Chapter 1, Concept of operation, Overview – Parr Instrument 6100 User Manual
Page 8: Compensated jacket operation, Hapter
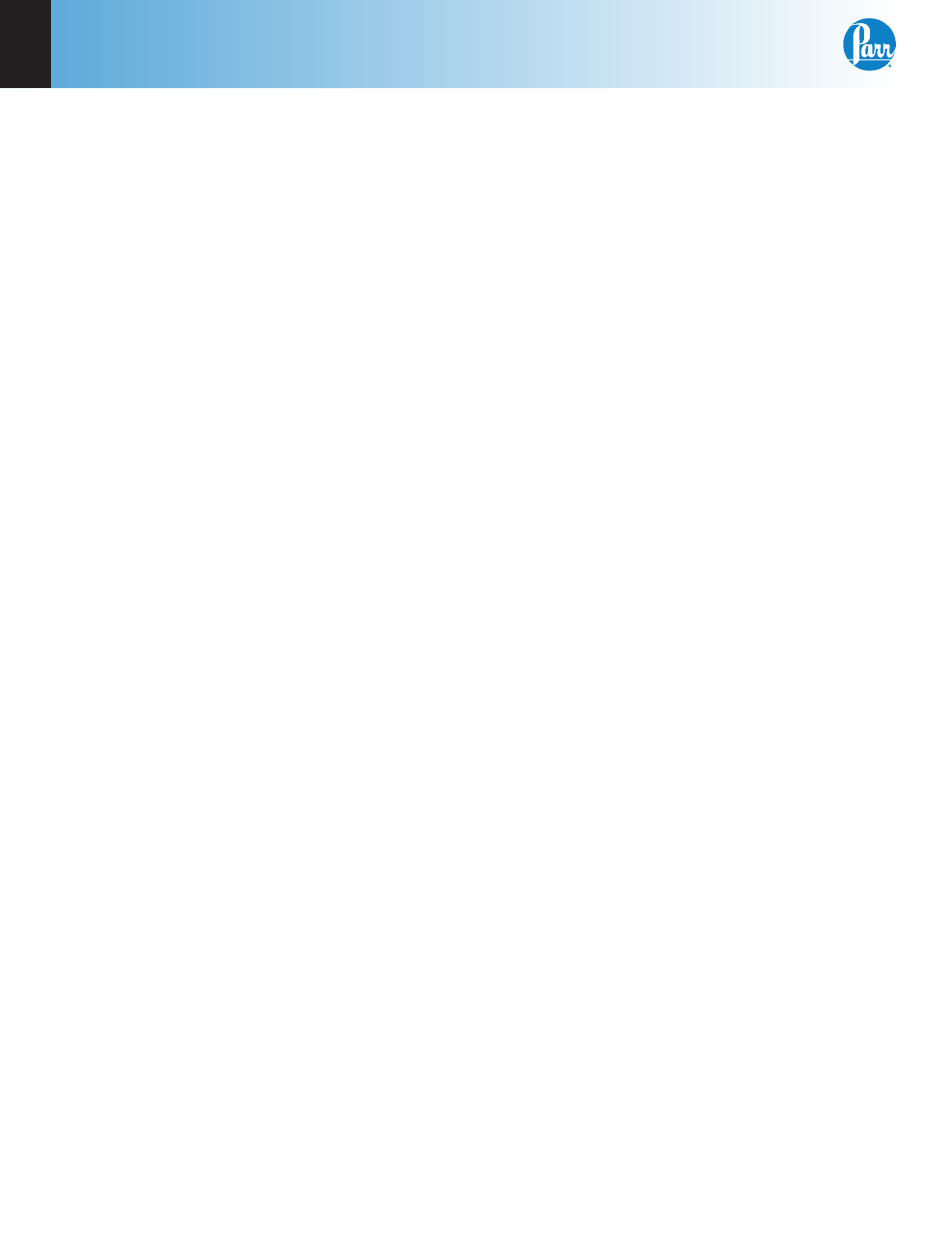
1
Concept of Operation
P a r r I n s t r u m e n t C o m p a n y
6
c
haPter
1
Concept of Operation
Overview
The 6100 Calorimeter has been designed to provide
the user with:
• A traditional design calorimeter with removable
oxygen bomb and bucket.
• A moderately priced calorimeter which uses real
time temperature measurements to determine
heat leaks without using a controlled calorimeter
jacket.
• A full featured calorimeter that does not require
circulating water.
• A compact calorimeter requiring minimum
laboratory bench space.
• A modern intuitive graphical user interface for
ease of operation and training.
• A calorimeter with up to date digital hardware,
software and communications capabilities.
• A calorimeter that is cost effective and which can
incorporate a user’s current bombs, buckets, and
accessories.
Removable Bomb
The Model 6100 Calorimeter utilizes the Parr 1108P
Oxygen Combustion Vessel. More than 20,000 of the
1108 style oxygen combustion vessels have been
placed in service on a world wide basis. This bomb
features an automatic inlet check valve and an adjust-
able needle valve for controlled release of residual
gasses following combustion. They are intended for
samples ranging from 0.6 to 1.2 grams with a maxi-
mum energy release of 8000 calories per charge.
The 1108P Oxygen Combustion Vessel is made of
high-strength, high nickel stainless steel designed
to resist the corrosive acids produced in routine fuel
testing. An alternative 1108PCL vessel is available,
constructed of an alloy containing additional cobalt
and molybdenum to resist the corrosive conditions
produced when burning samples containing chlori-
nated compounds.
The Model 6100 can also be equipped with a vari-
ety of special purpose oxygen bombs for unusual
samples and/or applications. The 1104 High Strength
Oxygen Combustion Vessel is designed for testing
explosives and other potentially hazardous materials.
The 1109A Semimicro Oxygen Combustion Vessel can
be fitted along with its unique bucket to test samples
ranging from 25 to 200 mg.
Removable Bucket
The A391DD removable bucket has been designed to
hold the bomb, stirrer and thermistor with a mini-
mum volume of water and to provide an effective
circulating system which will bring the calorimeter to
rapid thermal equilibrium both before and after firing.
Compensated Jacket Operation
The 6100 Calorimeter is intended for the user who
wants a calorimeter with the convenient automatic
features provided in a modern isoperibol calorimeter,
but whose precision requirements can be met with a
static system. To meet these criteria, the temperature
controlled water jacket and its accessories have
been removed from the 6200 Isoperibol Calorimeter
and replaced with an insulating jacket around the
bucket chamber. This eliminates all water and water
connections, resulting in a significant saving in cost.
To obtain the best precision with an uncontrolled
jacket, the 6100 Calorimeter has temperature moni-
toring capability built into the jacket. This allows the
calorimeter to measure the actual jacket temperature
and apply the appropriate heat leak corrections in
real time. While, not equal to a controlled jacket, the
6100 method offers a significant improvement over
the traditional static jacket and makes it possible to
obtain reasonable precision without the long pre-
and post-periods normally required for static jacket
calorimetry. It also makes it possible to use the Parr
Dynamic Method for rapid testing. As with all static
jacket calorimeters, best results are obtained when
the instrument is operated in a location where it is
not subject to air drafts and fluctuating tempera-
tures. The preferred operating environment is in a
temperature controlled room (+/- 1 C). It is a well
accepted principle of reliable analysis that any instru-
ment calibration be checked regularly. The optimum
frequency for checking the 6100 Calorimeter depends
largely on the temperature stability of the operating
environment. As general rule, the instrument calibra-
tion should be evaluated at least every tenth test. The
calorimeter controller software conveniently offers
both a graphical control chart approach in addition to