Trouble shooting – Magnum Venus Plastech Flex Molding Process MKVI Mix User Manual
Page 65
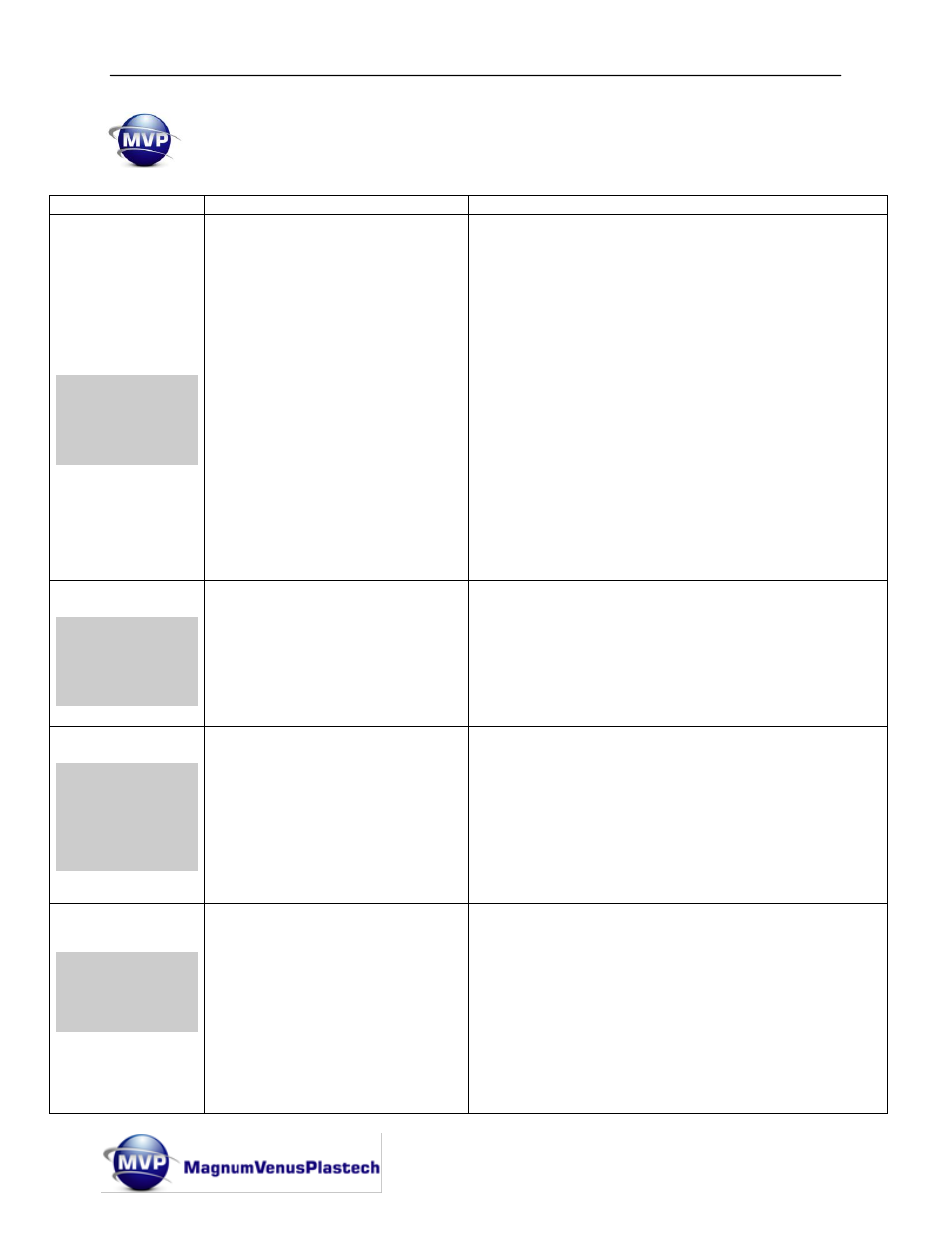
MKVI Mix Meter System Operations Manual
Rev. 08/2013
Page | 65
Trouble Shooting:
Symptom
Cause
Remedy
A:
PUMP DOES NOT
OPERATE ON
RECIRCULATION
COMMAND
1. NO AIR SUPPLY
2. SUPPLY SWITCH TRIPPED OFF
3. AIR SUPPLY - LOW PRESSURE
4. PUMP REGULATOR TOO LOW
5. CATALYST O/P VALVE
OPERATED
6. MPG SIGNAL READING LOW OR
ZERO
7. PUMP CHANGEOVER SWITCH
NOT BEING ACTIVATED
8. RESIN PUMP SEIZED WITH OLD
RESIN
Check pressurised air line connected to machine air inlet.
Check
‘pull on’ switch is down - pull down for ‘ON’
Check air supply is at least 5.0 bar on incoming pressure gauge
Increase pump speed regulator output pressure.
Check catalyst re-circulation valve is in re-circulation position.
Check red signal pipe and fitting on MPG at head is secure and is not
leaking. Also check MPG brass spool is not leaking air. Apply pressure
to brass spool and observe signal pressure increase on panel which may
indicate MPG diaphragm requires renewing. Service and renew internal
MPG ‘O’ ring seals if spool leaks air when machine is idle.
Check changeover switches are being activated correctly by pump
If resin is left in the machine fluid section for extended periods it may gel
prematurely or harden completely. Check for signs of this in tank, inlet
pipe or re-circ return pipe. A complete clean out and service will be
needed of the entire system if this condition arises.
B:
PUMPS DO NOT
START ON
INJECTION
COMMAND
1. HEAD VALVES NOT IN
INJECTION FLOW POSITION
2. AS ABOVE 1 - 8
3. PRE-DETERMINING COUNTER
NOT RESET TO ZERO
Check that both Auto Valves are opening correctly.
As above
Reset to zero on counter reset button.
C:
PUMP TRIES TO
PUMP BUT
STOPS OR
STALLS
IMMEDIATELY
1. CATALYST OVER PRESSURE
TRIGGERING
2. HEAD OR MIXER GELLED UP
3. BLOCKED RESIN FITTING AT
HEAD
4. RESIN GELLED IN PUMP/HOSES
Catalyst O/P valve triggers indicating catalyst blockage at head. Check
NRV8 and catalyst re-circulation valve for blockage.
Check mixer first. Renew mixer element if partially blocked. If major
blockage, renew element and service complete head internals.
Check RAV for blockages. This section of the resin flow system can
remain un-cleared when resin is changed or machine has been idle for
extended periods.
Dismantle and service all machine resin fluid section
D:
RESIN FAILS TO
PUMP ON BOTH
PUMP STROKES
WHEN RECYCLED
1. PICK-UP FILTER PARTIALLY
BLOCKED/DAMAGED/MISSING
2. PUMP INTERNAL BALL CHECK
VALVE(S) NOT SEATING
3. PUMP PISTON SEAL WORN
4. RESIN VISCOSITY TOO HIGH
Check pick-up filter and clean in acetone. Note. When using fillers, this
filter can become clogged very rapidly especially if filled resin is not
agitated and re-circulated regularly
If the resin pick-up filter becomes damaged and/or filled resin is left idle
in the machine for extended periods the pump valves may intermittently
fail to operate correctly. It may be possible to clear the fault by recycling
quickly for several minutes otherwise the pump must be serviced. When
checking the valves (point 2 above) inspect the pump piston seal and
renew if badly scored and worn.
Reduce speed of pump and/or reduce resin viscosity