Check valves, General description, Removal, inspection, and reinstallation – Pulsafeeder Pulsar Shadow User Manual
Page 26: 3 check valves
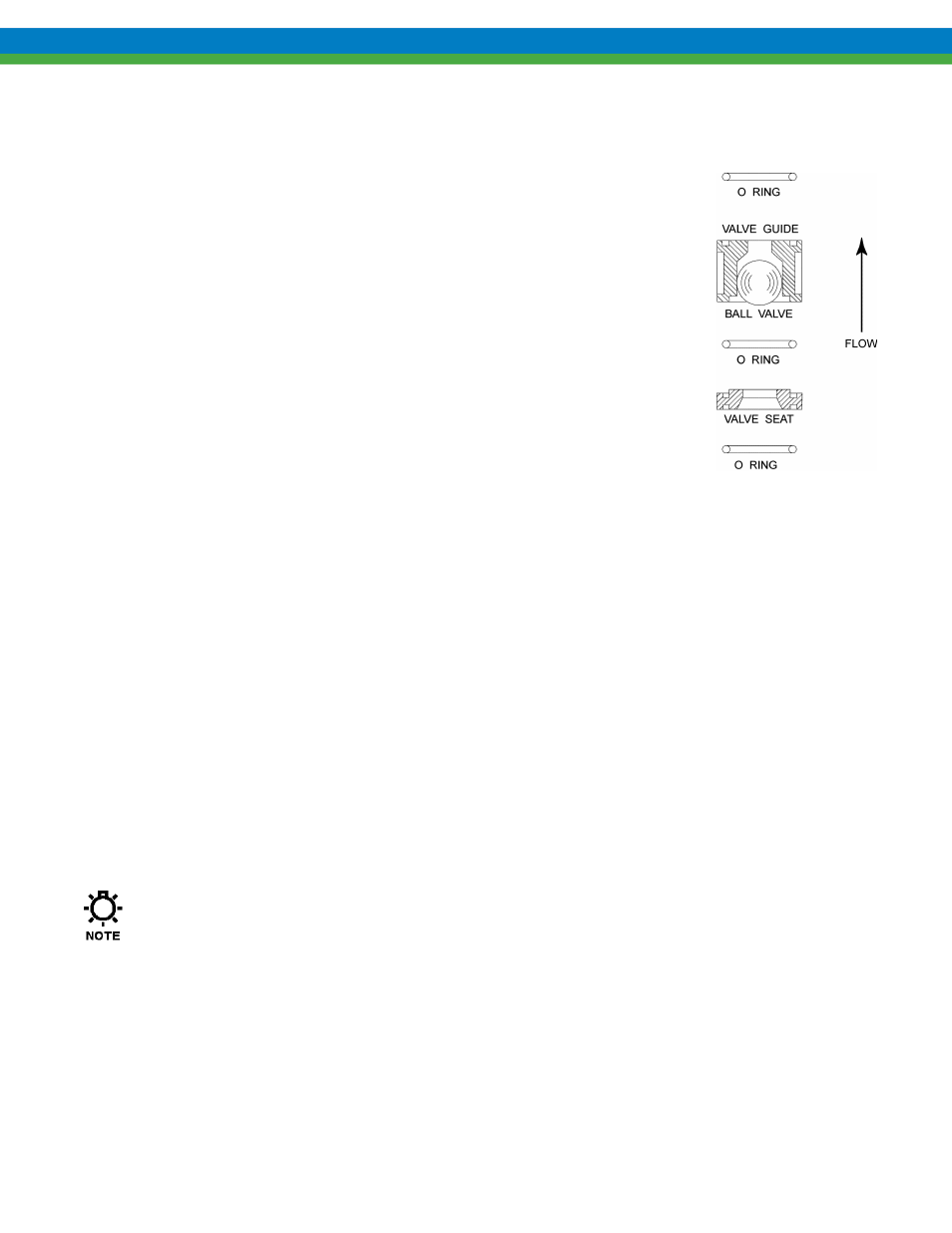
20
7.3
Check Valves
7.3.1
General Description
Most fluid metering problems are related to check valves. Problems usually
stem from solids accumulation between valve and seat, corrosion of seating
surfaces, erosion, or physical damage due to wear or the presence of foreign
objects.
The valve incorporates a ball, guide, and seat. Flow in the unchecked
direction lifts the ball off the seat, allowing liquid to pass through the guide.
Reverse flow forces the ball down, sealing it against the sharp edge of the
seat. The guide permits the ball to rotate but restricts vertical and lateral
movement in order to minimize “slip” or reverse flow. Ball rotation prolongs
life by distributing wear over the entire surface of the ball. Since ball return
is by gravity, the valve must be in the vertical position in order to function
properly. Parts are sealed by o-rings.
7.3.2
Removal, Inspection, and Reinstallation
Use the following procedure to remove, inspect and reinstall the check valves:
1. Disconnect the power source to the drive motor.
2. Relieve all pressure from the piping system.
3. Take all precautions to prevent environmental and personnel exposure to hazardous materials.
4. Close the inlet and outlet shutoff valves.
5. Loosen the suction valve tiebar bolts and spring the suction piping slightly to drain any liquid from
the reagent head cavity. If the piping is closely connected it may be necessary to disconnect a union
or flange.
6. Remove the suction check valve assembly (ball contained within guide and seat), holding it together
as a unit.
7. Loosen the tiebar bolts on the discharge valve and spring the piping slightly to drain any liquid.
8. Remove the discharge check valve assembly, holding it together as a unit as before.
9. Disassemble both valves and examine components for wear. Seats should have sharp edges or a
small chamfer, free from dents or nicks. Hold the ball firmly against its mating seat in front of a
bright light to inspect for fit.
Observation of light between ball and seat is cause for replacement of either or both components.
For best results, always loosen the unions or flanges on either side of the system piping prior to re-
tightening of the check valve assemblies. Retighten the unions or flanges after the check valves are
securely tightened into position.
10. Reassemble both valves using new parts as required. Sealing o-rings should always be replaced.
11. Reinstall both valve assemblies, taking care to ensure that they are correctly oriented with balls above
seats.
12. Tighten the tiebar bolts evenly, making sure the valve assemblies are assembled squarely. Refer to
Appendix IV for torque values.
13. Check for leaks and retighten tiebar bolts as necessary.