7 malfunctions and error correction, 1 general malfunctions, 1 power failure – Martin Christ Alpha 1-2 LDplus User Manual
Page 50: 2 insufficient vacuum
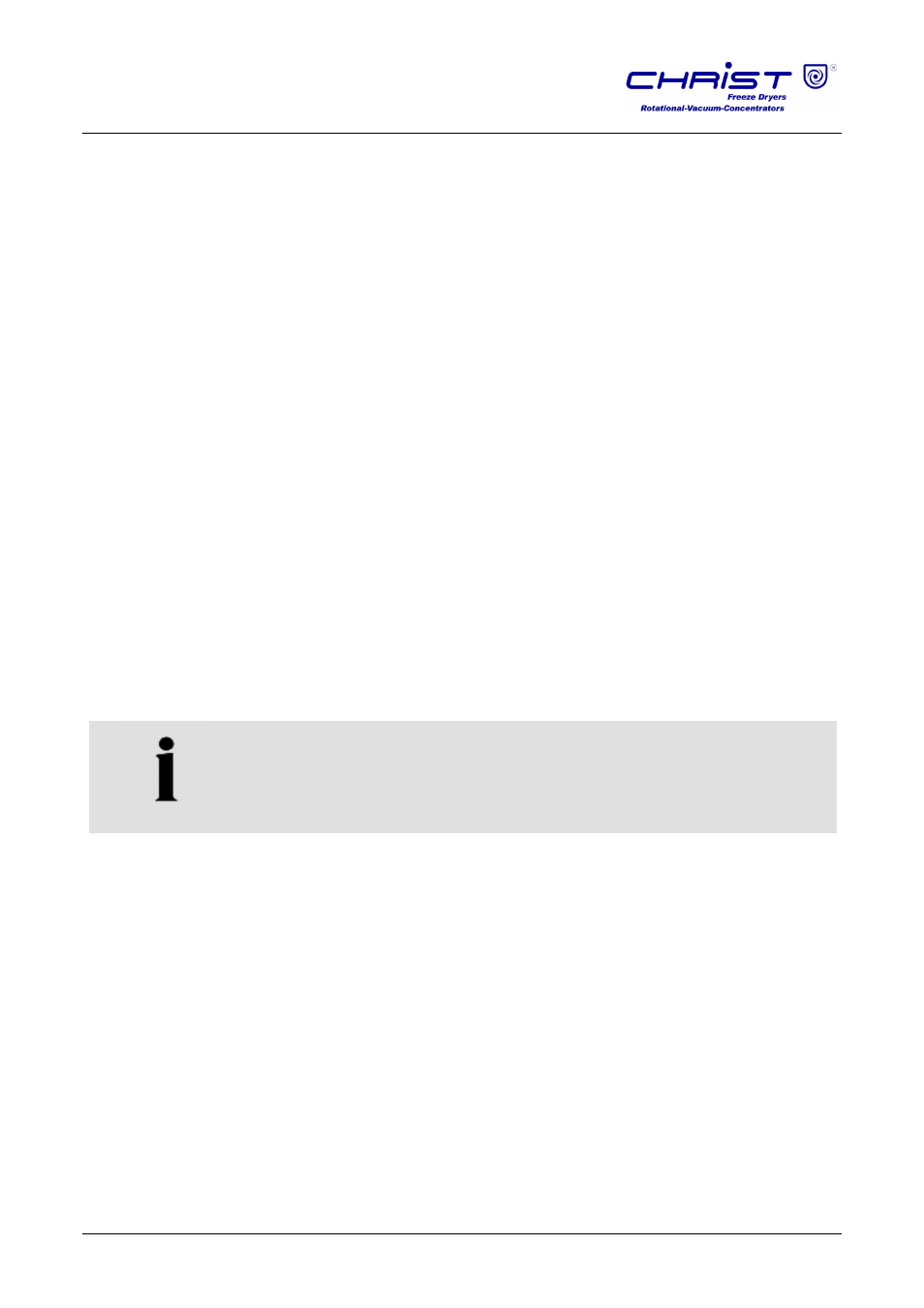
Freeze-dryer Alpha 1-2 LDplus
7 Malfunctions and error correction
50
Version 11/2006, Rev. 2.0 of 02/12/2014 • sb
Translation of the original operating manual
Pos: 139 /20 0 Ch rist/3 60 G T-BA L abo r-Pilot (STANDARDMODU LE)/0 70 Stö run gen und Fe hlers uche /07 0 Stö run gen und Fe hlers uche == == === == == === == == === == == == @ 25\ mo d_14 049 840 560 39_ 68.d ocx @ 184 111 @ 1 @ 1
7 Malfunctions and error correction
Malfunctions are displayed in the dialog box "Process & equipment
messages" (see chapter 6.5.3.3 - "Process and equipment information").
An acoustic signal sounds when an error message is generated.
• Eliminate the source of the problem (see the following chapter).
• Acknowledge the error message.
Pos: 140 /01 0 Univ ersal mod ule/L eerz eile @ 0\m od_ 120 211 624 450 0_0. docx @ 11 4 @ @ 1
Pos: 141 /20 0 Ch rist/3 60 G T-BA L abo r-Pilot (STANDARDMODU LE)/0 70 Stö run gen und Fe hlers uche /07 0-0 010 Allgem eine St öru nge n LDpl us @ 31\ mod _140 843 825 641 5_6 8.doc x @ 2 097 04 @ 2 @ 1
7.1 General malfunctions
Pos: 142 /20 0 Ch rist/3 60 G T-BA L abo r-Pilot (STANDARDMODU LE)/0 70 Stö run gen und Fe hlers uche /07 0-0 010 -00 10 N etzau sfall @ 25\ mod _14 049 840 5896 4_6 8.d ocx @ 1841 53 @ 3 @ 1
7.1.1 Power failure
The control system continues with the process after a power failure. The
preselected conditions remain saved even during a process run.
In the event of a power failure in the drying phase, the batch may become
unusable. Whether the batch can be saved or not depends on the drying
phase in which the product was when the power failure occurred.
• In the final drying phase, the product has reached a residual moisture
content of approx. 5%. Below this value, the product is generally not
damaged even if the power failure lasts for a longer period of time.
• If the product is in the main drying phase, we recommend aerating the
unit, removing the product, and storing it in a deep-freeze. The
defrosted condensate must be drained off prior to the next start.
Pos: 143 /01 0 Univ ersal mod ule/L eerz eile @ 0\m od_ 120 211 624 450 0_0. docx @ 11 4 @ @ 1
Pos: 144 /20 0 Ch rist/3 60 G T-BA L abo r-Pilot (STANDARDMODU LE)/0 70 Stö run gen und Fe hlers uche /07 0-0 010 -00 20 Kei n au sreic hend es Vak uum @ 2 5\mo d_1 404 984 060 039 _68. docx @ 18 416 7 @ 3 @ 1
7.1.2 Insufficient vacuum
NOTE
The vacuum checks must be carried out when the ice condenser is frozen.
Pos: 145 /01 0 Univ ersal mod ule/L eerz eile @ 0\m od_ 120 211 624 450 0_0. docx @ 11 4 @ @ 1
Pos: 146 /20 0 Ch rist/3 60 G T-BA L abo r-Pilot (STANDARDMODU LE)/0 70 Stö run gen und Fe hlers uche /07 0-0 010 -00 20- 0010 Kleinfl anschv er bindu nge n @ 25\m od_ 140 498 406 108 6_68 .docx @ 1 841 81 @ 4 @ 1
7.1.2.1 Small flange connections
Leakages are often due to improper small flange connections between the
various components and hose connections or to leakages in the valves.
• Loosen the connection and place the centring ring (with sealing ring
inside) in a centred manner between the flange connections.
• Seal the connection with the clamping ring by tightening the wing nut.
• Ensure that the centring ring neither slips out of place nor gets jammed.