1 setting and operating spring loaded valves, 8 integral pressure relief valves – Viking Pump TSM285: Classic+ Lobe Pump User Manual
Page 10
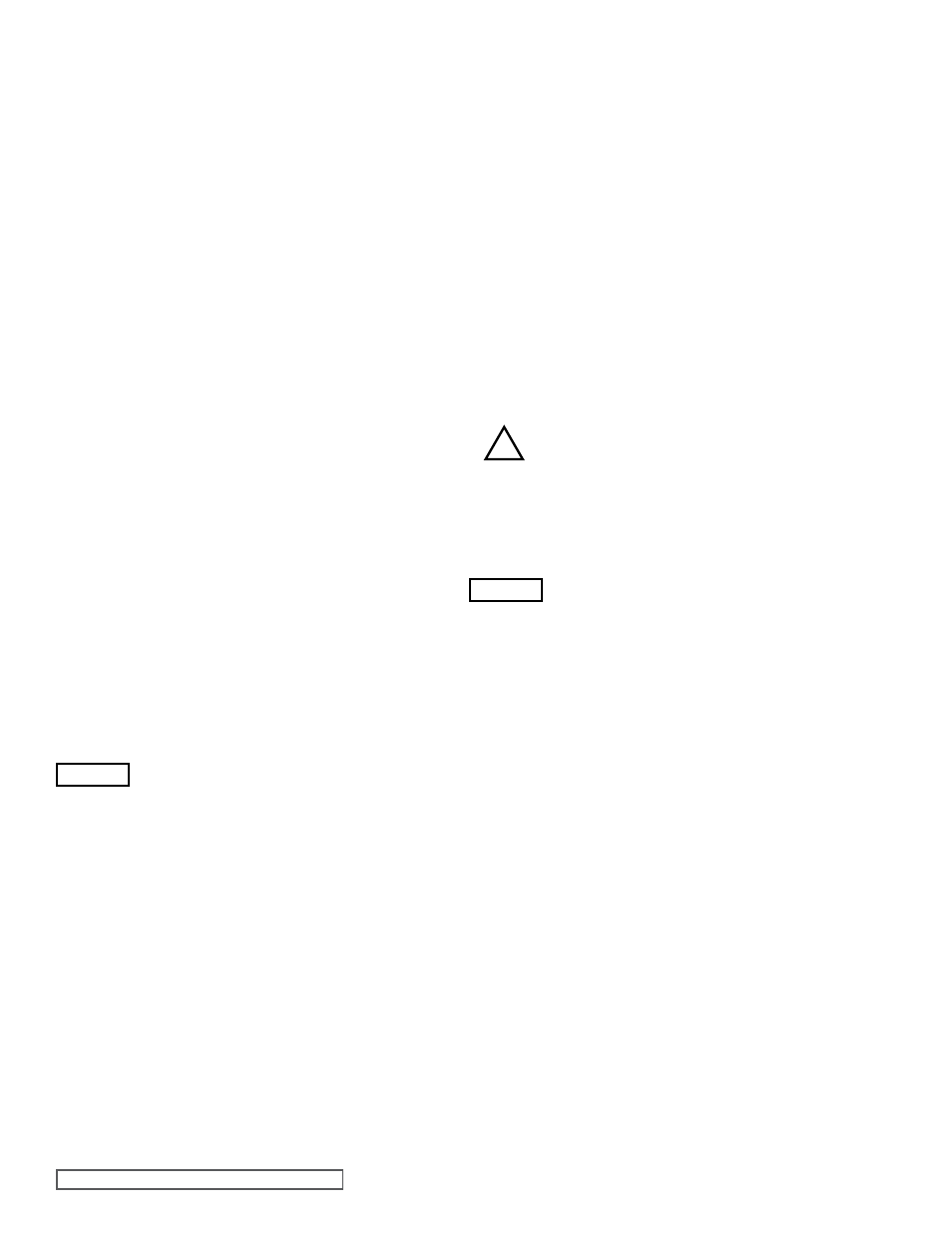
SECTION TSM 285
ISSUE
A
PAGE 10 OF 36
The selection, setting and application of integral relief valves is
influenced by the viscosity and nature of the pumped media, the
pumps operating speed and the required pressure relief setting
and mode of operation. For these reasons and to cover the
diverse range of products, the conditions under which they are
pumped and application demands, it is not practical to factory-
set integral relief. Valves and the setting of the valves should
be carried out on site, under the proposed duty conditions for
which the pump and valve were selected.
For setting and operating Classic+ integral relief valves refer
to sections 3.8.1 and 3.8.2. Before beginning the relief valve
setting procedure the pump should be installed, refer to section
3.3.1, paragraph (vi), with a pressure gauge in the discharge
line adjacent to the pump discharge port.
3.8.1 SETTING AND OPERATING
SPRING LOADED VALVES
See Figures 11, 12 and 13.
- Remove cover (108). For integral relief valve with manual lift,
see Figure 12; first remove nut (129) and hand wheel (111).
- Unscrew nut (107) using pry bar in holes
provided to relieve spring compression. For
integral relief valve with airlift, see Figure 13,
the air cylinder must be exhausted prior to
unscrewing the nut (107).
- Start pump. - refer to section 3.4.
- Screw in nut (107) using pry bar in holes provided until the
required pressure relief setting is reached.
Note: Care should be taken not to exceed the
lower of either the pump’s maximum pressure
rating or the system design pressure.
- Reinstall cover (108). For integral relief valve with manual
lift, see Figure 12; reinstall hand wheel (111) and nut (129).
- The relief valve is now set.
For Integral Relief Valve with Manual Lift - see Figure 12.
- To operate the manual lift, turn the hand wheel (111) clockwise,
which will lift the valve head (102/128). To resume normal
relief valve operation, turn the hand wheel (111) counter-
clockwise.
For Integral Relief Valve with Air Lift - see Figure 13.
- To actuate the airlift, connect an air supply not exceeding
7 Bar (102 psi) to the cylinder (123), connection ‘B’, which
will lift the valve head (112). To resume normal relief valve
operation, exhaust the cylinder (123).
3.8.2 SETTING AND OPERATING
AIR LOADED INTEGRAL
PRESSURE RELIEf VALVES
See Figure 14.
- Connect an air supply, not exceeding 7 Bar (102 psi), via
a regulating valve to the relief valve connection ‘A’ in the
cylinder (114). Do not turn on the air supply.
- Start the pump, refer to section 3.4.
- Using the regulating valve, gradually increase the air
pressure until required pressure relief setting is reached. The
air pressure must not exceed 7 Bar (102 psi).
- The relief valve is now set.
3.8 INTEGRAL PRESSURE RELIEf
VALVES
See Figures 11, 12, 13 and 14.
The Classic+ models CP10, CP20, CP30 and CP40 can be
supplied with integral pressure relief valves. For the CP10,
CP20 and CP30 both spring and air loaded versions are
available. The function of the valves can be further enhanced
with the option of manual or airlift override, offering particular
benefits where CIP or SIP procedures are employed. Valves
incorporating this option can be opened to regulate the flow
of the cleaning media through the pump chamber, thereby
avoiding the need for manual cleaning or external bypass.
Where the pump is mounted onto a portable base plate,
complete with motor and drive to be used as a mobile set, an
integral pressure relief valve should be installed.
The Classic+ integral pressure relief valves available include:
Spring Loaded - see Figure 11.
- Valve can be set to the required pressure relief setting.
Spring Loaded with Manual Lift - see Figure 12.
- Valve can be set to the required pressure relief setting.
Manual lift override can be used to open valve without
disturbing pressure relief setting.
Spring Loaded with Air Lift - see Figure 13.
- Valve can be set to the required pressure relief setting. Airlift
override, which operates on an air supply of up to 7 Bar (102
psi) depending on pressure relief setting, can be used to
open valve without disturbing pressure relief setting.
Air Loaded with Air Lift - see Figure 14.
- Valve, which operates on an air supply of up to 7 Bar (102
psi) regulated for required setting, can be set to the required
pressure relief setting. Airlift override, which operates on an
air supply of up to 7 Bar (102 psi) depending on pressure
relief setting, can be used to open valve without disturbing
pressure relief setting.
Air actuated relief valves can be operated remotely and inter-
faced with other elements of the system or process control.
Integral pressure relief valves are normally used
to protect the pump from the effects of increases
in system pressure caused, for example, by a
restricted or closed discharge line. In response
to a pressure increase, the valve opens and
internally circulates the pumped media within the
pump chamber. When the valve opens, because
the volume of liquid circulating is relatively small,
the temperature of the liquid in the pump chamber
may rise if the pump continues to operate for
an extended period. In severe cases, this may
result in temperatures in excess of the pumps
operating limits, or vaporisation of the liquid, both
of which should be avoided. For these reasons
when the valve is activated the cause of the
system pressure increase should be eliminated
as continuous operation of the pump with the
valve open is not recommended and may cause
severe damage to the pump.
If the pump on which the valve is fitted is to be installed within
either a pressurised system or one incorporating a vessel under
vacuum then the application of the valve should be referred to
Viking Pump.
!
WARNING
WARNING