3 braking – Siemens MICROMASTER 411 User Manual
Page 132
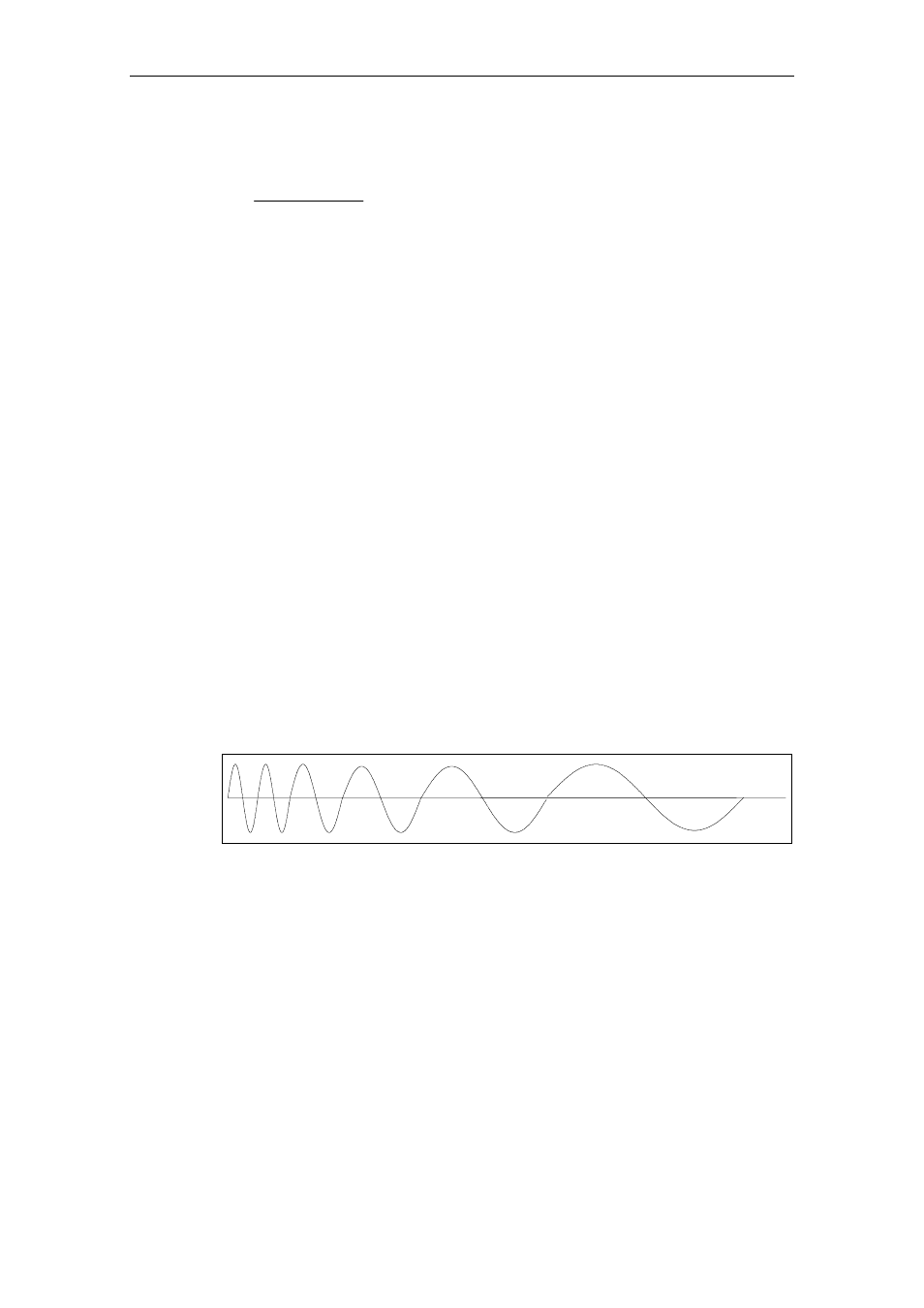
10 Engineering Information
Issue 03/01
MICROMASTER 411 & COMBIMASTER 411 Operating Instructions
132
6SE6400-5CA00-0BP0
If the active current falls below the normalized threshold P2395, then the setpoint is
linearly decreased as a function of the active current.
P2396
P2395
1
m
−
=
This reduction causes the motor to be powered-down and in turn the system (e.g.
pump), as long as the actual value (e.g. actual pressure) does not fall below the
threshold px.
If the actual value falls below threshold px, while the setpoint is decreased via the
active current, the decrease is stopped and the original setpoint p* is again re-
established.
If the actual value falls below threshold px after the motor was shutdown, the
inverter automatically powers-up again without having to toggle the ON command.
10.3 Braking
Reducing the output frequency of the inverter will cause the motor to slow down
and as the frequency is gradually reduced to zero the motor will stop. Reducing the
output frequency too rapidly may cause the motor to act as a generator and cause
a negative current (regeneration) to return to the DC link. To overcome this
possibility the MICROMASTER 411/COMBIMASTER 411 employs a number of
methods to control braking. These options are described in the following
paragraphs.
The method of bringing the motor to a standstill is selected by the user depending
on operational requirements.
Normal Braking
The usual or normal braking method is to allow the motor to come to a standstill at
the selected ramp-down rate (OFF1), to coast to a standstill (OFF2) or to quickly
ramp down (OFF3) without applying any additional braking. (Refer to parameters
P0701, P0702 and P0703). However, if regeneration does cause tripping, DC or
Compound braking methods may be considered.
Figure 10-13 Frequency Ramp Down