Operating procedures, Recirculation, Recirculation with inline heaters – Magnum Venus Plastech Flex Molding Process MKVI Mix User Manual
Page 26
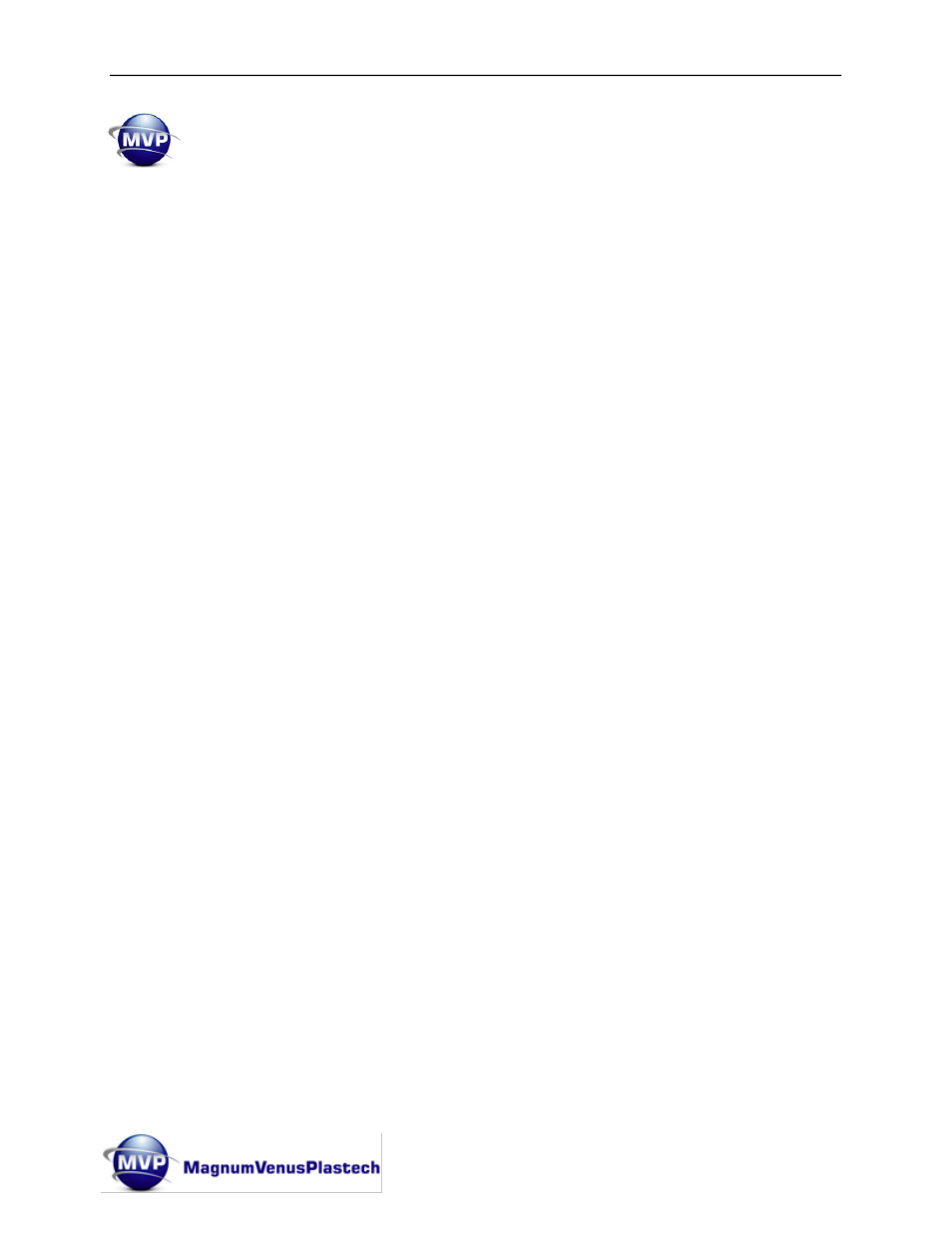
MKVI Mix Meter System Operations Manual
Rev. 08/2013
Page | 26
Operating Procedures:
Recirculation:
Recirculation of the machine should be carried out on a regular basis to ensure resin
and catalyst / hardener flows are even, free of air bubbles (observed through
recirculation returns) and to prevent sedimentation of any fillers/additives in the resin
system.
Recirculation should be carried out at the start of each shift or if new material has been
added to either the resin or catalyst containers.
1. Adjust pump pressure regulator until the pump pressure gauge reads approx. 2 bar.
If MPG is fitted, adjust MPG preset level to approx. 1 bar.
2. Push the
“Recirculation” button.
3. Allow machine to recirculate for required period. Ensure recirculating materials are
free of air bubbles and there is even flow on both pump strokes.
4. Press the
“Stop” button to turn “Off” the recirculation.
Recirculation with Inline Heaters:
1. If MPG is fitted, adjust MPG preset level to approx. 1 bar.
2.
Turn the main Electrical Power “On” – located on the side of control cabinet.
3.
Push the “Recirculation” button and slowly adjust the Pump pressure so that the
pump is moving slowly and even.
4.
Turn the Heat control to the “On” position and adjust the Controller to the desired
temperature.
5. Allow machine to recirculate for necessary period. Ensure recirculating materials are
free of air bubbles and at the desired temperature.
6.
Before shutting down turn the Heat control to the “Off” position and allow the machine
to recirculate for several minutes to remove any stored heat in the heater core.
7.
Press the “Stop” button to turn “Off” the recirculation.