Viking Pump TSM285: Classic+ Lobe Pump User Manual
Page 15
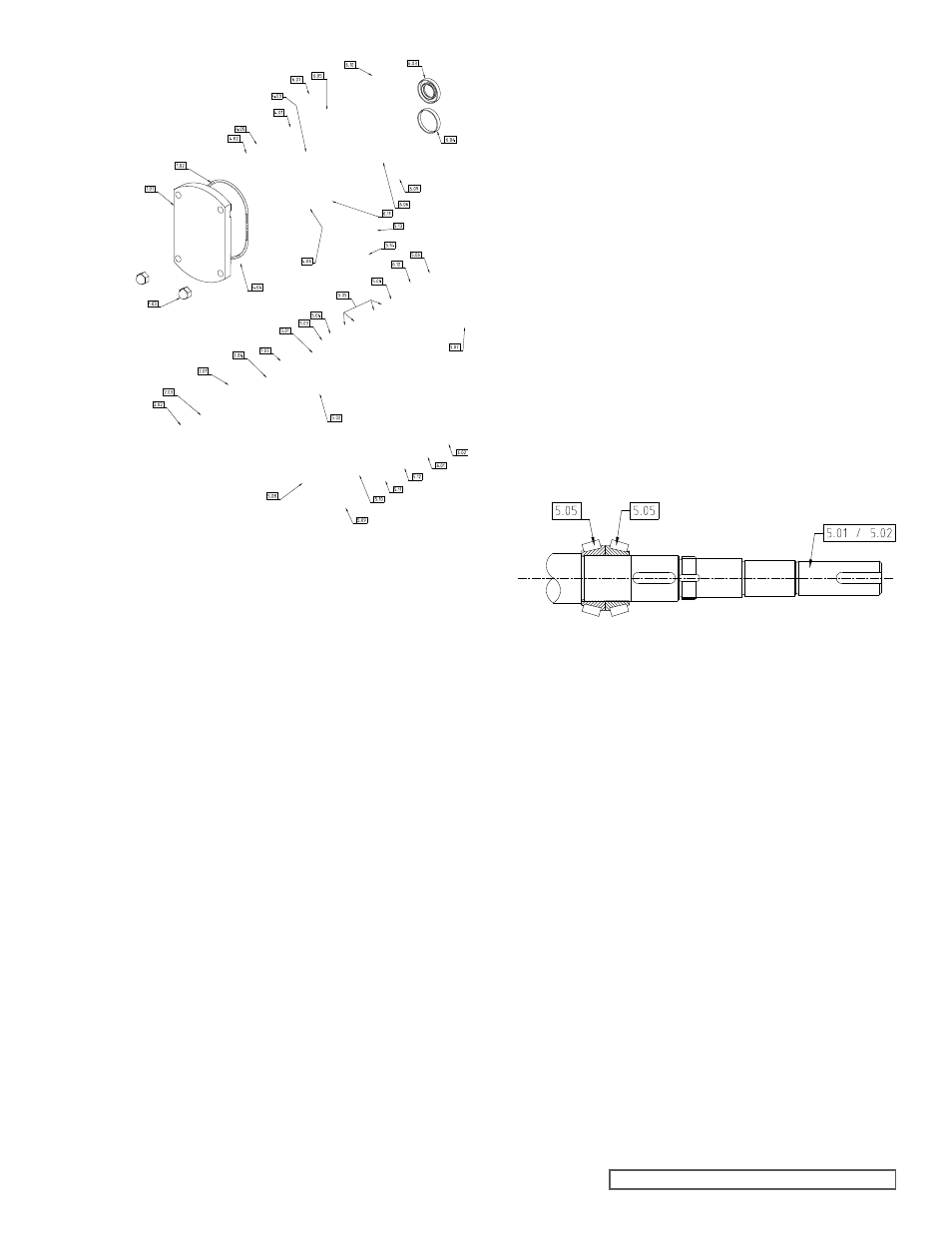
SECTION TSM 285
ISSUE
A
PAGE 15 OF 36
Before starting disassembly of the gearbox remove product
seals; refer to section 5.0 for Mechanical Seals, or section 6.0
for O-ring seals.
The following procedure describes complete disassembly of
the gearbox.
- Refer to Figure 22 for CP10; Refer to Figure 33 for CP20 and
CP30.
- Remove guard (5.06).
- Remove drive key (6.12).
- Remove oil drain plug (6.09) and breather (6.10), drain oil into
suitable container and retain if later inspection is required.
- Remove screws (6.11) and separate gearbox cover (6.00)
from bearing housing (4.01). The gearbox cover (6.00) is
located on dowels (6.06)
Note: The bearing housing (4.01) is provided with two
jacking holes (tapped M8 on CP10; M10 on CP20; M12 on
CP30), which can be used to separate the gearbox cover
(6.00) from the bearing housing (4.01).
- Remove gasket (6.05) from gearbox cover (6.00) or bearing
housing (4.01) depending upon which part the gasket is
adhered to.
- Remove oil seal (6.03) and blanking cap (6.04) from gearbox
cover (6.00).
- Remove retaining rings (6.01) from gearbox cover (6.00) and
press out bearing outer rings (6.02).
- Remove bearing inner ring (6.02) from shafts (5.01 and 5.02).
- CP10 & CP20 Pumps Only - Remove lock nuts (5.12) and
tab washers’ (5.11).
- CP30 Pumps Only – Loosen locking screws from and lock
nuts (5.12).
- Remove timing gears (5.09) and gear keys (5.10).
- CP10 Pumps Only - Remove shims (5.08) and spacers
(5.16), keep shims and spacers in sets and identify position.
- CP30 Pumps Only - Remove shims (5.08) in sets and
identify position.
- Remove screws (5.07) and retainers (5.06) from bearing
housing (4.01).
- Remove shafts (5.01 and 5.02) from bearing housing (4.01)
Shafts (5.01 and 5.02) will be complete with bearings (5.05)
and shims (5.04), keep shims in sets and identify position.
- Remove oil seals (5.03) from bearing housing (4.01).
- Remove bearing cups (5.05) and any associated shims
(5.04) from bearing housing (4.01), keep bearing cups (5.05)
and shims (5.04) in sets and identify position.
- Remove bearing cones (5.05) from shafts (5.01 and 5.02).
4.1.4 CP10, CP20 AND CP30
GEARbOX ASSEMbLy
Refer to Figure 22 for CP10 or Figure 23 for CP20 and CP30.
- Install bearing cones (5.05) to shafts (5.01 and 5.02) ensuring
they locate against shaft shoulder. The cones are installed
as shown in Figure 24.
- Install two bearing cups (5.05) to bearing housing (4.01).
- Install shafts (5.01 and 5.02) in bearing housing (4.01).
- Install remaining bearing cups (5.05), shims (5.04) to nominal
value of 0.60mm (0.024”), retainers (5.06) and secure with
screws (5.07) tightened to correct torque refer to section
8.2.
- Using a torque wrench, check the rolling torque of each
shaft assembly, referring to section 8.2. If necessary, adjust
amount of shim (5.04), either by adding shim (5.04) to
increase rolling torque or removing shim (5.04) to decrease
rolling torque, until correct rolling torque has been achieved.
If shim (5.04) is adjusted ensure screws (5.07) are tightened
to correct torque before final check of rolling torque.
- Install rotors (2.01) on to shafts (5.01 and 5.02) with rotor
retainers (2.02).
Note: The socket tool (not shown) should
always be used, the use of other tools may
damage the retainer.
- Using a depth micrometer or similar device measure any
difference (X) in rotor front face alignment, see Figure 25. If
a difference is found move shims (5.04) of thickness equal to
the difference (X) from beneath the forward rotor’s bearing
retainer (5.06) and reposition under the front bearing (5.05)
cup.
figure 24
Installation of bearing cones onto shafts
Figure 23
CP20 and CP30
Component Parts