Ultra-cut 400 xt – Tweco 400 XT Ultra-Cut Plasma Cutting System User Manual
Page 161
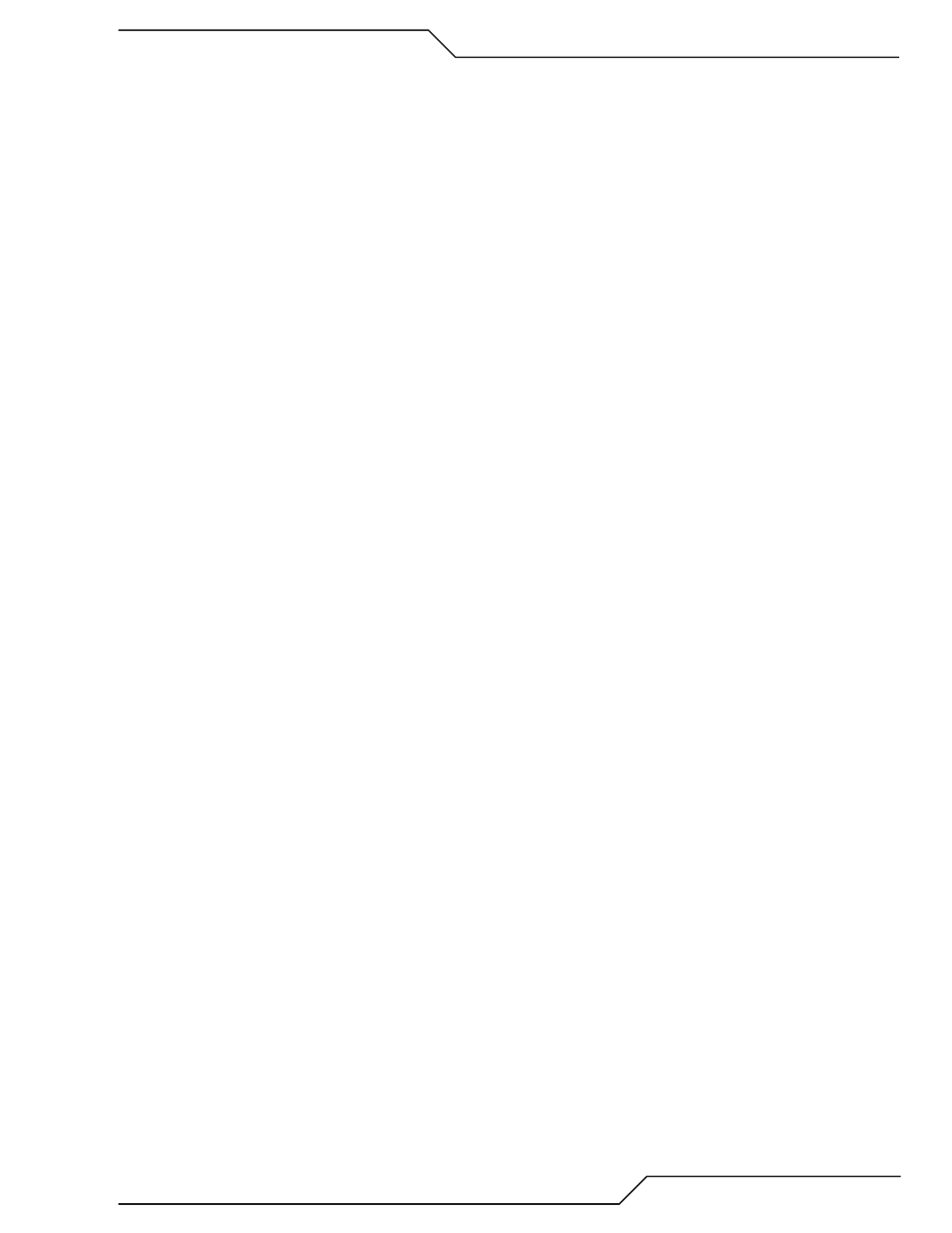
ULTRA-CUT 400 XT
Manual 0-5275
APPENDIX
A-53
• Preflow pressure/flow too low.
• Remote Analog Current Control switches set wrong can also result in lower than normal pilot current setting. See
section on these switch settings under section for code 10�.
• Defective work lead current sensor circuit. If transfer is not sensed cut current remains at the lower starting level and
pilot timer (�5 ms. or 3 sec) will time out.
107
Not Used. This is one of the reserved codes from the earlier product.
108
Tip to Electrode Voltage Fault
The Pilot voltage, measured between tip and electrode varies with different current and gas type, flow rate and consumable
design.
Once the arc is transferred the pilot switch opens leaving the tip basically floating. The voltage then is determined by how
much of a cold gas barrier surrounds the arc. Too much current or too little gas and the arc starts to contact the tip reducing
the voltage difference between tip and electrode and leading to a double arc that destroys the consumables.
The CCM measures both electrode and tip voltage and calculates the difference. If the difference between tip and electrode is
found to be less than a minimum voltage we stop cutting and set a fault for the 10� code. The normal tip to electrode voltage
is different for different processes so the min value for each process is embedded in the cut charts when using the DFC 3000
or in the CCM code if using the GCM 2010 or for Auto-Cut XT gas controls (GCM 1000XT or the built in one in the AC 200 XT).
New for the Auto-Cut XT units is a switch on the rear of the power supply that needs to be set according to the plasma gas.
If using an oxidizing gas (O2 or Air) set it as indicated for those gasses (left if AC 200 XT or up for AC300XT) or if using a
non-oxidizing gas (N2, H35 or other inert gas) set it to the right or down as indicated for those gas types.. This switch adjusts
the range of voltage for the gas type to better protect the torch. A wrong setting could result in false setting of the 10� code.
During piloting and ramping (the time from transfer until the current reaches full cut current), we lower the allowed tip to
electrode voltage to about �0% of that allowed during cutting because the current is lower and the gas flow is lower during
that time.
Causes for 10� code:
• Gas Flow/pressure too low for consumable parts being used.
o If gas source pressure is not well regulated it is possible pressure may be OK at times and drop too low at other
times such as during a cut.
o A leak of the preflow/plasma gas after the pressure/flow control (GCM 2010, DPC, GCM 1000 XT) can reduce the
pressure/flow to the torch because some if it is bypassing the torch, while seeming to have enough pressure/flow
at the gas control.
• Cut current set too high for consumable parts being used.
• With DFC 3000 a faulty component would be expected to set a fault code in either the DPC or DMC. However, if a
wrong process is selected which doesn’t match the consumable type or if using a custom process where pressure
has been set too low or current too high that could cause 10� without setting any faults in the DFC 3000.
• A broken pilot wire in the torch lead making intermittent contact can allow piloting or sometimes the torch can transfer
using only HF (high frequency). This intermittent connection will upset the tip voltage measurement and can result in
the 10� code. Symptom is - it may cut for a short time then fault. Check for an open/broken torch lead pilot wire.
• Physically shorted torch body between anode (tip) and cathode (electrode).
The fault resulting in a 10� code is measured while cutting. It is more likely a shorted torch body, depending on the resistance
of the short, it will set code 20� (Unwanted Current) as that is measured prior to starting cut However, it must be considered
as a last resort.
109
Part Process not Configured.
This represents a status, not a fault. This is used with the DFC 3000 only. It means the operator hasn’t loaded the cutting
process from either the TSC 3000 or from the program embedded in the cutting table CNC controller. The solution is to load
a process. The code will continue to be displayed until the CNC Start is applied at which time the code will clear.
110
Not Used. This is one of the reserved codes from the earlier product.