Dynamic operation, Full microprocessor based process control, Flexible programming – Parr Instrument 6100 User Manual
Page 9: Concept of operation
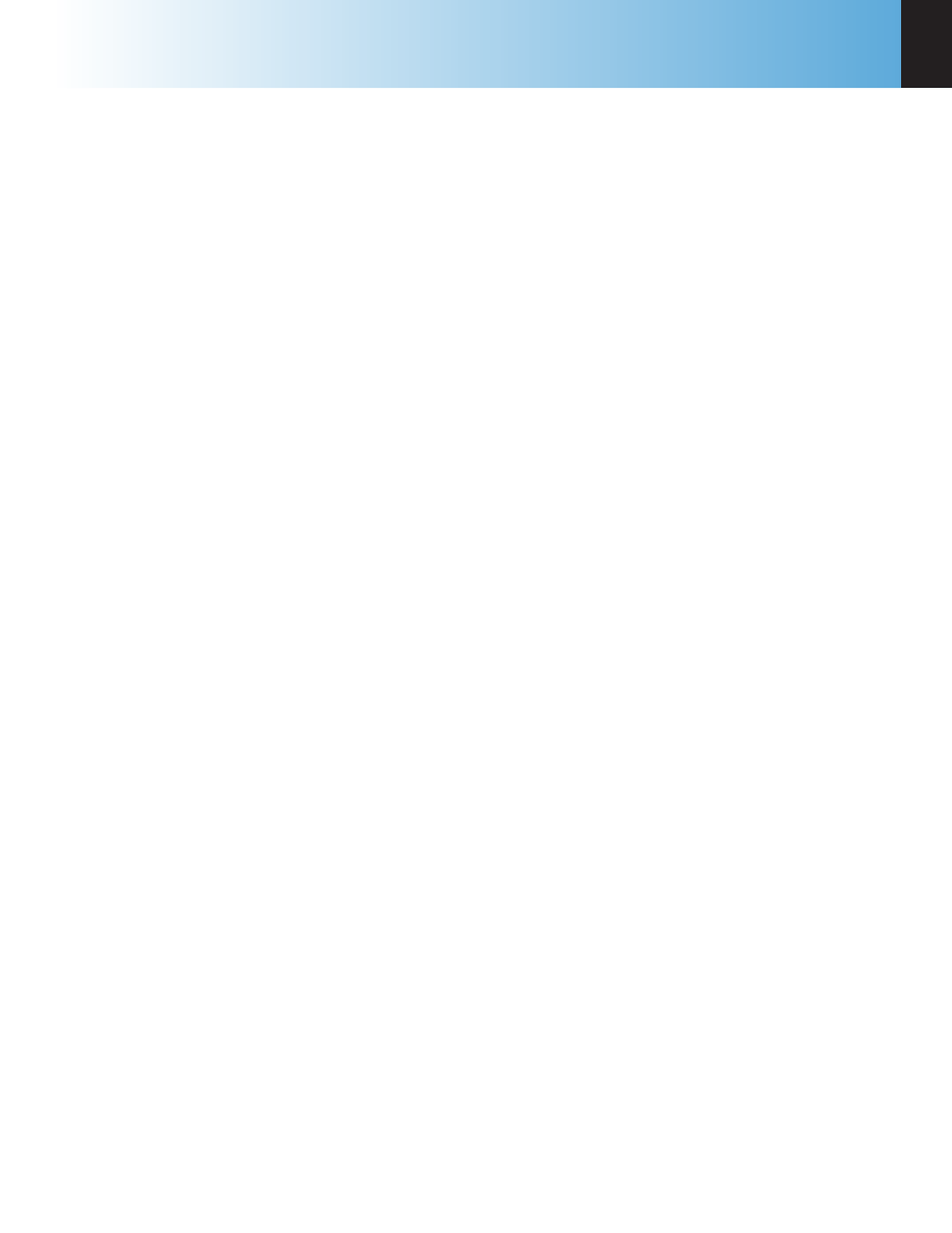
Concept of Operation
6100
1
w w w . p a r r i n s t . c o m
7
an automatic rolling average calculation to support
calibration maintenance and verification. Following
the aforementioned guidelines and using reference
samples, such as benzoic acid, the process sigma
(precision classification) of the 6100 Calorimeter can
be taken as 0.1%.
Dynamic Operation
In its Dynamic Operating Mode, the calorimeter uses
a sophisticated curve matching technique to compare
the temperature rise with a known thermal curve to
extrapolate the final temperature rise without actu-
ally waiting for it to develop. Repeated testing, and
over 20 years of routine use in fuel laboratories, has
demonstrated that this technique can significantly
cut the time required for a test by one-half without
significantly affecting the precision of the calorimeter.
Full Microprocessor Based Process Control
The microprocessor controller in this calorimeter has
been pre programmed to automatically prompt the
user for all required data and control input and to:
• Generate all temperature readings in the calorim-
eter.
• Monitor jacket as well as bucket temperature.
• Confirm equilibrium conditions.
• Fire the bomb.
• Confirm that ignition has occurred.
• Determine and apply all necessary heat leak cor-
rections.
• Perform all curve matching and extrapolations
required for dynamic operation.
• Terminate the test when it is complete.
• Monitor the conditions within the calorimeter and
report to the user whenever a sensor or operating
condition is out of normal ranges.
Full Microprocessor Based Data Acquisition
and Handling
In addition to its process control functions, the mi-
croprocessor in the calorimeter has been pre pro-
grammed to:
• Collect and store all required test data.
• Apply all required corrections for combustion
characteristics.
• Compute and report the heat of combustion for
the sample.
Flexible Programming
The fifth generation software built into this calorim-
eter and accessed through the screen menus permit
the user to customize the operation of the calorimeter
to meet a wide variety of operating conditions includ-
ing:
• A large selection of printing options.
• Choice of accessories and Peripheral equipment.
• Multiple options in regard to handling
thermochemical corrections.
• Choice of ASTM or ISO Correction procedures.
• A variety of memory management and reporting
procedures.
• Complete freedom for reagent concentrations and
calculations.
• Unlimited choice of reporting units.
• Automatic bomb usage monitoring and reporting.
• A choice of Equilibrium or Dynamic test methods.
• Automatic statistical treatment of calibration runs.
• Enhanced testing and trouble shooting procedure.
The 6100 Calorimeter is equipped with a universal
serial bus (USB) connection for communication with
a printer, balance, or other device. If more than one
device is to be used at the same time a USB hub will
need to be used. It is also equipped with an Ethernet
network connection for connections to laboratory
computers.