Bell & Gossett S13641B Technologic 5500 Series Pump Controller User Manual
Page 8
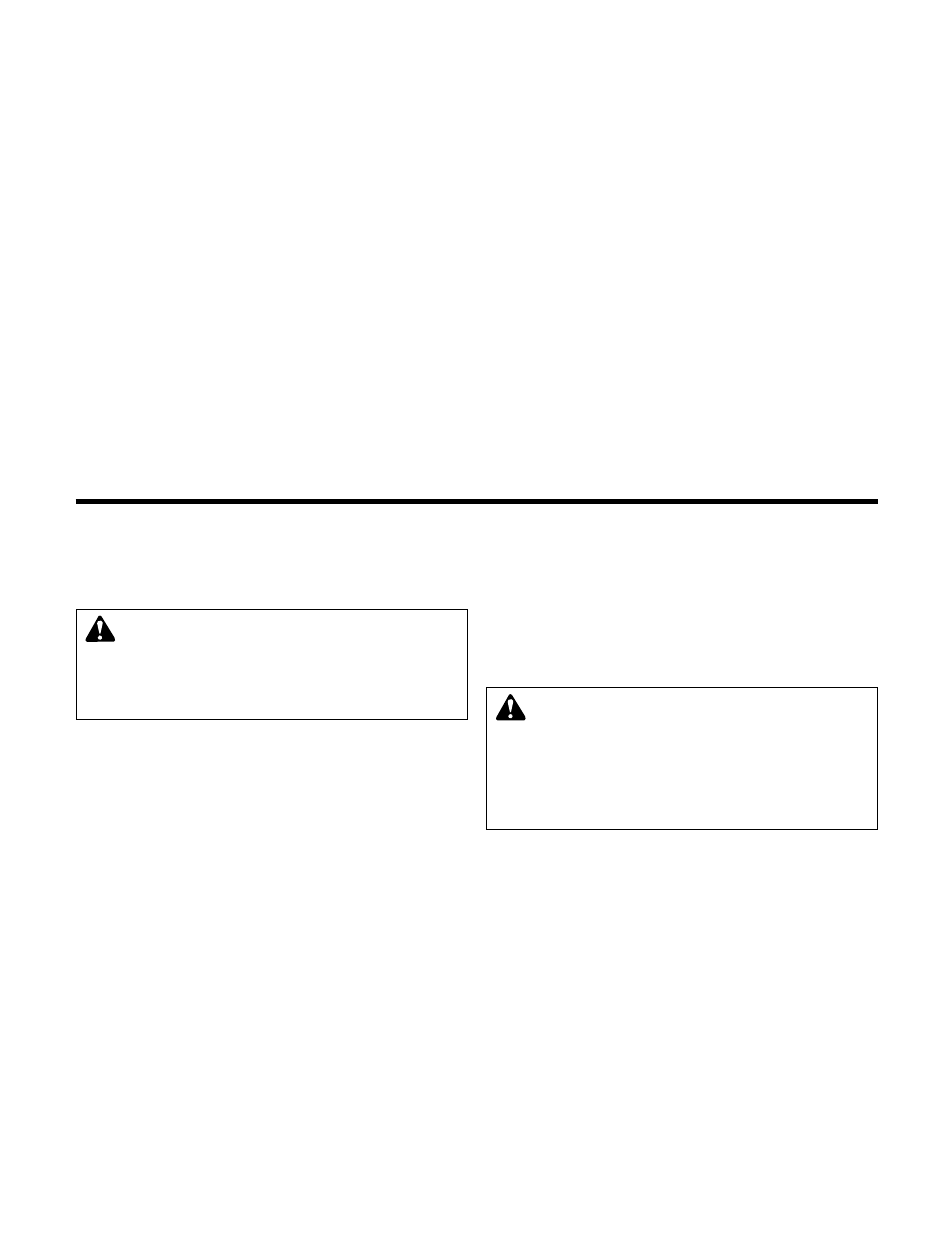
8
5) Terminate the negative (-) wire of the sensor to TB
41 of the respective analog input sensor con-
nection. Terminate the positive (+) wire of the
sensor to the terminal block which is connected to
the positive (+) terminal shown on the Analog input
card.
NOTE: Be certain that the power supplied to other
terminal blocks has not been interrupted since the
wires that have been removed in the proceeding
steps may have been used as jumpers.
1.12.9
Drive speed (follower) signals must be wired from the
Technologic 5500 Controller to each of the adjustable
frequency drives. The AFDs must be configured to
accept a 0-10 VDC speed signal with the minimum
speed set for 30% (0 VDC) and maximum speed set
for 100% (10 VDC). All shields must be grounded in
the Technologic 5500 only to prevent ground loops
and improper signals.
1.12.10 Hardwire communications refers to the capability of
the Technologic 5500 Controller to communicate with
an energy management system. Standard communi-
cation features are listed below:
1.12.11 Remote Start/Stop
Install a switch as indicated on the wiring diagram.
With the LOCAL-REMOTE-OFF switch in the
REMOTE position this contact closure will provide
the start signal.
1.12.12 Remote Alarm Indication
A digital output rated 8 AMPs at 115V is supplied.
This output closes to indicate an alarm condition
exists.
1.12.13 User Configurable I/O
The Technologic 5500 Controller comes equipped
with the capability to define the operation of any
unused input or output signal. Refer to Section 3.15
for detailed information on the I/O setup menus
2.0
LOCATION
2.1
Install the pumping unit appropriately for ease of
inspection, maintenance and service. Observe local
electrical codes concerning control panel spacing.
2.2
INSTALLATION OF SKID MOUNTED SYSTEMS
WITH FACTORY SUPPLIED PUMPS
This unit is built to give you years of service; install it
properly and provide a suitable foundation. A base of
concrete weighing 2-1/2 times the weight of the unit
is recommended. (Check the shipping ticket for unit
weight.) Tie the concrete pad in with the finished
floor. Use foundation bolts and larger pipe sleeves to
give room for final bolt location.
2.2.1
Place the unit on its concrete foundation, supporting
it with steel wedges or shims totaling 1” in thickness.
These wedges or shims should be put on both sides
of each anchor-bolt to provide a means of leveling
the base.
2.2.2
After the frame has been leveled and securely bolted
to the pad, a good grade of grout should be installed
beneath the base. A suggested mixture for grout is:
one part Portland Cement and two or three parts
plain, sharp sand mixed with water until it will pour
easily. Commercial grout mixtures with suspended
iron particles are available. Wet the concrete base
before pouring grout. To hold wedges or shims in
place, allow the grout to flow around them and
beneath the entire length of the base flange.
2.2.3
Important. Do not install and operate the Bell &
Gossett Technologic 5500 pump controller in a
closed system unless the system is constructed with
properly sized safety and control devices. Such
devices include the use of properly sized and located
pressure relief valves, compression tanks, pressure
controls, temperature controls and flow controls as
appropriate. If the system does not include these
devices, consult the responsible engineer or architect
before making pumps operational.
2.2.4
Eccentric increasers can be used in the suction lines
when increasing the pipe size, with straight sides of
increaser on top to eliminate air pockets. Be sure to
eliminate any pipe strain on the unit. Support the suc-
tion and discharge pipes independently by use of
pipe hangers near the unit. Line up the vertical and
horizontal piping so that the bolt holes of the flanges
match. DO NOT ATTEMPT TO SPRING THE SUC-
TION OR DISCHARGE LINES INTO POSITION.
2.2.5
As a rule, ordinary wire or band hangers are not ade-
quate to maintain alignment. It is very important to
provide a strong, rigid support for the suction line. A
saddle hanger is recommended.
2.2.6
For critical installations, equipment for absorbing
expansion and vibration should be installed in the
inlet and outlet connections of the unit.
2.2.7
Before starting, all pumps and motors should be
checked for proper lubrication.
Section 2 - Installation
DANGER: The heating of water and other fluids
causes volumetric expansion. The associated forces
may cause failure of system components and releases of
high temperature fluids. This will be prevented by installing
properly sized and located pressure relief valves and com-
pression tanks. FAILURE TO FOLLOW THESE INSTRUC-
TIONS COULD RESULT IN SERIOUS PROPERTY DAM-
AGE AND SERIOUS PERSONAL INJURY OR DEATH.
DANGER: Heavy load, may drop if not lifted properly.
Do not lift the entire unit by the motor eyebolts. Lift
the unit with slings placed under the unit base rails. FAIL-
URE TO FOLLOW THESE INSTRUCTIONS COULD
RESULT IN SERIOUS PERSONAL INJURY, DEATH,
AND/OR PROPERTY DAMAGE.