1 dc braking, 2 vdc max controller – Siemens MICROMASTER 411 User Manual
Page 133
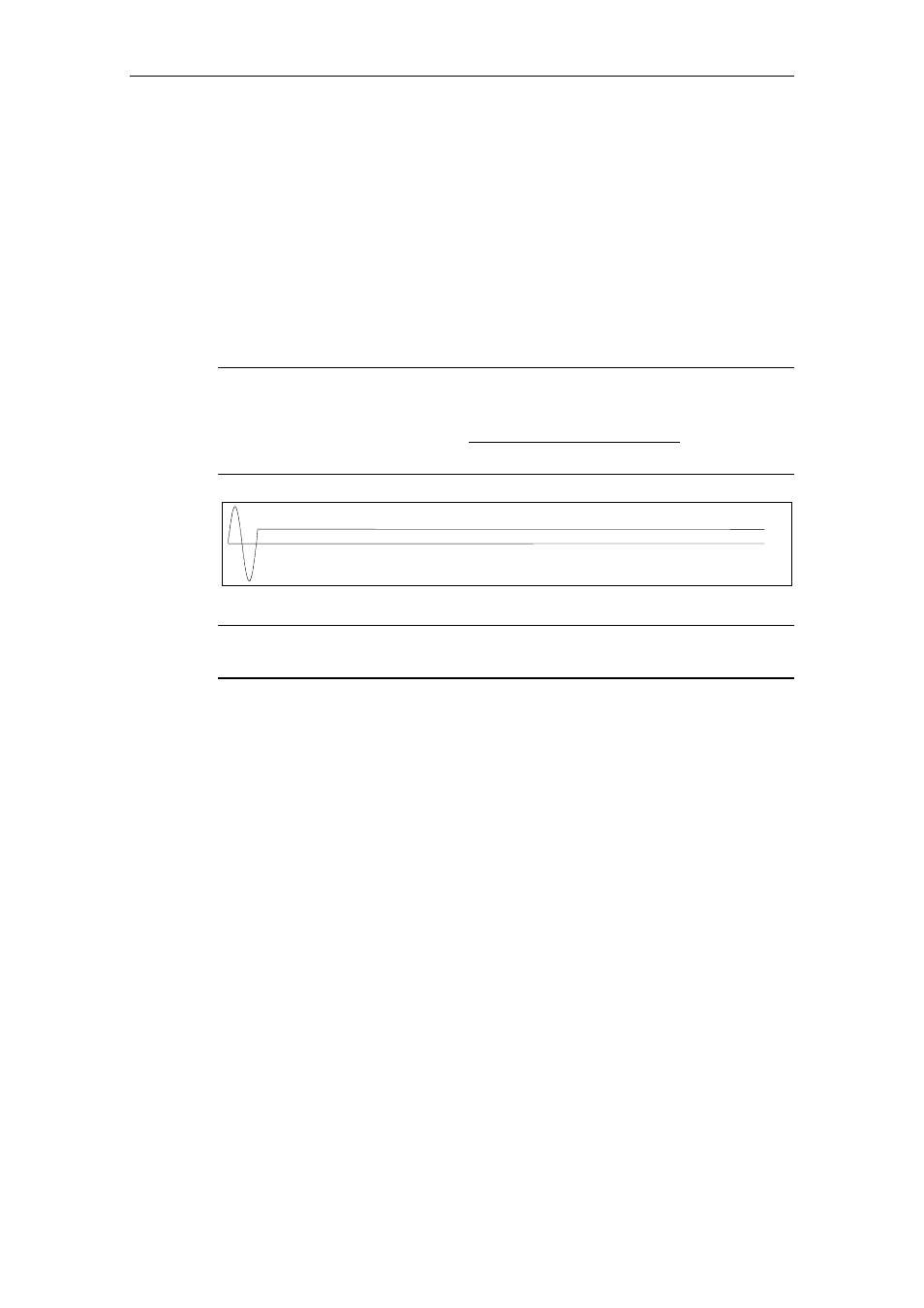
Issue 03/01
10 Engineering Information
MICROMASTER 411 & COMBIMASTER 411 Operating Instructions
6SE6400-5CA00-0BP0
133
10.3.1 DC
Braking
In this method a controlled DC voltage is applied to the rotor. When using DC
braking, the inverter output pulses are disabled and the actual time taken to bring
the motor to a standstill cannot be predicted. Stored energy in the motor and the
load is dissipated in the rotor therefore no regeneration occurs.
The DC braking current is defined as a percentage of nominal motor current using
parameter P1232. The current will be applied only when the motor is sufficiently
demagnetized. If the demagnetization time for the motor (P0347), is reduced too
much then the drive will trip on over current (F0001) when DC braking is activated.
DC braking can be enabled by an external source such as a digital input.
NOTE
The braking time depends on the rampdown time as follows.
Figure 10-14 DC Braking
NOTE
Frequent use of DC Braking can cause the motor to overheat.
10.3.2
Vdc Max Controller
The MICROMASTER 411/COMBIMASTER 411 has a controller to limit the DC
voltage (Vdc Max controller). When braking a load faster than would normally be
possible, excess energy has to be dissipated. This energy is unable to go back into
the input supply so the result is that the DC link voltage rises. If this voltage rises
too high, the trip level will be reached and the output pulses disabled to prevent
damage to the inverter. The Vdc Max controller automatically increases the
frequency and extends the ramp down period so that the braking is not as fast,
thus reducing the risk of an overvoltage trip and keeping the system running. This
means that the system will ramp down on the voltage limit until a standstill or a new
setpoint is reached. (Refer to Parameter P1240 for configuration details).
Braking time = Rampdown-time *
P0305 (Motor rated current)
r0207 (Inverter rated current)