
4. Product change.
Check viscosity.
5. Bypass leakage.
Correct for bypass valve leakage.
6. Piston seal worn or damaged by
contamination.
Inspect and replace if necessary, refer to Piston
Seal.
7. Supply tank vent plugged.
Unplug vent.
Delivery erratic.
1. Leak in suction line.
Locate and correct.
2. Product cavitating.
Increase suction pressure.
3. Entrapped air or gas in product.
Consult factory for suggested venting.
4. Motor speed erratic.
Check voltage and frequency.
5. Fouled check valves.
Clean, replace if necessary.
Delivery higher than
rated.
1. Suction pressure higher than
discharge pressure.
Install backpressure valve or consult factory for
piping recommendations.
2. Back pressure valve set too low.
Increase setting.
3. Back pressure valve leaks.
Repair, clean, or replace.
4. Calibration error
Review calculations