1 configuration parameters 29, Configuration parameters 29 - 41, Cntr – West Control Solutions KS 92-1 Programmer manual User Manual
Page 29: 1 configuration parameters, Configuration level
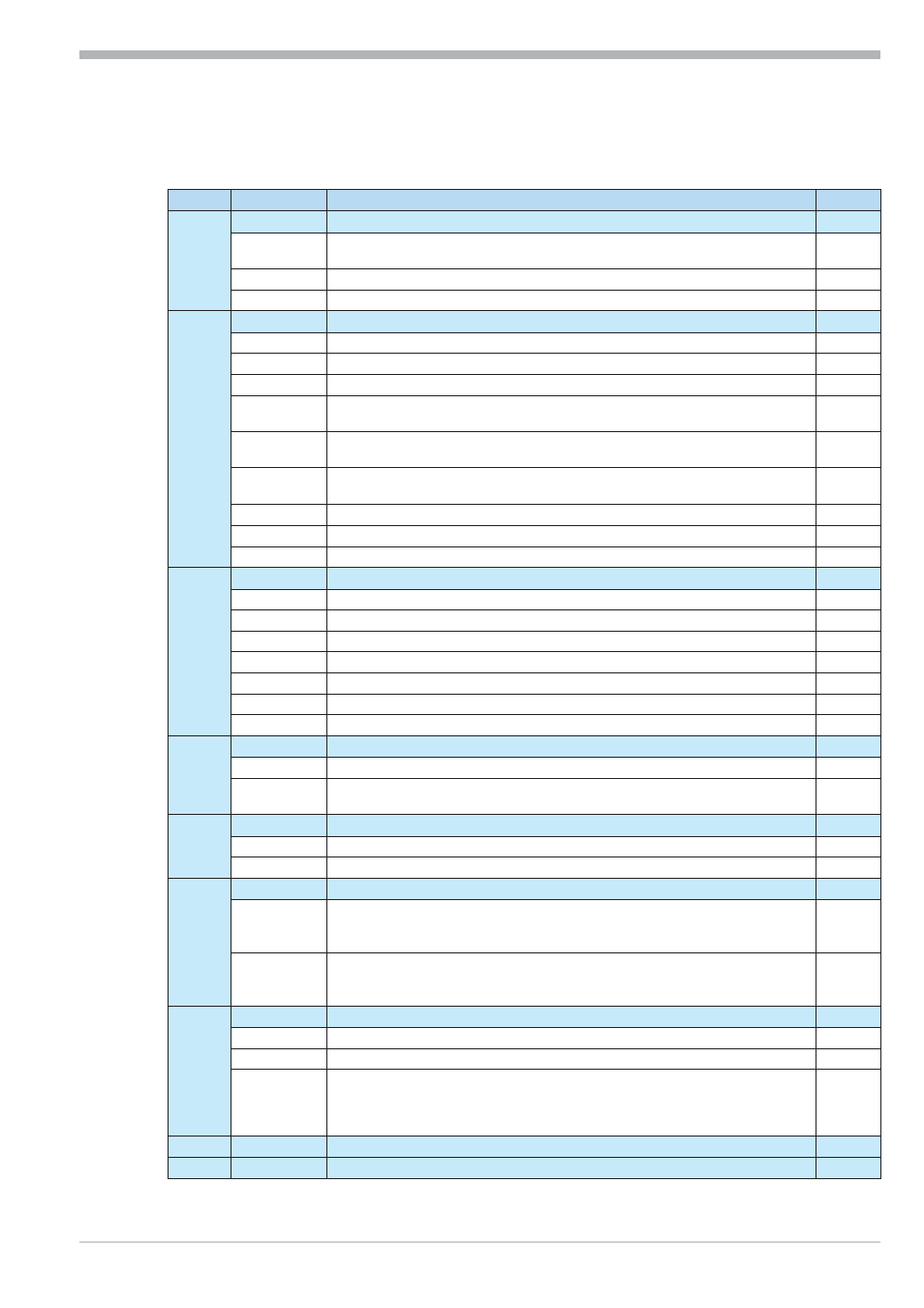
4.1 Configuration parameters
Configuration level
KS 90-1
p / KS 92-1
p
29
Configuration parameters
q
Cntr
Name
Value range Description
Default
SP.Fn
Basic configuration of setpoint processing
0
0
set-point controller can be switched over to external set-point
(->
LOGI/ SP.E)
8
standard controller with external offset (
SP.E)
9
Programmer with external offset (SP.E)
C.tYP
Calculation of the process value
0
0
standard controller (process value = x1)
1
ratio controller (x1/x2)
2
difference (x1 - x2)
3
Maximum value of x1and x2. It is controlled with the bigger value.
At sensor failure it is controlled with the remaining actual value.
4
Minimum value of x1and x2. It is controlled with the smaller value. At
sensor failure it is controlled with the remaining actual value.
5
Mean value (x1, x2). With sensor error, controlling is continued
with the remaining process value.
6
Switchover between x1 and x2 (->
LOGI/ I.ChG)
7
O
2
function with constant sensor temperature
8
O
2
function with measured sensor temperature
C.Fnc
Control behaviour (algorithm)
1
0
on/off controller or signaller with one output
1
PID controller (2-point and continuous)
2
D / Y / Off, or 2-point controller with partial/full load switch-over
3
2 x PID (3-point and continuous)
4
3-point stepping controller
5
3-point stepping controller with position feedback Yp
6
continuous controller with integrated positioner
C.dif
Output action of the PID controller derivative action
0
0
Derivative action acts only on the measured value.
1
Derivative action only acts on the control deviation
(set-point is also differentiated)
mAn
Manual operation permitted
0
0
no
1
yes (r
LOGI / mAn)
C.Act
Method of controller operation
0
0
inverse, e.g. heating
The correcting variable increases with decreasing process value and
decreases with increasing process value.
1
direct, e.g. cooling
The correcting variable increases with increasing process value and
decreases with decreasing process value.
FAIL
Behaviour at sensor break
1
0
controller outputs switched off
1
y = Y2
2
y = mean output. The maximum permissible output can be adjusted
with parameter
Ym.H. To prevent determination of inadmissible va-
lues, mean value formation is only if the control deviation is lower
than parameter
L.Ym.
rnG.L
-1999...9999
X0 (start of control range) 1
-100
rnG.H
-1999...9999
X100 (end of control range) 1
1200