General information – Multiquip WRS5200DFPU (KUBOTA WG972-GL-E3 DUAL FUEL) User Manual
Page 21
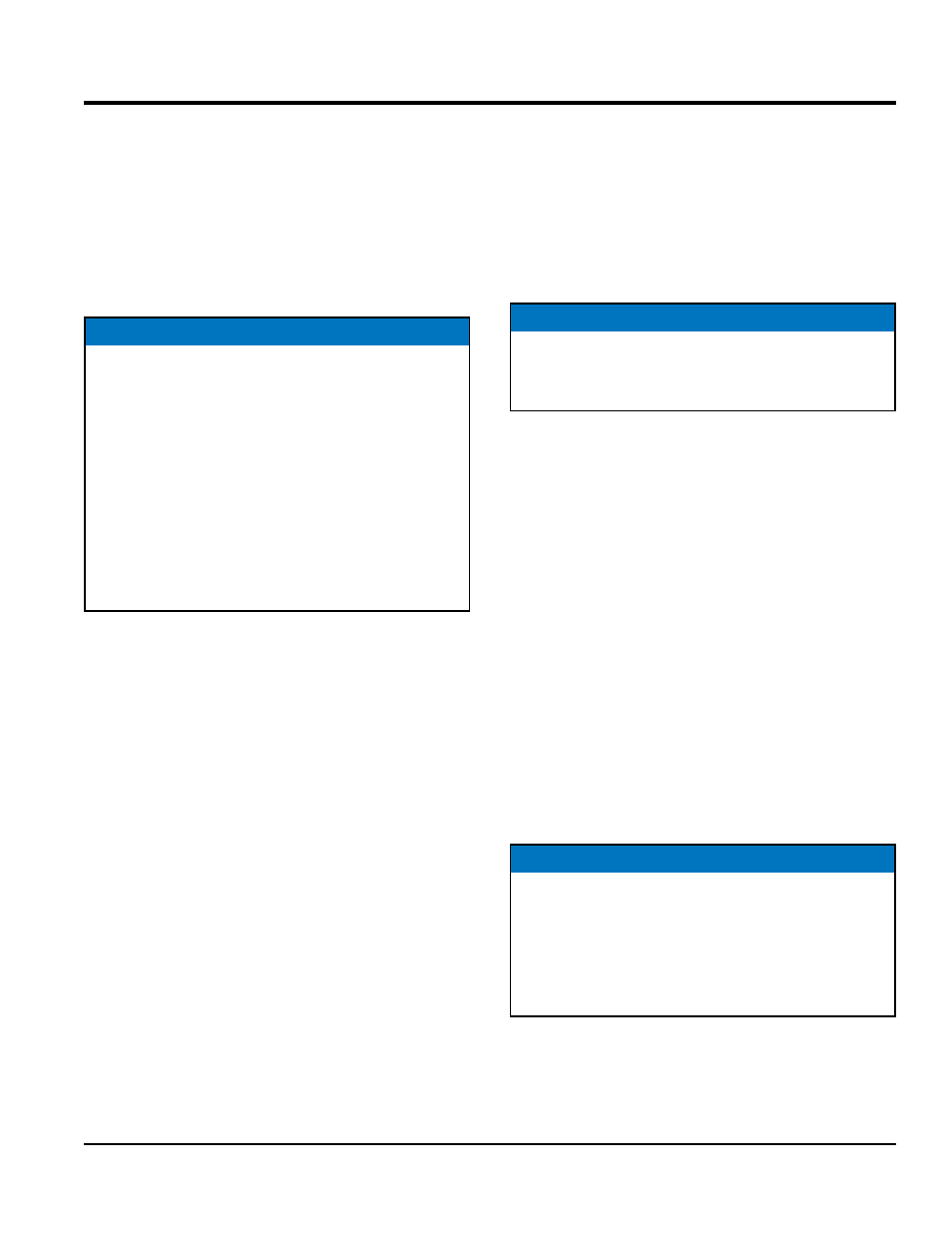
wrs5200dfpu hYdrauLIC roLLer sCreed • operatIon manuaL — rev. #0 (08/18/14) — page 21
general information
Form Specifications
Inadequate substrate and form support can lead to form
failure causing unnecessary job delays and expenses while
contributing to poor floor flatness and floor levelness ratings.
The intent of the form specifications is to establish minimum
guidelines to help the contractor choose the most
economical and effective formwork/support system for the
job application.
subgrade/deck forms
Subgrade must be sound enough to support slab edge
forms and bracing as well as the load imposed by the
screed and its support. Potential deflections, as in the case
with metal and plywood decks, should be considered when
determining brace and support spacing.
Soil substrates must be well compacted and must be able
to support bearing pressures greater than or equal to those
imposed by the screed supports and the slab forming.
For proper bearing support, shims should be used to
adequately distribute loads where grade is not level or
is soft. Use standard ACI concrete form pressures when
calculating lateral loads on slab edge forms.
NOTICE
It is recommended that at least the day prior to the
concrete pour, a dry run be accomplished to test the
load capacity of the forms and substrate. Proper job
planning is essential to a successful application.
The WRS5200 Super Screed weighs approximately
4000 lbs. (1,814 kg.) at a maximum length of 52 ft.
(16 meters). This works out to be 2000 lbs. (907 kg.)
per side.
Any screed support (forms, rails supports and
substrate) must withstand a 2000 lbs. (907 kg.) point
load at a 2:1 safety factor.
Wood Forms
Wood forms are not a preferred method of scree support.
Because of the concentrated bearing loads by the screed,
wood is not a good support material. Nominal 2 X 1-1/2
No. 2 Douglas Fir is calculated to support a maximum of
1000 lbs. (453 kg.). The grain could crush and splinter
causing level variations and potential failure. 4 X 3-1/2
lumber for edge form should be acceptable
Screed Rails
Screed rails and supports, independent of slab edge
forming is the preferred method. Due to strength, deflection
and traction considerations, 2.5" X 2.5" X.1875 (3/16-inch)
wall structural steel tubing with adjustable supports spaced
as shown in Figure (8).
Standard deflection with 3/16-inch wall tubing thickness for
the above reference configuration is 1/16-inch for every 3
ft. (1.2 meters). Refer to standard material charts for other
configurations.
Steel Forms
Paving forms with 90° lip-edge at bottom with stake pockets
is preferred. If soft or unleveled subgrade is encountered,
a bearing pad and/or shims should be used under the steel
forms for additional bearing support. Depending on slab
thickness and subgrade, forms may require diagonal
bracing.
NOTICE
Check with city and state civil engineering regulations
regarding the type and size of lumber used for edge
forms.
NOTICE
These recommended form and rail specifications
are provided to illustrate the application and are not
intended to supersede or replace any city or state civil
engineering procedures and or specifications. Multiquip
will not be responsible for the improper application of
the WRS5200 Ride-On Roller Screed.