Encoder power, Encoder phasing, Encoder power -26 encoder phasing -26 – Rockwell Automation 8720MC High Performance Drives Installation Manual User Manual
Page 60
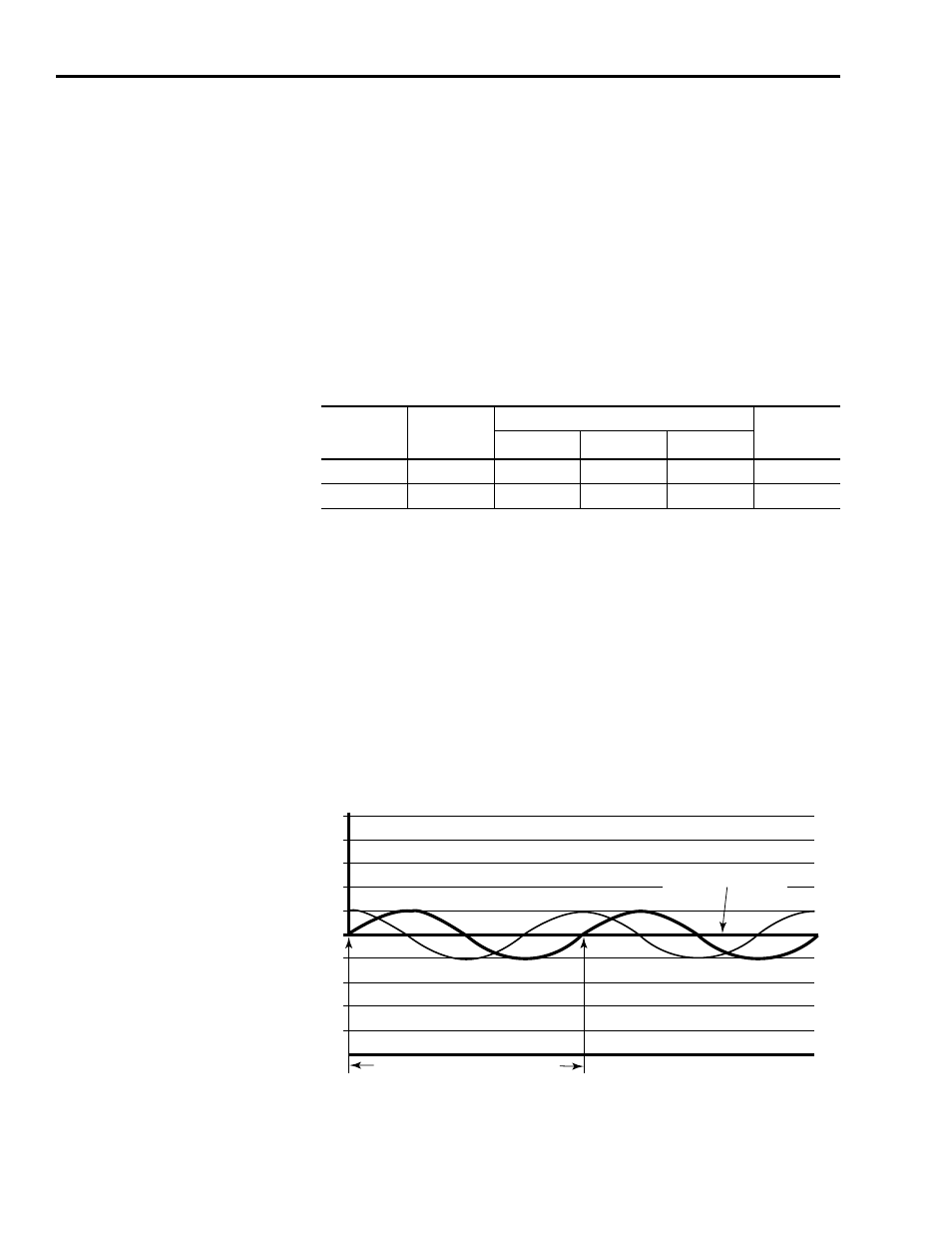
Publication 8720MC-IN001D-EN-P — December 2002
2-26
8720MC Connector Data
Encoder Power
The motor and auxiliary feedback port connector (P1) provides
terminals for both 5V dc and 9V dc encoder power. The encoder
voltage used is determined by the feedback device selected (refer to
the table on page 2-23 for a list of feedback devices and their required
input voltages). The standard 8720SM and MP-Series (460V) motor
Stegmann feedback devices use 9V dc encoder power. A total of 300
mA of 5V dc encoder current is shared between the two 5V dc
encoder power terminals, P1-7 and P1-20. In a like manner, a total of
300 mA of 9V dc encoder current is shared between the two 9V dc
encoder power terminals, P1-6 and P1-19. Refer to 8720MC Connector
Pin-outs beginning on page 2-4.
Encoder Phasing
The 8720MC feedback interface supports standard one volt
peak-to-peak sine/cosine devices and AquadB square wave encoders.
The feedback choice is a software configuration option. Figure 2.20
shows the one volt peak-to-peak sine or cosine wave ride on a 2.5V
dc offset voltage supplied by a Stegmann encoder.
Figure 2.20
Sinusoidal Encoder Signals, SRS-660, SNS-60 and SRM-60
Supply
Reference
Voltage
Maximum
Current
mA
Minimum
Nominal
Maximum
+5V dc
EPWR_5V
5.0
5.25
5.5
300
+9V dc
EPWR_9V
8.3
9.1
9.9
300
5
4.5
4
3.5
3
2.5
2
1.5
1
0.5
0
Volts
1 cycle = 360 deg/512 or 1024
SIN
COS
REFSIN, REFCOS
Signal variation with a clockwise shaft rotation looking at the shaft end