Rejection of a splice and its causes – ERICO CADWELD for Rebar Splicing System User Manual
Page 12
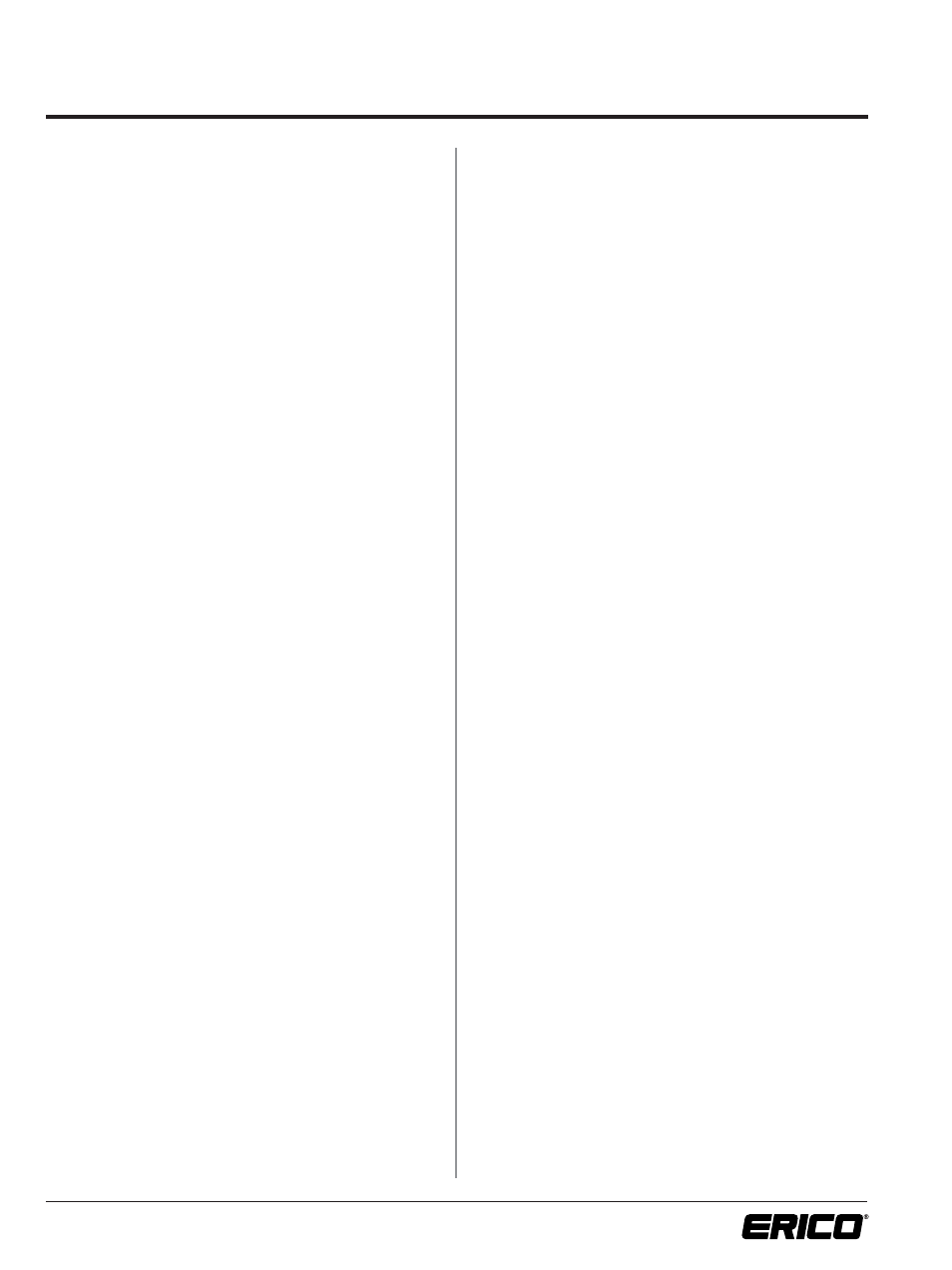
10
www.erico.com
Rejection Of A Splice And Its Causes
Improper Fill
Filler metal not visible at ends of sleeve –
See “Void Limits.”
1. Filler metal leakage due to faulty use of packing or
misalignment of equipment.
2. Excessive gap between the ends of the rebars or
between the rebar end and the plate or structure to
which a B-Series splice sleeve is welded. (Requires more
filler metal to fill this space.)
3. Use of a smaller cartridge than called for or use of only
part of the correct cartridge due to spillage when loading.
4. Undersize rebar requiring more filler metal to completely
fill the sleeve. (Check the latest ASTM specification.)
5. Packing forced into the sleeve beyond the acceptable
void limits.
6. If rebars are not clean and dry, gas or steam will be
generated by the heat of the molten filler metal. This
gas or steam can cause a blowout or general porosity
and produce voids.
7. Improper placement of rebar ends in sleeve causing
blockage of incoming filler metal at the Tap Hole.
8. Inadequate venting of Splice Sleeve. For vertical splices
refer to Splice Kit Sheet for proper length of top packing
(approximately 1-1/4 wrap around top bar). See page 8
for recommended venting procedures on horizontal
splices.
9. Sound splices often have pin holes, shrinkage fissures
and cold joints. These are usually visible at the ends of
completed splices and are not cause for rejection.
Slag at Taphole
1. Omission of Steel Disk at bottom of Crucible.
2. Any one or more of items 1, 2, 3, and 4 under
“Improper Fill.”
NOTE: When checking for filler metal at the sleeve Tap
Hole, you cannot rely on color alone. When a hot
riser is broken off, the exposed filler metal will
oxidize almost immediately and discolor. If there is
any doubt as to whether filler metal or slag is present
in the Tap Hole, use a coarse file, prick punch or
hammer to test. Filler metal will shine while slag will
remain dull and crumble. Breaking off the riser may
pull metal out of the sleeve Tap Hole. This should
not be construed as an unfilled Tap Hole and is not
cause for rejection.
Blowouts indicate that the cleaning practice
for rebar ends should be reviewed
Power wire brushing and torch drying (as called for in
standard instructions “Rebar Cleaning Procedure”) will help
eliminate blowouts and severe voids.
Blowouts also can be caused by Splice Sleeves and other
equipment being damp. This most commonly occurs when
material is left out overnight or in the rain.