Powers 595 Series 11 Self-Operating Temperature Regulators - Type CD Composition Disc User Manual
Page 14
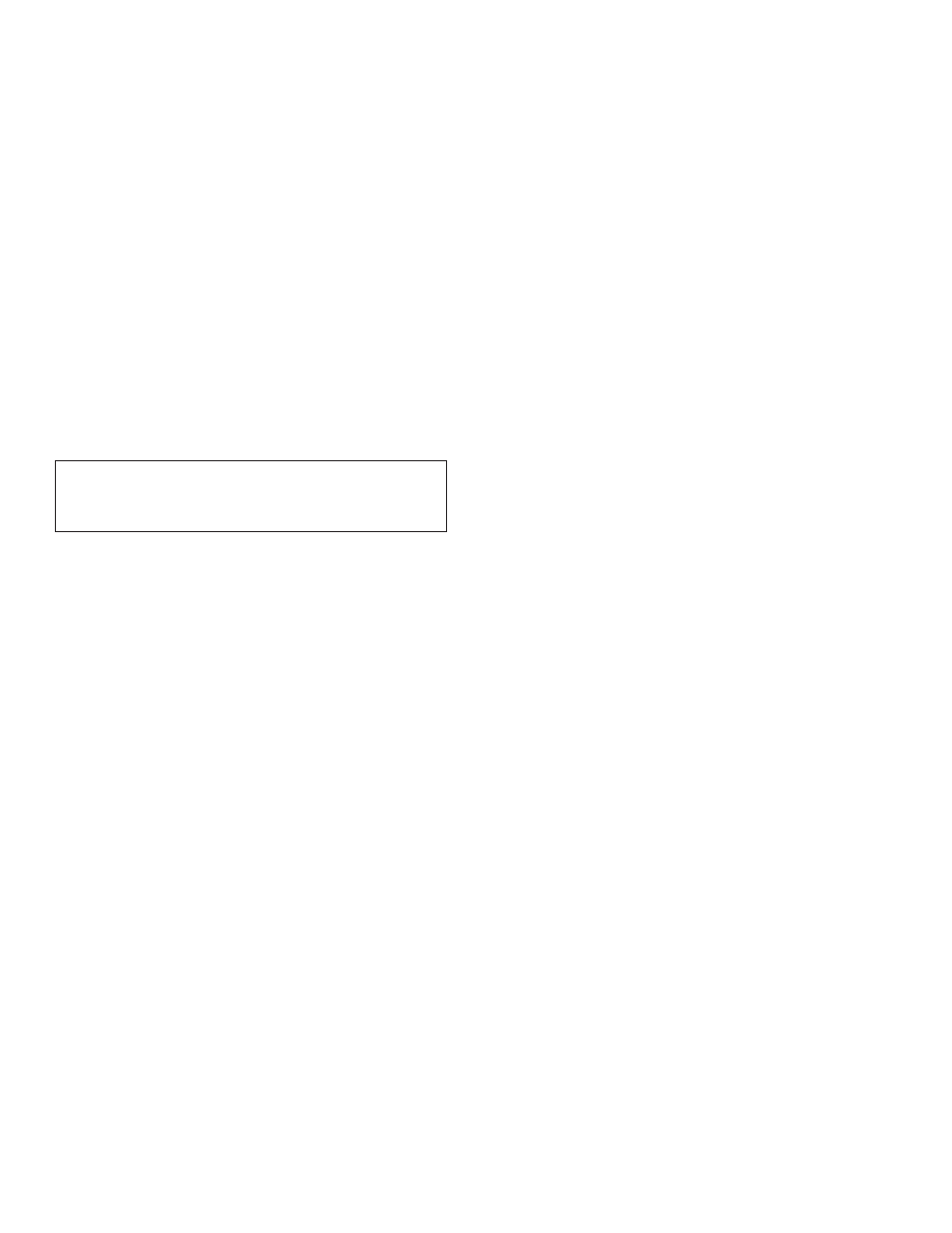
Preventive Maintenance
■
Once every three months, inspect the Regulator
as follows:
1. Visually check for leaks from the valve body joints, piping-to-
valve connections, packing and stem areas
2. Visually check for excessive corrosion on the regulator,
including the bellows, capillary, bulb, thermal system legs,
bridge, and yoke. Also check for excessive corrosion on the
valve body.
3. Perform the instructions in Testing the Thermal System Less
than full valve travel may indicate a leak in the bellows, capil-
lary, or bulb, or other problems.This may result in excessive
temperature in the process.
4. Test the temperature adjusting nut assembly for freedom of
movement (see Adjust Set Point for instructions).
5. Remove bulb form the process fl uid and check for excessive
corrosion, or erosion that may weaken the bulb and/or cause
thermal system failure.
Troubleshooting
■
WARNING: Failure of the thermal system will result in a
constant rise in temperature (or constant high tempera-
ture) of the fl uid which you are trying to control.
• Erratic temperature control (valve cycles too hot/too cold)
1. Valve sized incorrectly. Verify valve selection.
2. Regulator is controlling at incorrect set point. Refer to Adjust
Set Point.
3. Bulb is poorly positioned and/or oriented, and will not control
the actual temperature of the heating/cooling medium. Refer
to Install Bulb.
4. Incorrect type of bulb is being used. See Table on page 11.
5. The valve stem is sticking. Lubricate the stem.
6. The valve stem is bent. Refer to Maintenance for disassem-
bly instructions and replace.
7. Packing gland assembly too tight. Loosen packing
gland nut [14].
8. Faulty or incorrect steam traps. Replace with correct
steam trap.
9. Very wet steam. Install a high pressure steam trap just ahead of
the valve to drain off condensate that collects in the steam line.
• Regulator Does Not Shut Off
1. Pressure differential is greater than allowable pressure drop.
Refer to Water Capacities and Steam Capacities tables.
2. Disc is worn. Replace disc (refer to Maintenance).
3. Foreign material between the disc and the valve plug seat.
Refer to Replace only the composition disc for disassembly.
Clean.
4. Bulb is poorly positioned and/or oriented, and will not control
the actual temperature of the heating/cooling medium. Refer
to Install Bulb.
5. Incorrect type of bulb is being used. See Table on page 11.
6. Valve sized incorrectly, causing wire drawing and leakage.
Refer to Sizing Information.
7. Packing gland assembly is too tight, locking valve stem.
Loosen packing gland assembly and lubricate if desired.
8. Bent valve stem; need to replace. Refer to Maintenance
for disassembly.
9. Thermal system failure. Refer to Testing the Thermal System.
10. Temperature adjusting nut assembly raised too high. Refer to
Adjust Set Point.
• Valve "chatters"
1. Regulator installed with the fl ow of the control medium in
reverse of arrow direction on valve body.
2. Pressure differential too high, refer to Tables on pages 3 and
4 for correct pressure differential range.
3. Trapped condensate in line. Install a steam trap just ahead
of the regulator to drain off condensate that collects in the
steam line.
• Constant rise in process fl uid temperature
1. A constant rise in temperature may indicate the thermal sys-
tem is leaking charge and/or the valve has failed in a partially
or fully open position. This would allow a constant fl ow of
heating medium, which would overheat the fl uid which you
are trying to control.
14