Specifications, Installation requirements – Rockwell Automation 1336_F_E_T_S SERIES A CHOPPER BRAKE MODULE User Manual
Page 24
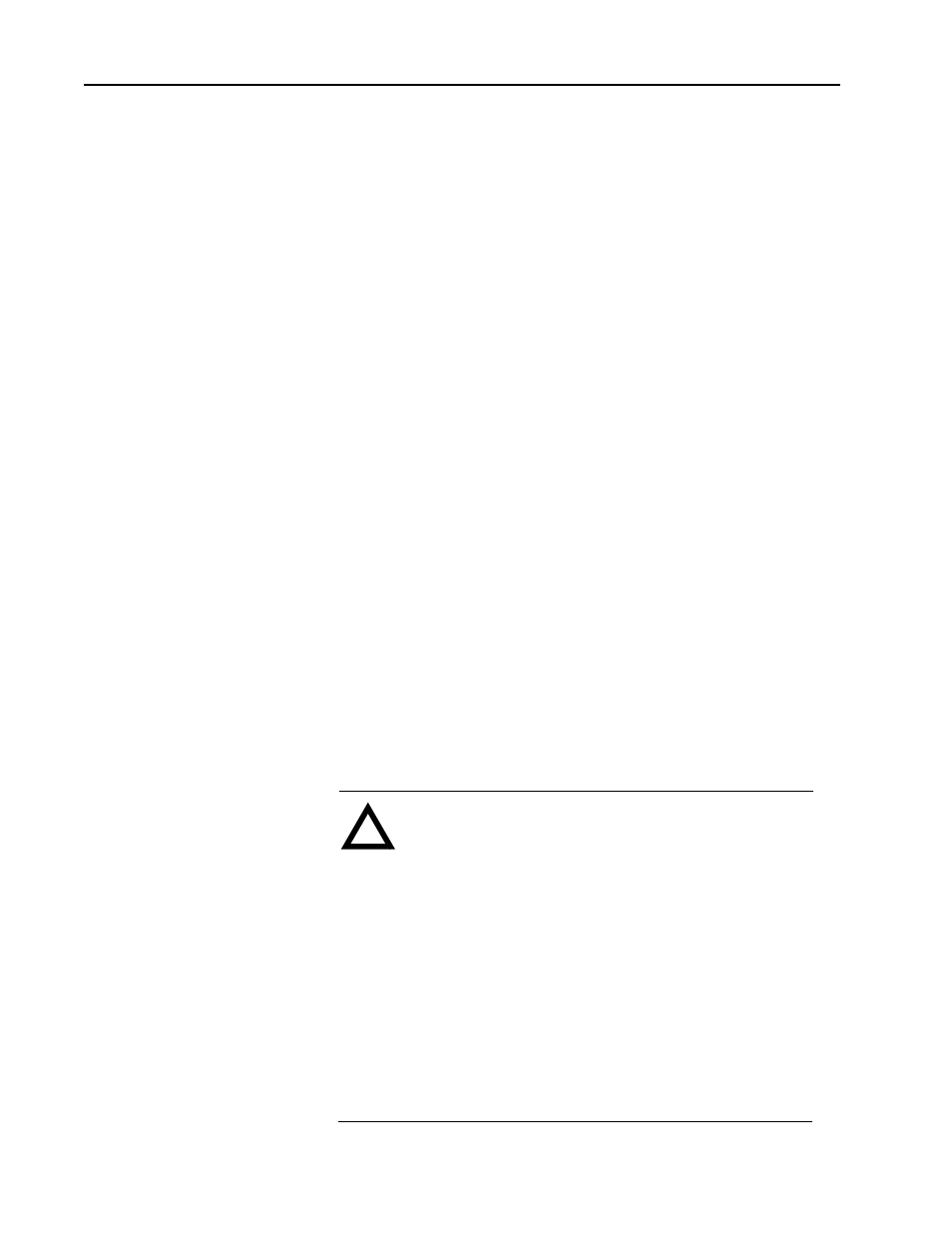
Heavy Duty Dynamic Braking
24
1336-5.65 — March, 2007
Specifications
1
Watts Dissipated at 100% (Continuous Duty Cycle) are approximately equal to the average watts
dissipated at 20 and 50% Duty Cycles.
Installation Requirements
Braking Torque
&
Duty Cycle
(Refer to pages 5-10)
Input Power
DC power supplied from DC Bus.
Brake Fault
Contact
(1) N.C. contact, TTL compatible, closed when power is applied to the
brake module, open when a brake fault or loss of power occurs.
UL/CSA Rating:
1.0 Amps, 125VAC.
1.0 Amps, 110VAC.
2.0 Amps, 30VDC.
CE Certification: Low Voltage EN 60204-1.
PREN 50178.
Initial Contact Resistance: 100mOhms maximum.
Operating
Temperature
Chopper: -10
°C to 40°C (14°F to 104°F).
Resistors: -10
°C to 50°C (14°F to 122°F).
Storage
Temperature
Chopper: -40
°C to 70°C (-40°F to 158°F).
Resistors: -40
°C to 70°C (-40°F to 158°F).
Humidity
5% to 95% non-condensing.
Atmosphere
Noncorrosive/nonhazardous dust, vapor or gas.
Altitude Derating
1,000 meters (3,300 feet) maximum without derating.
Enclosure Type
IP00 (Open)
Watts Dissipated
1
WA018, WB009, WC009:75W at 100% Duty Cycle
WA070, WB035, WC035:115W at 100% Duty Cycle
WA115, WB110, WC085:190W at 100% Duty Cycle
Minimum
Brake Resistance
WA018 = 9.0 Ohms
WB009 = 37.0 Ohms WC009 = 46.0 Ohms
WA070 = 2.5 Ohms
WB035 = 9.0 Ohms
WC035 = 15.5 Ohms
WA115 = 1.25 Ohms WB110 = 2.5 Ohms
WC085 = 3.0 Ohms
ATTENTION: Electric Shock can cause injury or death.
Remove all power before working on this product.
For all chopper module ratings, DC brake power is supplied
from the drive DC Bus.
Hazards of electrical shock exist if accidental contact is made
with parts carrying bus voltage. A DC power indicator on the
brake enclosures provides visual indication that bus voltage
is present. Before proceeding with any installation or
troubleshooting activity, allow at least one minute after input
power has been removed for the bus circuit to discharge. Bus
voltage should be verified by using a voltmeter to measure
the voltage between the +DC and -DC terminals on the drive
power terminal block. Do not attempt any servicing until the
DC power indicating light has extinguished and bus voltage
has been verified to be zero volts.
!