Control and signal wiring – Rockwell Automation 23C PowerFlex 400 AC Drive Packages for Fan & Pump Apps User Manual
Page 15
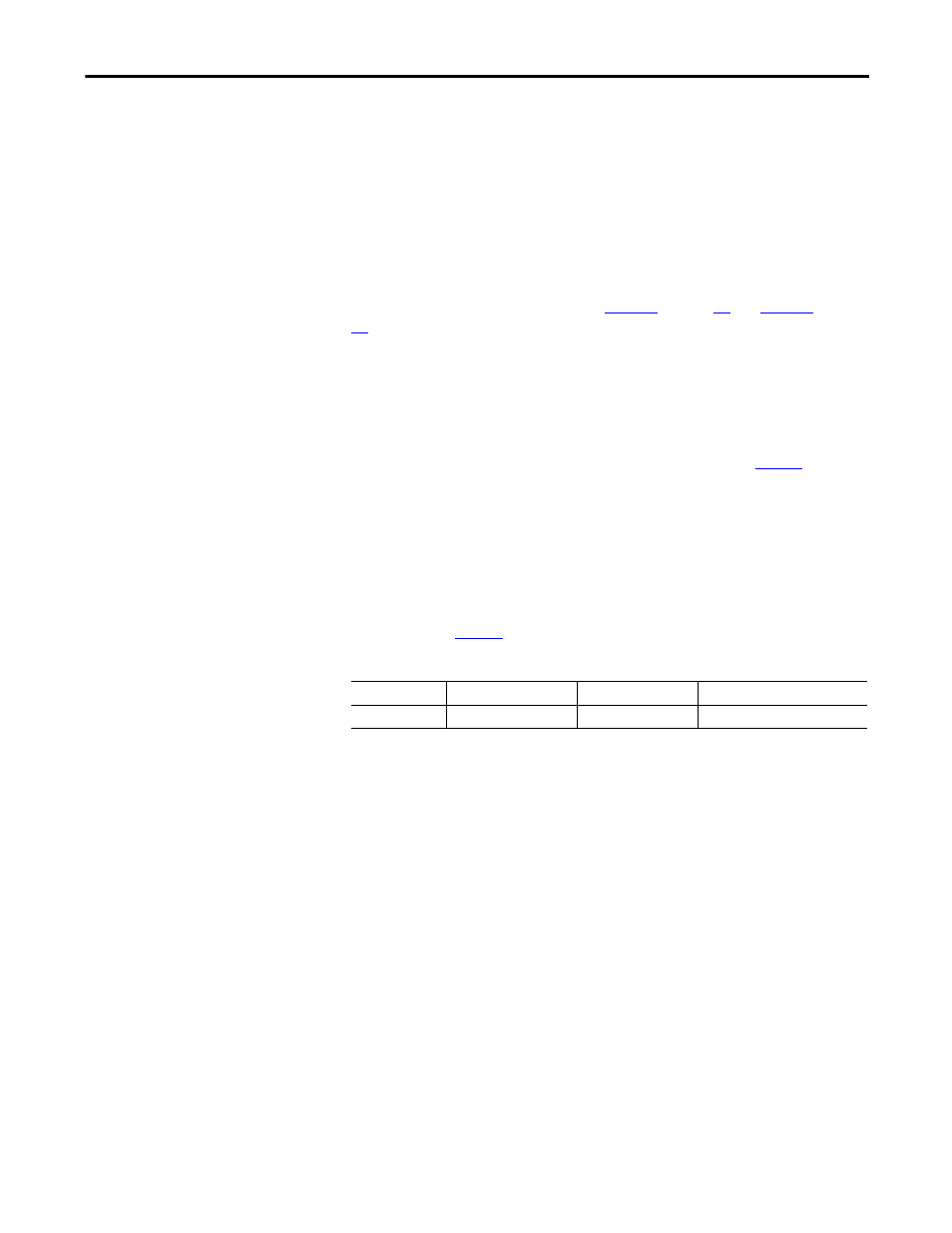
Rockwell Automation Publication 23C-IN001B-EN-P - June 2013
15
Main Input Disconnect Package (Style A/M)
Chapter 1
Control and Signal Wiring
Refer to the PowerFlex 400 User Manual for additional detailed information
about control and signal wiring.
The Control I/O Terminal Block (TB1) and Relay Terminal Block (TB2)
located on the drive Main Control Board provide terminals for interfacing
customer supplied control inputs and outputs. All analog and discrete control
wiring will be made at these terminals. Typical customer control and signal wiring
is shown on the Interconnect Drawings
on page
and
on page
To connect control and signal wiring to the drive package:
❏
1. Wire the control and signal leads by routing them according to the drive
option type. Note that you must punch openings in the option cabinet of
the desired conduit size, following NEC and all applicable local codes and
standards. I/O terminal block specifications are listed in
.
Control and signal wires should be separated from power wires by at least
0.3 meters (1 foot).
❏
2. Connect the control and signal wiring to the I/O terminals located on the
drive.
❏
3. Tighten the I/O terminals to the proper torque according to drive type as
Table 4 - I/O Terminal Block Specifications
Voltage Rating
Maximum Wire Size
(1)
(1) Maximum/minimum sizes that the terminal block will accept - these are not recommendations.
Minimum Wire Size
Torque
208…460V AC
1.3 mm
2
(16 AWG)
0.13 mm
2
(26 AWG)
0.5…0.8 N•m (4.4…7 lb•in)