5 profibus, Profibus, 4system description – Lenze Controller-based Automation User Manual
Page 40
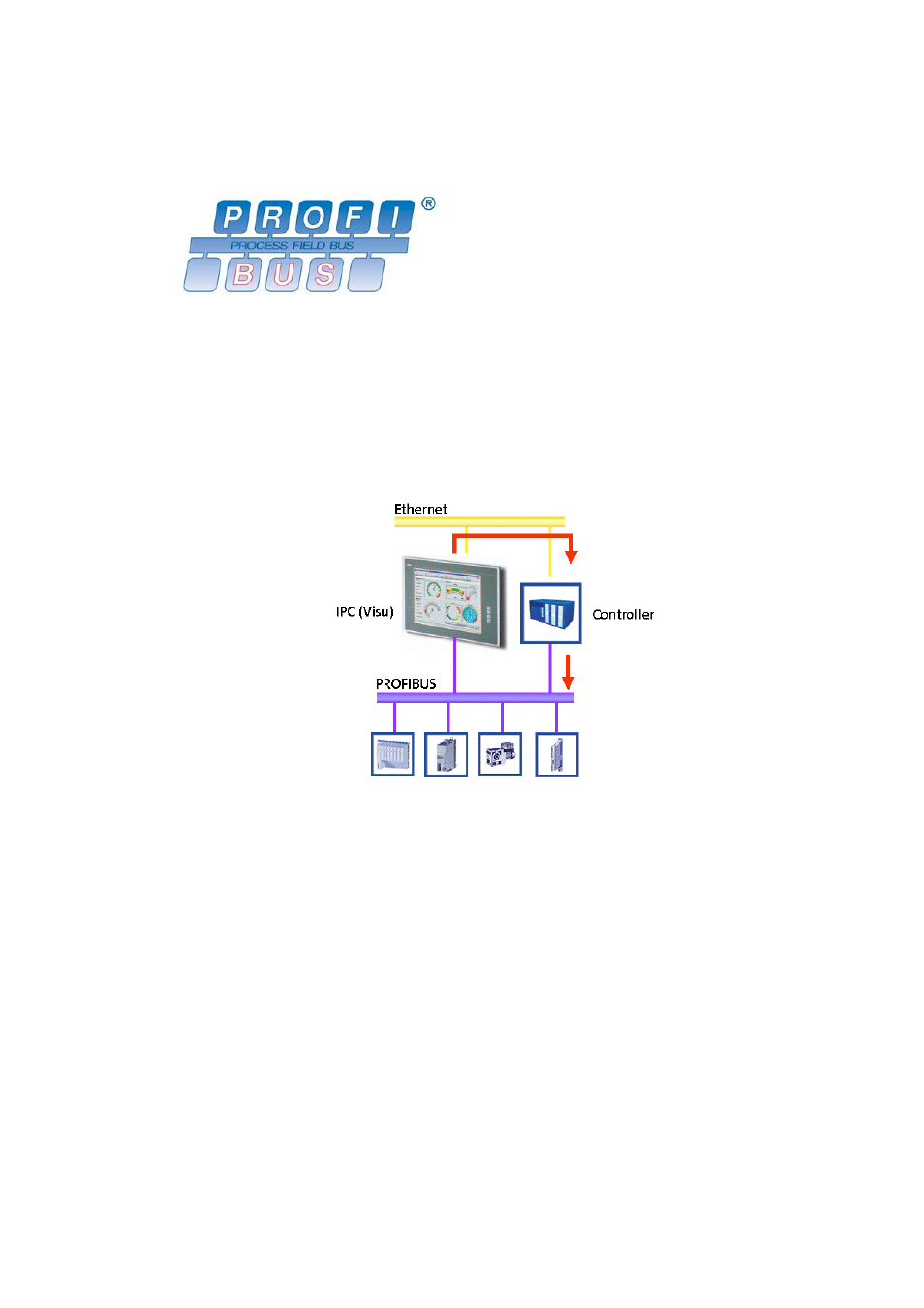
4
System description
4.3
Network topologies
40
Lenze · Controller-based Automation - Visualisation · System Manual · DMS 1.5 EN · 04/2014 · TD17
_ _ _ _ _ _ _ _ _ _ _ _ _ _ _ _ _ _ _ _ _ _ _ _ _ _ _ _ _ _ _ _ _ _ _ _ _ _ _ _ _ _ _ _ _ _ _ _ _ _ _ _ _ _ _ _ _ _ _ _ _ _ _ _
4.3.5
PROFIBUS®
Visualisation applications with PROFIBUS are available for the following Lenze devices:
• HMI series EL 100
• Industrial PCs: EL 1800-9800, CS 5800-9800 and CPC 2800
The Industrial PCs use an OPC server for communication.
• Cabinet Controller 3231 C/3241 C (with an external monitor panel/display)
• Panel Controller p300/p500
Under Windows® CE, a direct driver is provided for communication.
The connection of the visualisation to PROFIBUS makes use of the properties that the MPI protocol
is "tunnelled" on PROFIBUS and the connection of an MPI node to PROFIBUS is identical as regards
the hardware. Thus a direct connection to a Siemens S7 control is possible without logging on a
separate PROFIBUS node in the control configuration.
For this purpose, the Industrial PCs are equipped with a communication card (MC-MPI), whereas the
interface is already available on-board for the EL 100 with the MPI variant.
To facilitate the creation of an application in »VisiWinNET®«, the variables can be imported from an
S7-PLC program. Communication drivers are available for all runtime systems.
Functions
• Access to Siemens S7-300/400 control systems via PROFIBUS (MPI)
• Access to other controls via Ethernet if an OPC server or »VisiWinNET®« direct driver is available.
• Visualisation variables can be imported from STEP 7®.